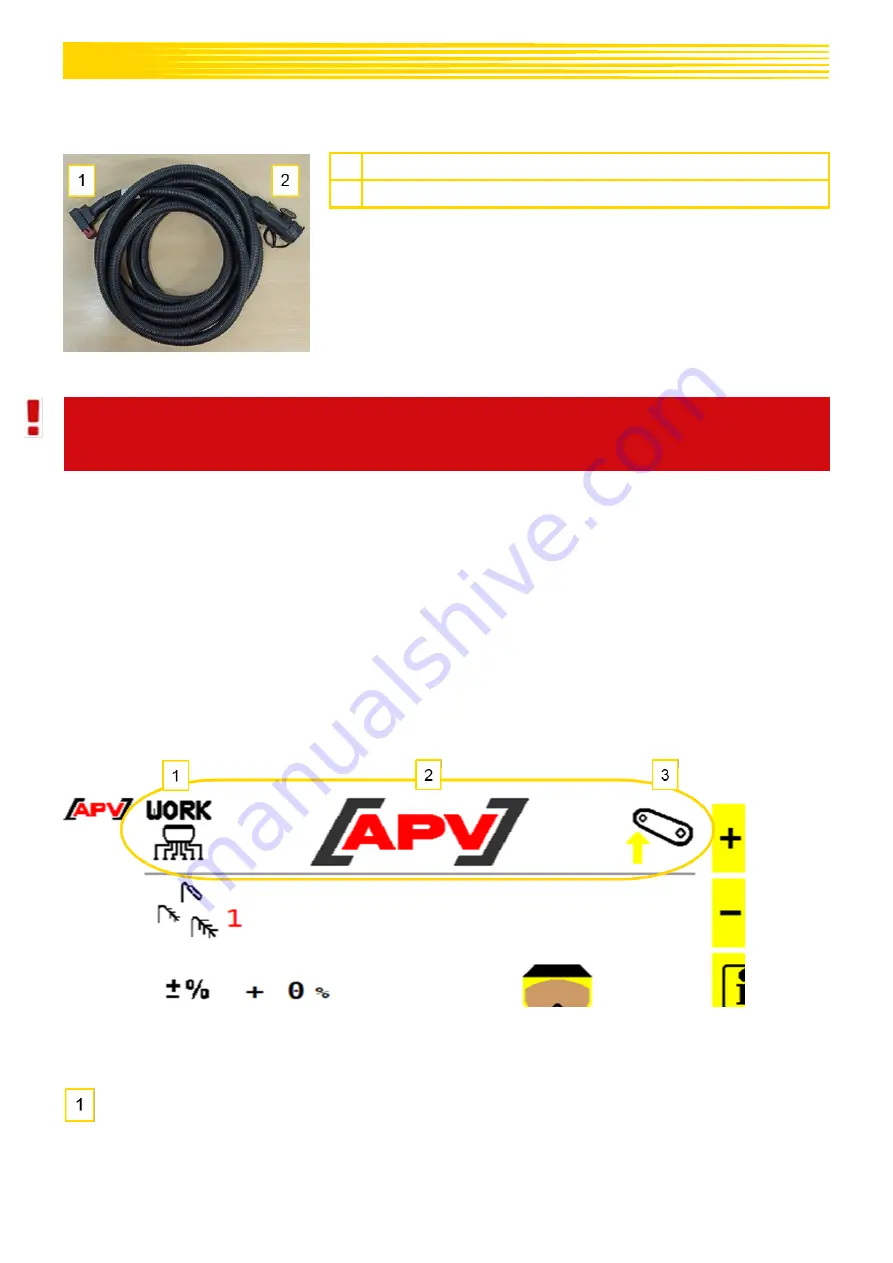
6
4.3
ISOBUS CONNECTION CABLE
The connection cable connects the implement wiring harness to the ISOBUS socket of the tractor.
Figure 4
1 Connection with 16-pin plug (number 5 in Figure 3)
2 Connection with the ISOBUS socket on the tractor
CAUTION!
Before disconnecting the ISOBUS connection cable from the tractor, it is mandatory to turn off
the tractor ignition. Otherwise, the saved values could be lost!
4.4
INSTALLATION MATERIAL AND OTHER ACCESSORIES
Depending on the implement configuration, the corresponding installation material, covers and other parts
will be supplied.
Details about the different versions can be found in the enclosed conversion instructions.
5
INITIAL OPERATION
5.1
GENERAL INFORMATION ON THE CONTROLLER
5.1.1
STATUS BAR
The status bar is located in the upper area of the display, which is shown in every menu:
Figure 5
Description of the display elements
On the left in the status bar, the current menu is shown. In this case, it is the Work
menu.
Summary of Contents for ISOBUS M2
Page 54: ...54 NOTES ...
Page 55: ...55 NOTES ...