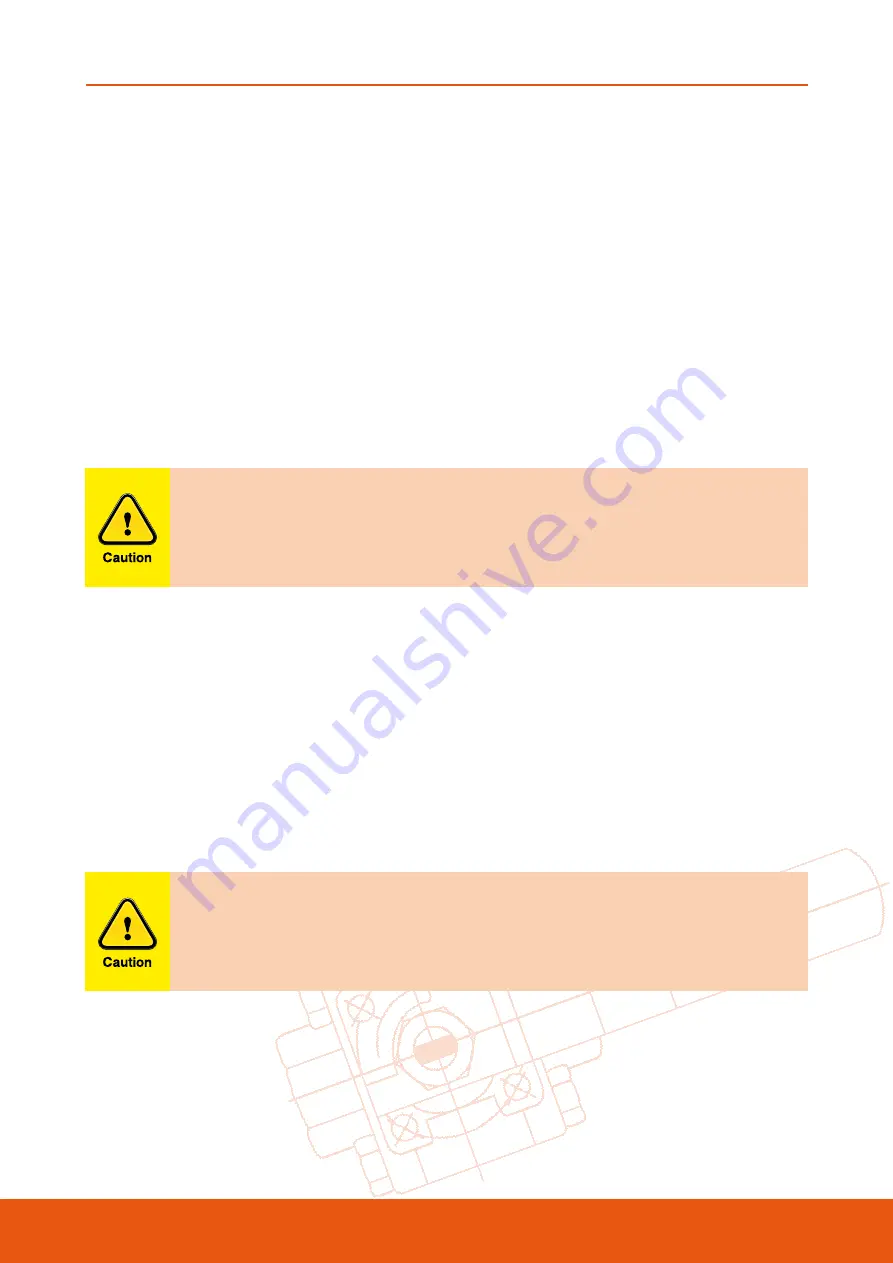
Australian Pipeline Valve - Installation, Operation and Maintenance Manual
7
FLOATING BALL VALVES - BV100 SERIES
2.1 INSTALLATION POSITIONS
Ball valves are usually bi-directional, and therefore may be installed in either direction. In some cases,
ball valves such as ‘metal to metal’ seated and low temperature valves may be uni-directional, in which
case the direction of flow will be indicated on the valve body.
2.2 PREPARATION FOR INSTALLATION
• Remove protective end caps or plugs and inspect valve ends for damage to threads, weld ends or
flange faces.
• Thoroughly clean adjacent piping system to remove any foreign material that could cause damage to
seating surfaces during valve operation.
• Verify that the space available for installation is adequate to allow the valve to be installed and to be
operated.
Ensure sufficient clearance for the stem in the full open position. Inadequate
clearance for valves may add mechanical loading to the valve ends. Sufficient
clearance should be allowed for threaded end valves to be ‘swung’ during
installation.
2.3 END CONNECTIONS
2.3.1 Threaded Ends
Check condition of threads on mating pipe. Apply joint compound to the male end of joint only. This will
prevent compound from entering the valve flowpath.
2.3.2 Flanged Ends
Check to see that mating flanges are dimensionally compatible with the flanges on the valve body ensure
sealing surfaces are free of debris. Install the correct studs and nuts for the application and place the
gasket between the flange facings.
Stud nuts should be tightened in an opposing criss-cross pattern in equal increments
to ensure even gasket compression.
2.3.3 Socket weld Ends
Remove all debris, grease, oil, paint, etc., from the pipe that is to be welded into the valve and from the
valve end connections.