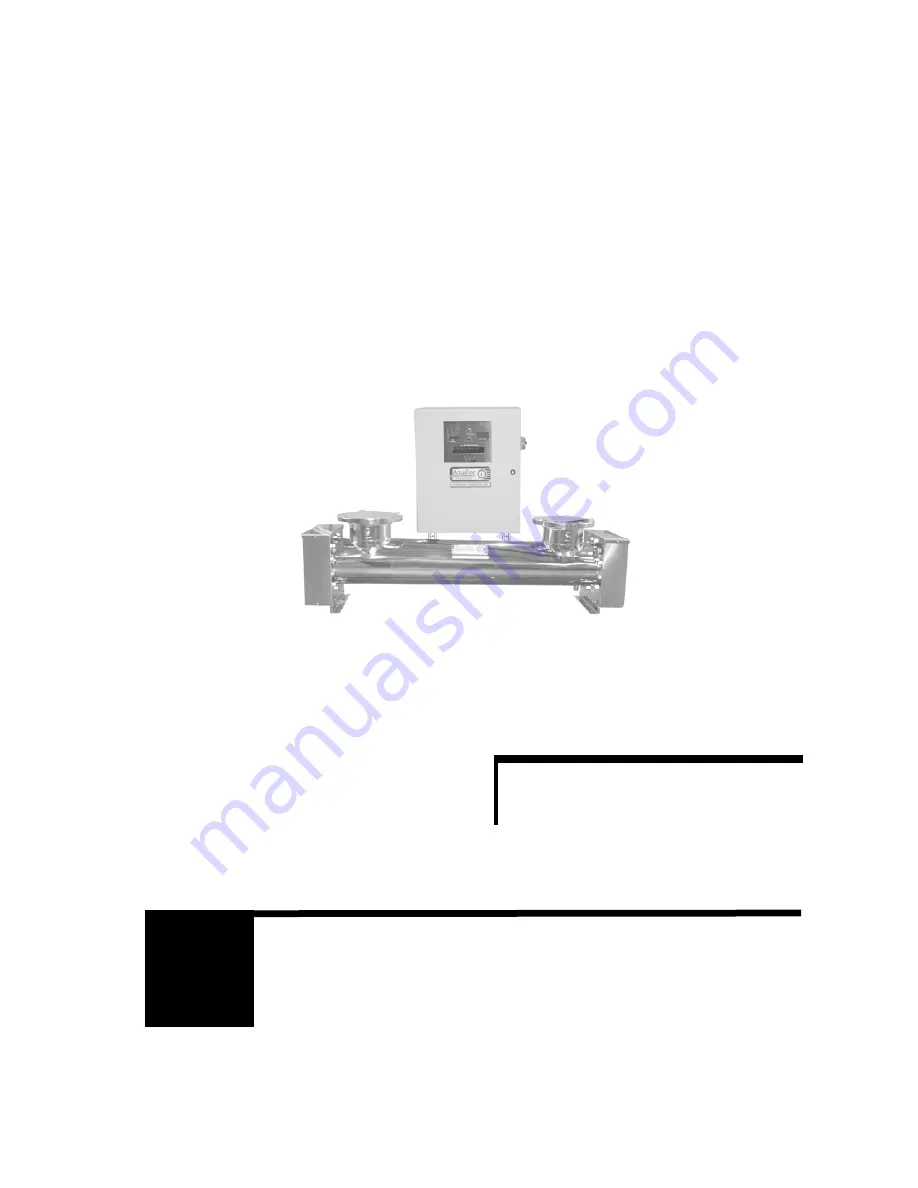
1
READ THIS MANUAL
PLEASE KEEP FOR PERMANENT REFERENCE
Part No. 120, Rev. 6.0 10/04
This manual covers the installation, operation and general maintenance
requirements for Aquafine Ultraviolet Water Treatment Equipment.
Disinfection
It is imperative that those responsible for the installation of this
equipment, as well as operating personnel, read this manual and
carefully follow all instructions and guidelines
. EQUIPMENT
OPERATORS AND INSTALLERS MUST COMPLY WITH
OPERATIONAL SAFETY REQUIREMENTS.
SAFETY
ISSUE
O
O
p
p
t
t
i
i
m
m
a
a
H
H
X
X
&
&
O
O
p
p
t
t
i
i
m
m
a
a
H
H
X
X
-
-
U
U
S
S
e
e
r
r
i
i
e
e
s
s
I
I
n
n
s
s
t
t
a
a
l
l
l
l
a
a
t
t
i
i
o
o
n
n
a
a
n
n
d
d
O
O
p
p
e
e
r
r
a
a
t
t
i
i
o
o
n
n
M
M
a
a
n
n
u
u
a
a
l
l
1.800.423.3015
(outside California and within domestic USA)
email:
web:
www.aquafineuv.com
Optima HX
Summary of Contents for optima hx series
Page 44: ...44 ...