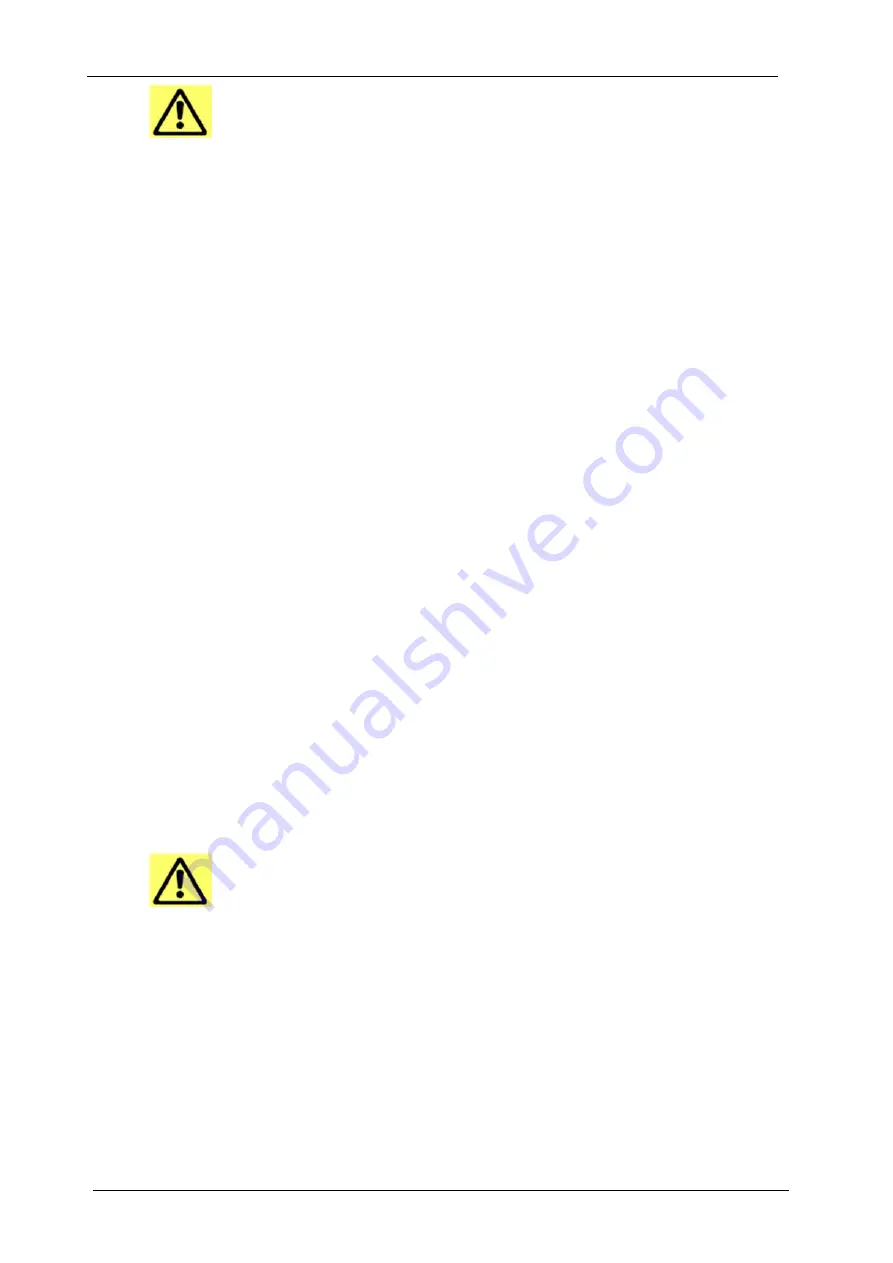
MINIPACK
X:/Aquatech-Pressmain Instruction manuals/current/MINIPACK
5
0.1 WARNINGS
0.1.1
Do not touch any live parts for at least 5 minutes after switching off the electricity supply. Failure to
observe this will constitute a severe Electric shock and/or Burns hazard and may be lethal.
0.1.2
The equipment is only suitable for earth referenced supplies and must be permanently earthed to avoid
Electric shock hazard.
0.1.3
With equipment isolator OFF, mains voltage may still be present from BMS system. This constitutes an
Electric shock hazard.
0.1.4
Emergency stop button does not remove dangerous voltages from control panel/pump motor
assemblies. This constitutes an Electric shock hazard.
0.1.5
Metal parts (e.g. heat sinks) may reach temperatures of 90 degrees centigrade and will constitute a Burns
hazard.
0.1.6
Some equipment is designed to operate with liquid temperatures up to 150 degrees centigrade and will
constitute a Burns/scalding hazard.
0.1.7
The equipment must not be pressurised beyond the maximum working pressure as stated on
pumps/pipework/vessels/control panel otherwise serious mechanical damage/destruction could occur
causing injury to people or property.
0.1.8
The equipment must not be heated/chilled beyond the maximum/minimum working temperature as
stated on pumps/pipework/vessels/control panel otherwise serious mechanical damage/destruction
could occur causing injury to people or property.
0.1.9
Any damage to equipment, pumpset, vessels, pipework or system components caused by misapplication,
mishandling or misuse could lead to Electric shock hazard, Burns hazard, Fire hazard, Flooding hazard or
cause injury to people or property.
0.1.10
This equipment may contain moving/rotating parts that must remain guarded. Removal of or missing
guards could lead to serious personal injury.
0.1.11
Pressure vessels must never be disassembled whilst in use, they contain high pressure air/gas charge
which could cause injury to people or property.
0.1.12
Pump motors with lifting eyes; the lifting eyes are only suitable for lifting motors NOT the entire pump
assembly. This could cause injury to people or property.
0.1.13
Ensure the base/foundation/plinth/wall to which the equipment is to be attached is sufficiently strong
enough to carry the entire mass of the equipment including the water that it will contain under worst-
case fault conditions. E.g. fully saturated pressure vessel with no air charge, break tank full to
overflowing, etc. Failure to observe this could cause serious mechanical damage/destruction resulting in
injury to people or property.
0.1.14
This equipment contains a fluid which may under certain circumstances leak/drip/spray fluid (e.g.
servicing, repair or malfunction). Ensure any fluid discharge will not cause damage to the surroundings by
taking appropriate action. E.g. install in a place that will not be damaged by leakage or install in a bunded
area with adequate drainage.
0.2
CAUTIONS FOR INSTALLATION
0.2.1
READ GENERAL SAFETY INFORMATION 0.0, WARNINGS 0.1 and CAUTIONS 0.2, 0.3 & 0.4
0.2.2
The unit should only be installed/operated by a competent person;
A competent person is someone who is
technically competent and familiar with safety practices and the hazards involved.
0.2.3
Do not lift the pumpset by pipework. Lift the pumpset by the container pallet using a pallet/forklift or crane
by passing strops underneath the skid using a spreader bar. Failure to utilise these facilities will result in
damage to the pumpset.
0.2.4
Store in a dry place to avoid damp conditions deteriorating the equipment.
0.2.5
Protect against dirt, damage and frost. It is absolutely essential that no foreign matter such as pipe thread
swarf, welding slag, grit or stones are allowed to enter the set. Debris of this type can cause severe damage
to the mechanical seals, diaphragms and impeller. Frost/freezing will damage pumps/pipework and control
panel components.
0.2.6
The equipment is only suitable for installation in a clean, dust free indoor environment, with adequate
protection from heat and frost, and sufficient ventilation to ensure cooling of the motors. Ambient air