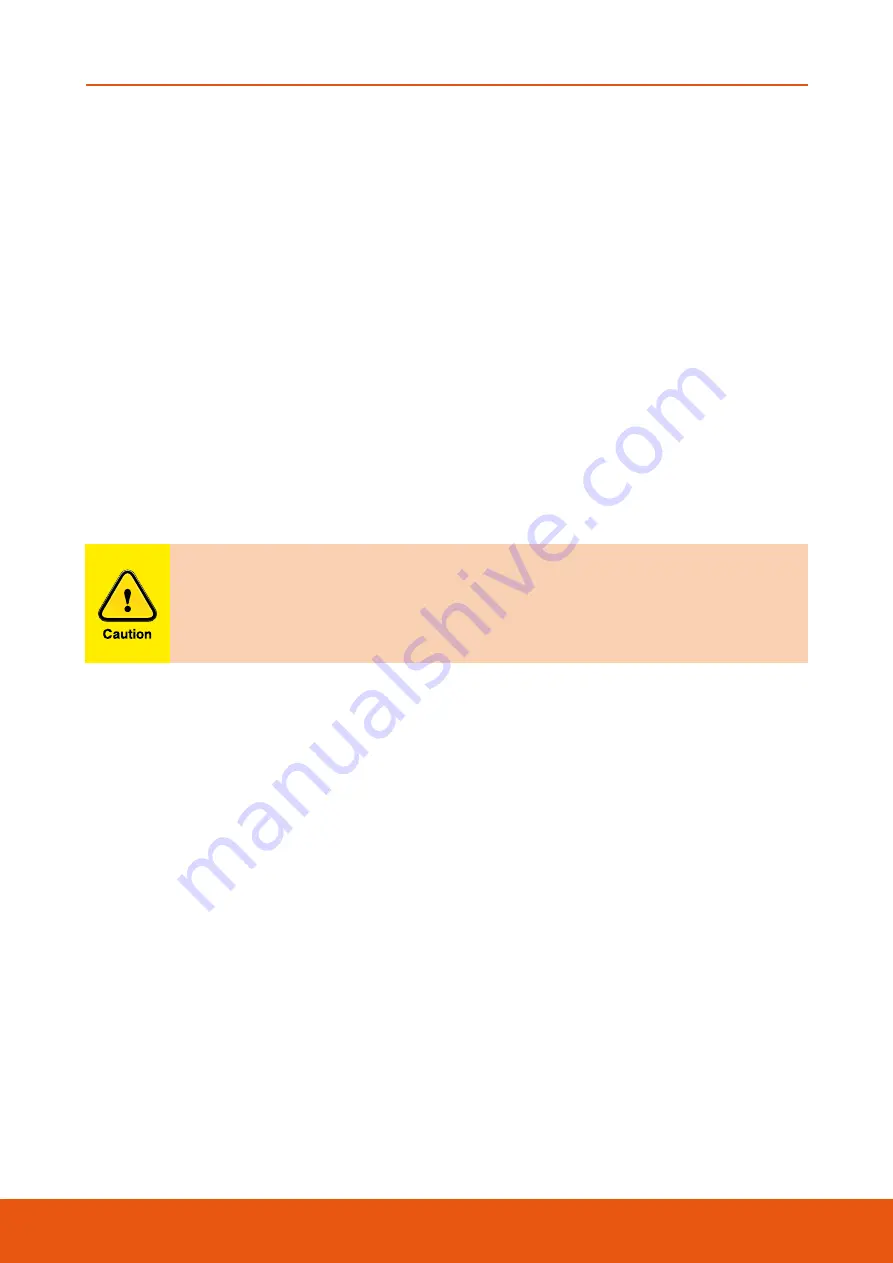
Australian Pipeline Valve - Installation, Operation and Maintenance Manual
6
FLOATING BALL VALVES - BV100 SERIES
1.3 PREPARATION
a) Remove the valve end protection.
b) Prior to shipment, a preservative/corrosion inhibitor may have been applied to the inner body of the
valve. This preservative/corrosion inhibitor can be removed with a solvent provided the solvent used
does not affect the seats/seals used in the valve.
c) The inside of the valve should be inspected and blown out with compressed air. Adjacent piping must
be clean and free from debris to prevent damage to the valve.
d) To prevent valve distortion, inefficient operation or early maintenance problems, support piping on
each side of the valve.
e) Make sure the valve is positioned such that there is sufficient space so that the hand wheel is easily
and safely reached and there is enough clearance for the stem when the valve is open.
f) Install the valve according to the flow indicator on the valve body where applicable.
2 . 0 I N S T A L L A T I O N
Piping should be properly aligned and supported to reduce mechanical loading on
end connections. Never use the lever (wrench) to hold the valve during transport,
handling or assembly.
The following procedure is required to be followed for correct installation.
a) Before installation confirm the marking (rating, size and material) on the valve body and nameplate.
Ensure the valve is suitable for the service which it is being used.
b) Body bolts and nuts on valve shall be checked and retightened if necessary in case loosened during
installation.
c) Remove valve end protectors and ensure gasket faces are free from damage. Tighten all bolts between
mating flanges and valve equally paying careful attention to properly tighten bolts. Ensure you rotate
tightening procedure (opposing bolts sequentially) gradually increasing torque. Refer to Appendix Table
2 for bolt tightening sequence.
d) Prior to installation of valve, ensure the line is completely flushed to remove any debris as soft seated
ball valves are easily damaged. Filters or strainers should be installed upstream to protect soft seated
valves.
e) Valves will operate at any angle horizontally or vertically, although it is recommended you install
valves in a vertical position with stem pointing upwards for ease of operation, inspection and
accessibility.