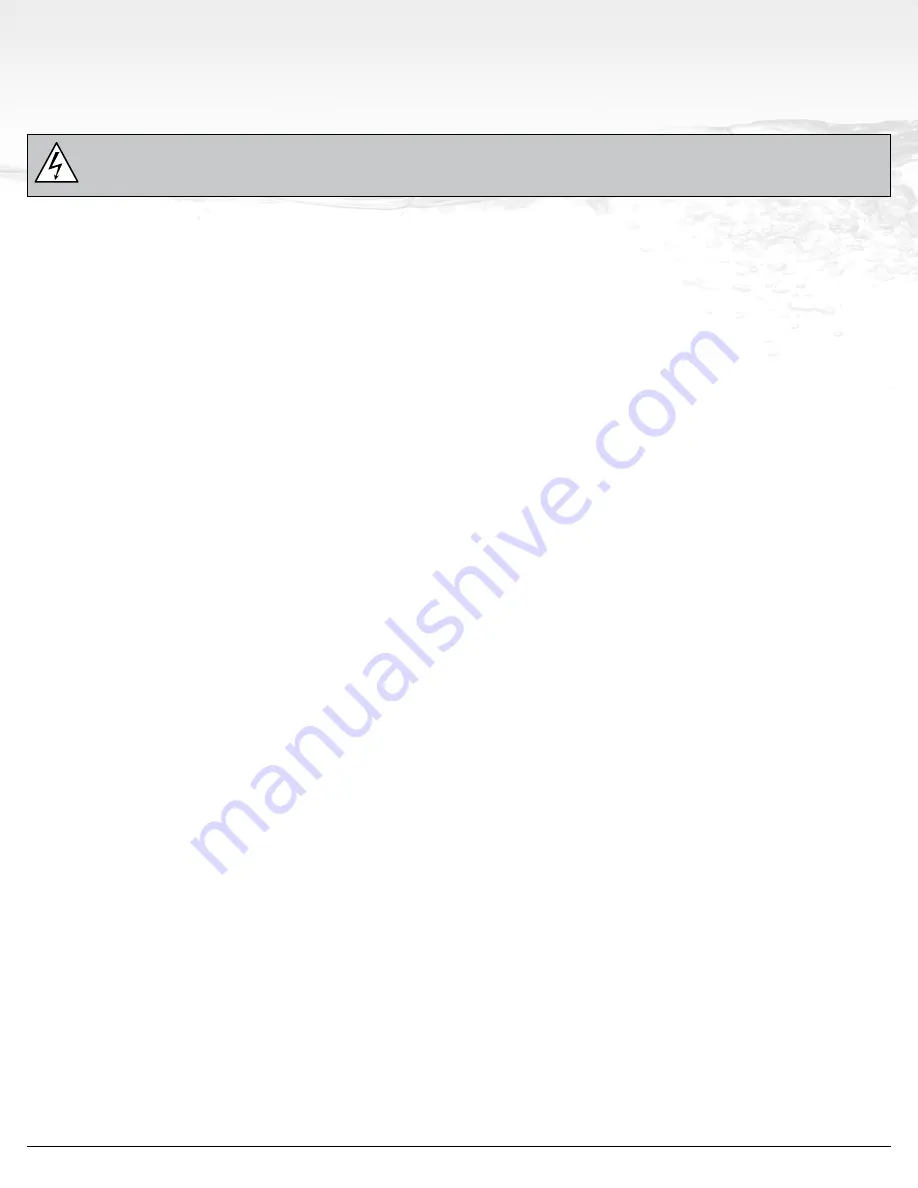
23
www.AquaProducts.com/Service
7. DOES NOT CLEAN ENTIRE POOL (MISSES AREAS) OR DOES NOT CLIMB WALLS
A. Make sure cleaner climbs walls up to the waterline and moves left or right before reversing. Lateral waterline
movement is not required by models with permanently fixed Handles, no Handles or with Handle Floats. See
pages 5-6, FLOATING HANDLE. See also pages 11-13, CLEANING PATTERNS.
