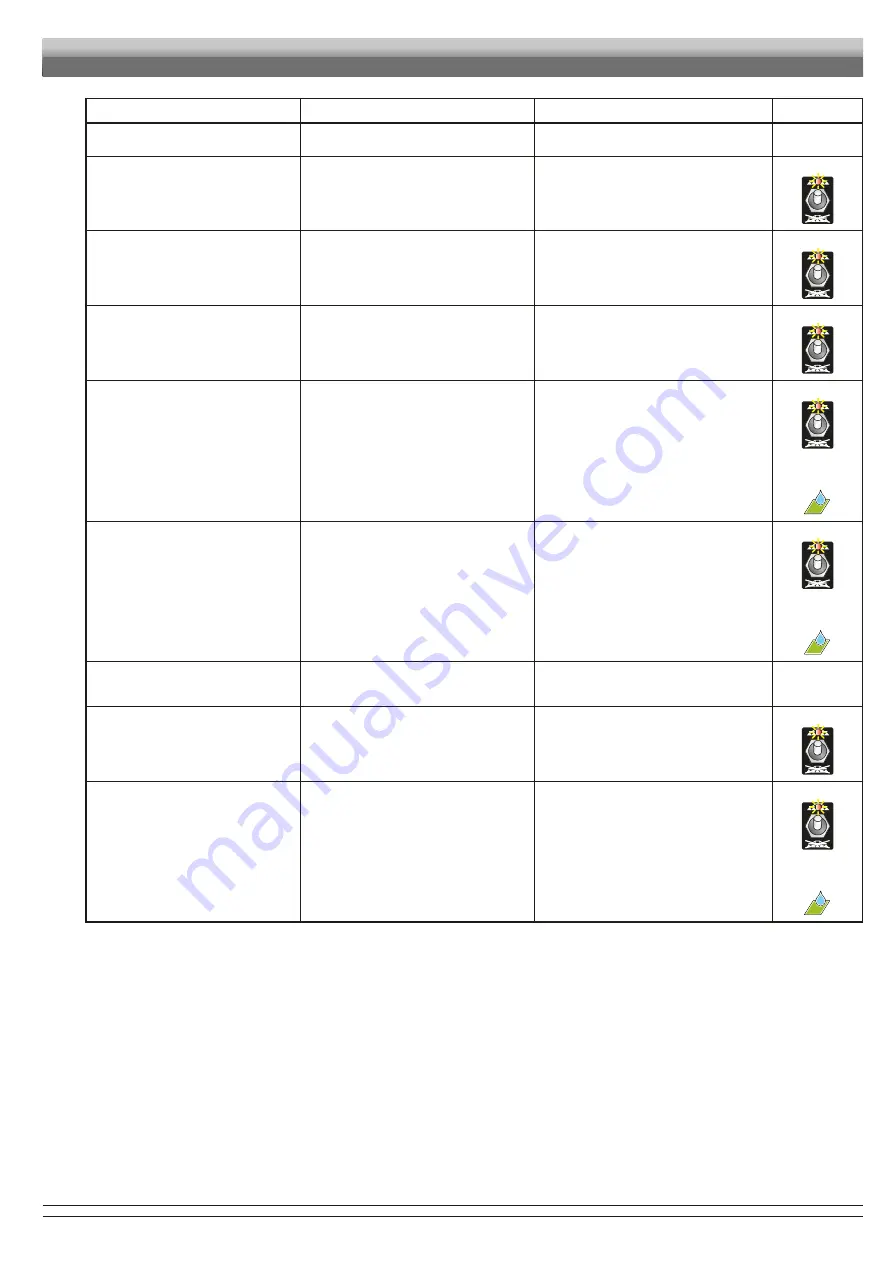
117
MESSAGE ON DISPLAY
CAUSE
REMEDY
JOB MODE
Invalid signal of the pressure sensor!
Signal from pressure sensor is out of allowed
range
• Check the sensor and connection cable (and
connector) status
(par. 6.6)
--
Decelerate!
Pressure too high
The pressure exceeds the maximum level
allowed for the nozzle being used
• Decrease driving speed
• Adjust the operating pressure so as to respect
the previously set limits for nozzles in use.
• Check set maximum pressure for nozzles in use
(par. 10.1.7)
Master ON
Accelerate!
Insufficient pressure
The pressure does not reach the minimum value
for the nozzle in use
• Increase driving speed
• Adjust the operating pressure so as to respect
the previously set limits for nozzles in use.
• Check set minimum pressure for nozzle in use
(par. 10.1.7)
Master ON
Flowmeter out of range!
Rate out of the limits allowed by flowmeter
• Modify working conditions to suit flowmeter limits
(speed, pressure, etc.)
• Make sure that flowmeter parameters are set
correctly
(par. 10.1.3)
Master ON
Decelerate!
Insufficient flowrate
Flowrate does not reach the value requested
for output
• Decrease driving speed
• Make sure that flowmeter parameters are set
correctly
(par. 10.1.3)
Master ON
+
Automatic
adjustment ON
Accelerate!
Too high flowrate
The flowrate exceeds the value required for
output
• Increase driving speed
• Make sure that settings in the
Implement
advanced settings
menu (boom width,
flowmeter, etc.
chap. 10.1
) are set correctly
Master ON
+
Automatic
adjustment ON
Reduce rotation speed!
RPM exceeds the maximum set value
• Decrease the rotation speed of the moving part
• Check the constant set for the rev counter
(par. 10.1.9)
--
Increase rotation speed!
RPM does not reach the minimum value
• Increase the rotation speed of the moving part
• Check the constant set for the rev counter
(par. 10.1.9)
Master ON
Check nozzles wear status!
Difference between measured and calculated
flowrate (according to selected nozzle data)
higher than set value
• Check that the set nozzle coincides with the one
installed on the boom
(par. 10.1.1)
• Replace nozzles
Master ON
+
Automatic
adjustment ON
CONTINUES
MAINTENANCE / DIAGNOSTICS / REPAIRS