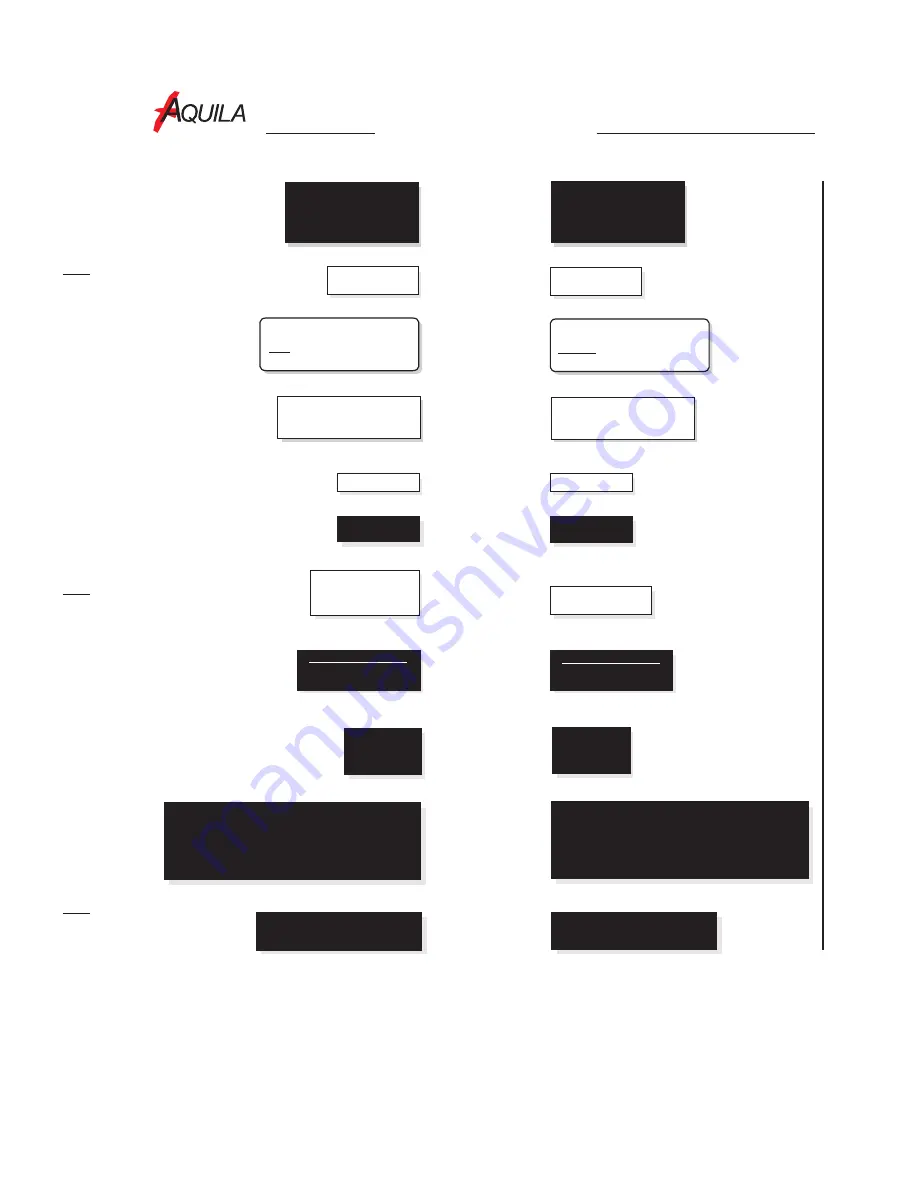
MAINTENANCE MANUAL
AQUILA AT01
Aviation by Excellence AG
11-30-00
Page 206
Placards and Markings
Interior Placards and Markings
Figure 201 (Sheet 6 of 7)
KÜHLMITTEL-
AUSGLEICHGEFÄSS
NICHT ÖFFNEN
COOLANT
DO NOT OPEN
STECKDOSE
12 - 14 V
Max. 8A
RECEPTACLE
12 - 14 V DC
Max. 8A
Z
Detail-
A1
Detail-
B1
Detail-
C1
Detail-
KÜHLMITTEL
COOLANT
X
Detail-
Detail-
Y
Detail-
Detail-
W
Detail-
Detail-
ÖLFÜLLUNG 3,0 Liter
SIEHE FLUGHANDBUCH
OIL CAPACITY 3,0 (l)
REFER to POH
HYD. BRAKE
FLUID (
FLUID 4)
HYDRAULIKÖL
FLUID 4
T
Detail-
Detail-
U
Detail-
Detail-
V
Detail-
Detail-
GEPÄCK max. 40 KG
NUR MIT
VERZURRUNG
BAGGAGE MAX: 40 KG
SECURELY
ANCHORE DOWN
! ACHTUNG !
Kein Flugmotorenöl einfüllen.
Siehe Flughandbuch
! CAUTION !
DO NOT use aviation grade oil
Refer to POH
ELT-REMOTE-CONTROL
Zur Aktivierung den Hauptschalter
des ELT auf ARMED stellen!
ELT-REMOTE-CONTROL
To activate switch transmitter
to ARMED!
Das Flugzeug ist für den Betrieb unter VFR-Tag
ohne Vereisungsbedingungen zugelassen. Alle
Kunstflugmanöver, einschließlich beabsichtigtem
Trudeln, sind verboten. Weitere Betriebsgrenzen
stehen im Flughandbuch.
