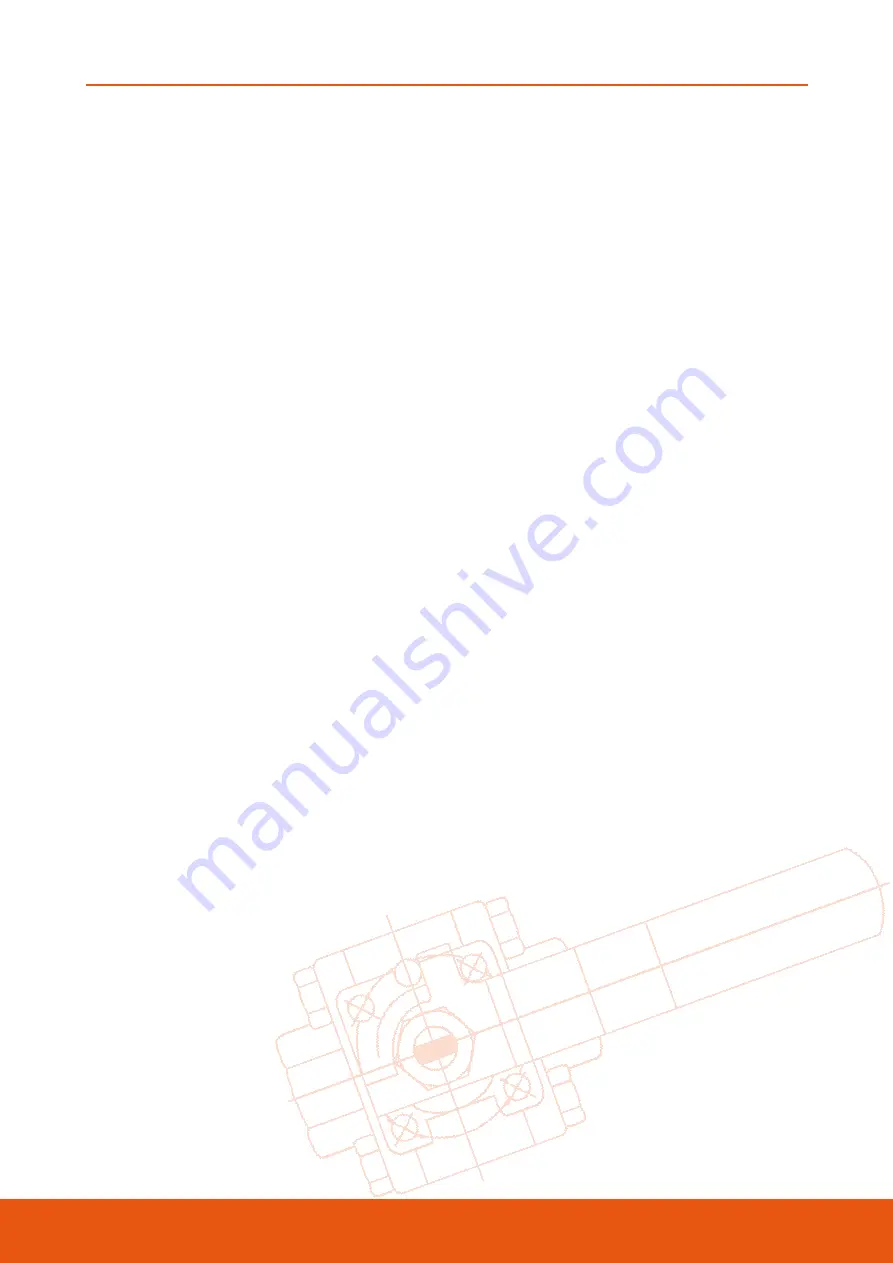
Australian Pipeline Valve - Installation, Operation and Maintenance Manual
9
FLOATING BALL VALVES - BV100 SERIES
temperature. It will be the responsibility of the operator to ensure valves are kept cool during welding
and then post-weld testing of the valve should be performed. Larger size valves over 80 NB (3”) are less
likely to transmit heat to seat and stem packing during welding but still care should be taken. The ‘swing
out’ version of BV100 Series valve can be disassembled prior to welding to avoid damage to seats and
body seals (only 3 bolts need to be removed to ‘swing out’ the centre section of the remaining bolt).
Ensure the centre section of the valve is ‘swing out’, typically only 800 class up to 50 NB (2”) are ‘swing
out’ design. The seats and seals remain in the centre section hence no seat or seal removal is required. If
this option is recommended by APV then these valves have in-line removable sections hence no line
movement is necessary to insert the fully self contained centre section. There must be sufficient
movement in line to allow tightening of body bolts to compress the body gasket. In class 1500 and 2500
the disassembly method cannot be performed due to intersecting components.
1- Tack weld in 4 points on both end caps, leave the valve in the open position and do not move during
and at least 30 minutes after welding until the valve cools. For socket weld also see 2.3.3, for butt
weld also see 2.3.4.
2- Remove centre section and complete welding.
3- Replace centre section but first apply grease to the seat rings to aid the seat and torque (unless for
oxygen service).
The below procedures should also be followed:
a) Always ensure there is no pressure or product in the line. Ball valves will be supplied with socket weld
ends to ANSI B16.11 or butt weld ends to ANSI B16.25. Welding should be done using procedures and
welders qualified under section IX of the ASME boiler and pressure vessel code.
b) For 1500 & 2500 class valves, if the body seats are removed, put them back in the same side from
which they were removed and take care not to cut or scratch them. Smear some grease into the seat
pocket to help them fit into pockets. (Don’t apply grease if for oxygen service). If the valve leaks from
the stem after assembly, try adjusting the stem packing. Always clean all welding surfaces from
contamination, grease etc., prior to welding.
Note: For higher pressures and sizes, Delrin and PEEK seats may have graphite or PTFE backing rings.
c) Always do as a low temperature weld as necessary to obtain a reliable connection. Use whatever
measure necessary to localise heat at the joint, dissipating it before damage can occur to adaptor
gaskets and/or seats (the main risk is seats). Use a tempil stick or other temperature indicator on the
outside of the valve body (centre section) directly adjacent to adapter end piece) being welded to
assure the body temperature does not increase 160°C. Always leave valve in open position during
welding but also at least 60 minutes after welding unit valve cools.
d) Where required APV will supply spare body gaskets. Graphite body gaskets are brittle so great care
should be taken not to damage.
2.4.2 No Disassembly Method
Valves under 50 NB (2”) that are not disassembled should have pup ends fitted to avoid seat damage. If
not fitted ensure valve body temperature is kept cool. Temperatures over 180°C can damage seats &
seals. In 1500 and 2500 class, BV100 valves have encapsulated seats, hence you must have 3mm of
movement in your line in order to replace disassembled centre section, due to seats intersecting end cap