B. Floating Handle should be locked at an angle across the unit’s body, and be sure that no water is present in
the Floating Handle. If water is present, please visit Aqua Products’ Customer Service Department online at
AquaProducts.com/Service
to locate your local Authorized Service Center.
C. Clean Filter Bag thoroughly (See page 14).
D. Install Flotation to help the cleaner climb (See page 15).
E. Operate the cleaner several cycles (up to 7 hours depending upon model), each time locking the Floating
Handle in opposite directions (not applicable to models with permanently fixed or no handles) and starting
the cleaner in different areas of the pool. You may also adjust the programs with the Magnet. See page 11.
8. GETS STUCK ON LADDERS, MAIN DRAINS, RETURN FITTINGS, LIGHTS, STAIRS OR IN CORNERS
A. Remove obstructions from pool walls and floor if possible.
B. Check Scrubbing Brushes for wear (see Page 16-17 SCRUBBING BRUSHES).
C. Adjust Flotation (see page 15, FLOTATION).
D. Models with the New Generation Bottom Lid Assembly: Inspect / Clean NeverStuck™ Rollers (Page 10; Fig. 12)
so that they spin freely.
9. POWER SUPPLY APPEARS TO SHUT OFF BEFORE COMPLETING A CLEANING CYCLE
A. Unplug the Power Supply and check the Fuse. Page 4; Fig. 4a-d.
B. Make sure that the timer (if applicable) is set correctly. Page 8-9.
10. DOES NOT SINK OR FLOATS AWAY FROM THE WALL
A. Check that the Floating Handle is locked and in the correct position.
B. Remove any additional flotation and trapped air. See page 7, CLEANER START POSITION).
C. Check for squeaking or grinding.
11. MAKES LOUD NOISES
A. Allow your Filter Bag to continue to trap debris and particles until your cleaner no longer climbs as high at the
waterline and its top Debris Intake Ports begin to submerse and the noise lessens.
B. Remove any added flotation (Page 15) one-by-one until proper buoyancy has been restored.
C. Apply non-water soluble grease or oil to components.
D. Check Drive Belts and Drive Tracks (Page 18, Page 19; Fig. 26a, 26b) for proper alignment and tension.
12. CLIMBS TO THE WATERLINE THEN MOVES LEFT WHEN FLOATING HANDLE IS LOCKED IN ONE DIRECTION, BUT
DOES NOT MOVE RIGHT WHEN HANDLE DIRECTION IS REVERSED
A. Check that the Floating Handle (Page 5-6) is locked and in the correct position.
B. (Applicable models) Insert one Side Pocket Float (Page 15; Fig. 17b) into the Bottom Lid Assembly.
WARNING: Before performing any troubleshooting maintenance procedures on your cleaner, it should be
disconnected from the Power Supply (transformer) and the Power Supply should be unplugged from the electrical
outlet to prevent the possibility of personal injury or damage to the cleaner!
C. Make sure Cable Plug (Page 3; Fig. 2) fits tightly into Power Supply.
D. If your Power Supply is equipped with a Safety Reset Button make sure that the Power Switch is “ON”. Then
press the Safety Reset Button (Page 8).
E. First, unplug the Power Supply from the outlet! Then, using a cotton swab, dry any moisture within Fuse
Holder (Page 4; Fig. 4a-d) and on fuse itself.
F. Check Floating Cable (Page 3; Fig. 2) and Power Cord for possible cuts or damage.
6. DOES NOT PUMP WATER OR MOVE, OR POWER SUPPLY (Page 4; Fig. 4a-d) DOES NOT TURN ON
A. Check to see if electrical outlet has power.
B. Check the Fuse in the Power Supply (Page 4; Fig 4a-d). If necessary, replace with the same type / amperage
Fuse. If unsure as to Fuse type, please contact Aqua Products’ Customer Service Department online at
AquaProducts.com/Service.