The aircraft is certified for VFR flights on day,
outside of icing conditions.
No aerobatic
maneuvers, including spins are approved. For
further operating limitations refer to POH.
Amperemeter
Ammeter
Note: Placards illustrated not in scale.
D1
Detail-
MANÖVERGESCHWINDIGKEIT
V =112 kts
A
MANEUVERING SPEED
V =112 kts
A
30.04.08
Summary of Contents for ATO1
Page 2: ...MAINTENANCE MANUAL AQUILA AT01 Aviation by Excellence AG ...
Page 12: ...MAINTENANCE MANUAL AQUILA AT01 Aviation by Excellence AG Introduction ...
Page 16: ...MAINTENANCE MANUAL AQUILA AT01 Aviation by Excellence AG ...
Page 18: ...MAINTENANCE MANUAL AQUILA AT01 Aviation by Excellence AG ...
Page 20: ...MAINTENANCE MANUAL AQUILA AT01 Aviation by Excellence AG ...
Page 38: ...MAINTENANCE MANUAL AQUILA AT01 Aviation by Excellence AG ...
Page 42: ...MAINTENANCE MANUAL AQUILA AT01 Aviation by Excellence AG ...
Page 44: ...MAINTENANCE MANUAL AQUILA AT01 Aviation by Excellence AG ...
Page 46: ...MAINTENANCE MANUAL AQUILA AT01 Aviation by Excellence AG ...
Page 48: ...MAINTENANCE MANUAL AQUILA AT01 Aviation by Excellence AG ...
Page 52: ...MAINTENANCE MANUAL AQUILA AT01 Aviation by Excellence AG ...
Page 54: ...MAINTENANCE MANUAL AQUILA AT01 Aviation by Excellence AG ...
Page 55: ...MAINTENANCE MANUAL AQUILA AT01 Aviation by Excellence AG CHAPTER 11 PLACARDS AND MARKINGS ...
Page 56: ...MAINTENANCE MANUAL AQUILA AT01 Aviation by Excellence AG ...
Page 58: ...MAINTENANCE MANUAL AQUILA AT01 Aviation by Excellence AG ...
Page 60: ...MAINTENANCE MANUAL AQUILA AT01 Aviation by Excellence AG ...
Page 75: ...MAINTENANCE MANUAL AQUILA AT01 Aviation by Excellence AG CHAPTER 23 COMMUNICATIONS ...
Page 76: ...MAINTENANCE MANUAL AQUILA AT01 Aviation by Excellence AG ...
Page 78: ...MAINTENANCE MANUAL AQUILA AT01 Aviation by Excellence AG ...
Page 80: ...MAINTENANCE MANUAL AQUILA AT01 Aviation by Excellence AG ...
Page 88: ...MAINTENANCE MANUAL AQUILA AT01 Aviation by Excellence AG ...
Page 90: ...MAINTENANCE MANUAL AQUILA AT01 Aviation by Excellence AG ...
Page 94: ...MAINTENANCE MANUAL AQUILA AT01 Aviation by Excellence AG ...
Page 102: ...MAINTENANCE MANUAL AQUILA AT01 Aviation by Excellence AG ...
Page 104: ...MAINTENANCE MANUAL AQUILA AT01 Aviation by Excellence AG ...
Page 106: ...MAINTENANCE MANUAL AQUILA AT01 Aviation by Excellence AG ...
Page 116: ...MAINTENANCE MANUAL AQUILA AT01 Aviation by Excellence AG ...
Page 117: ...MAINTENANCE MANUAL AQUILA AT01 Aviation by Excellence AG CHAPTER 34 NAVIGATION ...
Page 118: ...MAINTENANCE MANUAL AQUILA AT01 Aviation by Excellence AG ...
Page 122: ...MAINTENANCE MANUAL AQUILA AT01 Aviation by Excellence AG ...
Page 128: ...MAINTENANCE MANUAL AQUILA AT01 Aviation by Excellence AG ...
Page 130: ...MAINTENANCE MANUAL AQUILA AT01 Aviation by Excellence AG ...
Page 132: ...MAINTENANCE MANUAL AQUILA AT01 Aviation by Excellence AG ...
Page 140: ...MAINTENANCE MANUAL AQUILA AT01 Aviation by Excellence AG ...
Page 152: ...MAINTENANCE MANUAL AQUILA AT01 Aviation by Excellence AG ...
Page 158: ...MAINTENANCE MANUAL AQUILA AT01 Aviation by Excellence AG ...
Page 159: ...MAINTENANCE MANUAL AQUILA AT01 Aviation by Excellence AG CHAPTER 52 DOORS ...
Page 160: ...MAINTENANCE MANUAL AQUILA AT01 Aviation by Excellence AG ...
Page 162: ...MAINTENANCE MANUAL AQUILA AT01 Aviation by Excellence AG ...
Page 164: ...MAINTENANCE MANUAL AQUILA AT01 Aviation by Excellence AG ...
Page 168: ...MAINTENANCE MANUAL AQUILA AT01 Aviation by Excellence AG ...
Page 170: ...MAINTENANCE MANUAL AQUILA AT01 Aviation by Excellence AG ...
Page 172: ...MAINTENANCE MANUAL AQUILA AT01 Aviation by Excellence AG ...
Page 198: ...MAINTENANCE MANUAL AQUILA AT01 Aviation by Excellence AG Charts and Diagrams ...