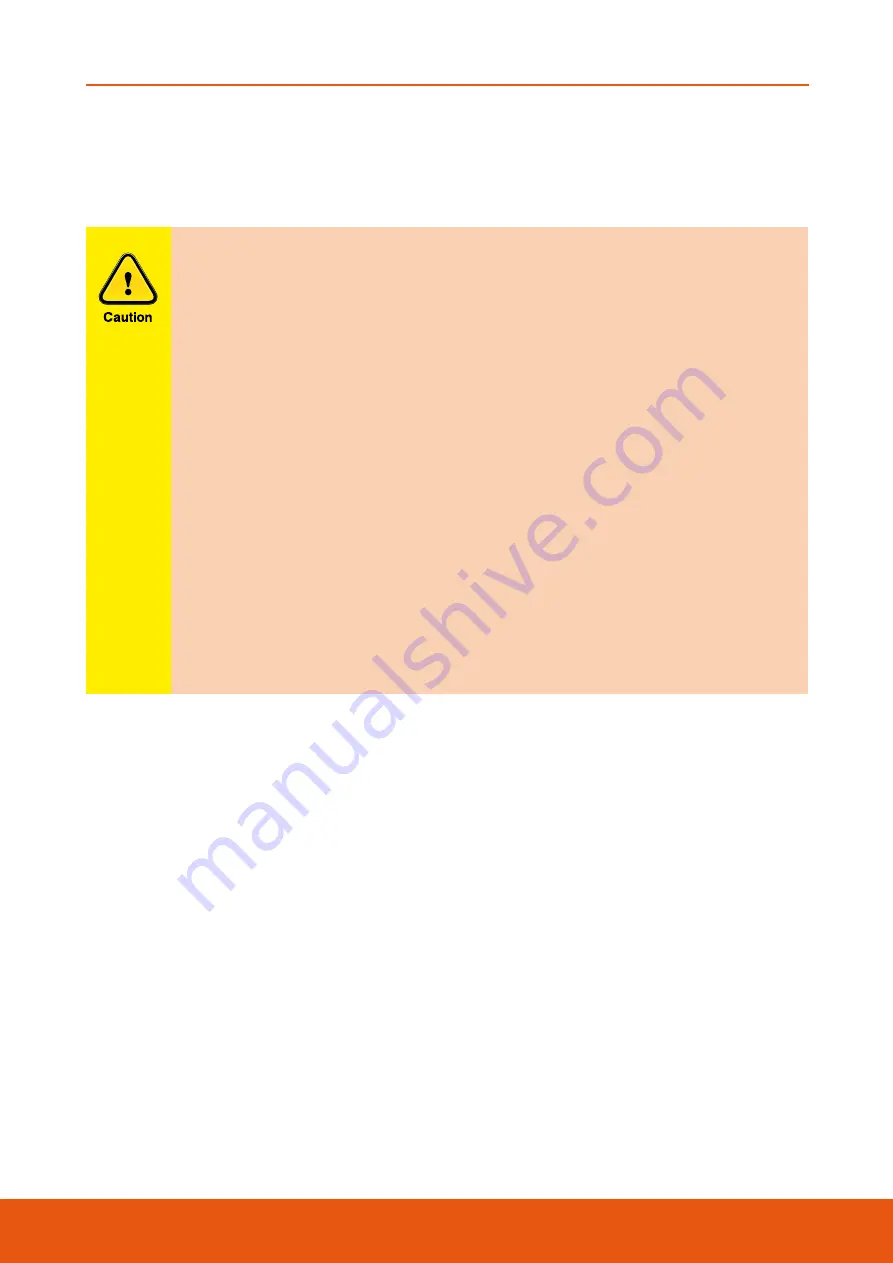
2 PIECE BODY BALL VALVES - FS660 SERIES
Australian Pipeline Valve - Installation, Operation and Maintenance Manual
8
Insert the pipe into the valve end connection until it bottoms out in the socket weld bore. Withdraw the
pipe 1/16” so that a gap remains between the pipe and the bottom of the socket weld bore to prevent
cracks (ASME B16.11). Tack the pipe into the valve and complete the fillet weld.
WELDING INSTRUCTIONS
• Local welding regulations and specification must be complied with when carrying
out welding work.
• Remove any paint and rust around the weld area on the pipe and welded end of the
ball valve.
• Check that the ball valve is correctly positioned and aligned with the pipeline.
• Where weld connection is close to seat area, due to short length of the welded ends
there is a risk that the soft inserts may be destroyed during the welding work.
Hence the following procedure is advised: -
Use temperature measuring strips to check that the temperature does not rise beyond
the permissible limits (160°C). The strips must be fitted to the connection near the soft
inserts. These temperature measurements strips are designed so that, when a type-
dependent temperature is reached, the colour irreversibly changes from white to
black. The temperature measurement strip must be monitored constantly throughout
the welding work. If any change of colour is noticed, the welding work must be
interrupted immediately and the weld allowed to cool. For ‘swing out centre’ design,
the centre section containing soft parts can be removed during welding if preferred,
see 2.4.1.
2.3.3 Buttweld End Valves
Clean the weld ends as necessary and weld into the line using an approved weld procedure. Make sure
the pipe and valve body material given on the valve body or nameplate is compatible with the welding
procedure. (Refer our compatibility cross reference chart for equivalent pipe, valve & fittings grades at
the Technical section of our website). Soft seats can be damaged during welding, take steps to ensure
valve is not over heated, especially smaller size valves (see above caution note).
2.4 VALVE INSTALLATION BY WELDING
For all sizes of valves, leave valves in the full open position during installation, welding and post-weld
heat treatment. This will reduce temperature transmission to soft seats. After welding completion, open
the valve and flush line to clean out any foreign matter. Valves over 65 NB ( 2 1/2”) have minimal risk of
temperature damage to seats.
2.4.1 Method
For valves up to 80 NB (3”) the welding temperature can adversely affect the PTFE and elastomer
components. Follow the welding instructions above but also use temperature measuring strips to monitor
temperature. It will be the responsibility of the operator to ensure valves are kept cool during welding