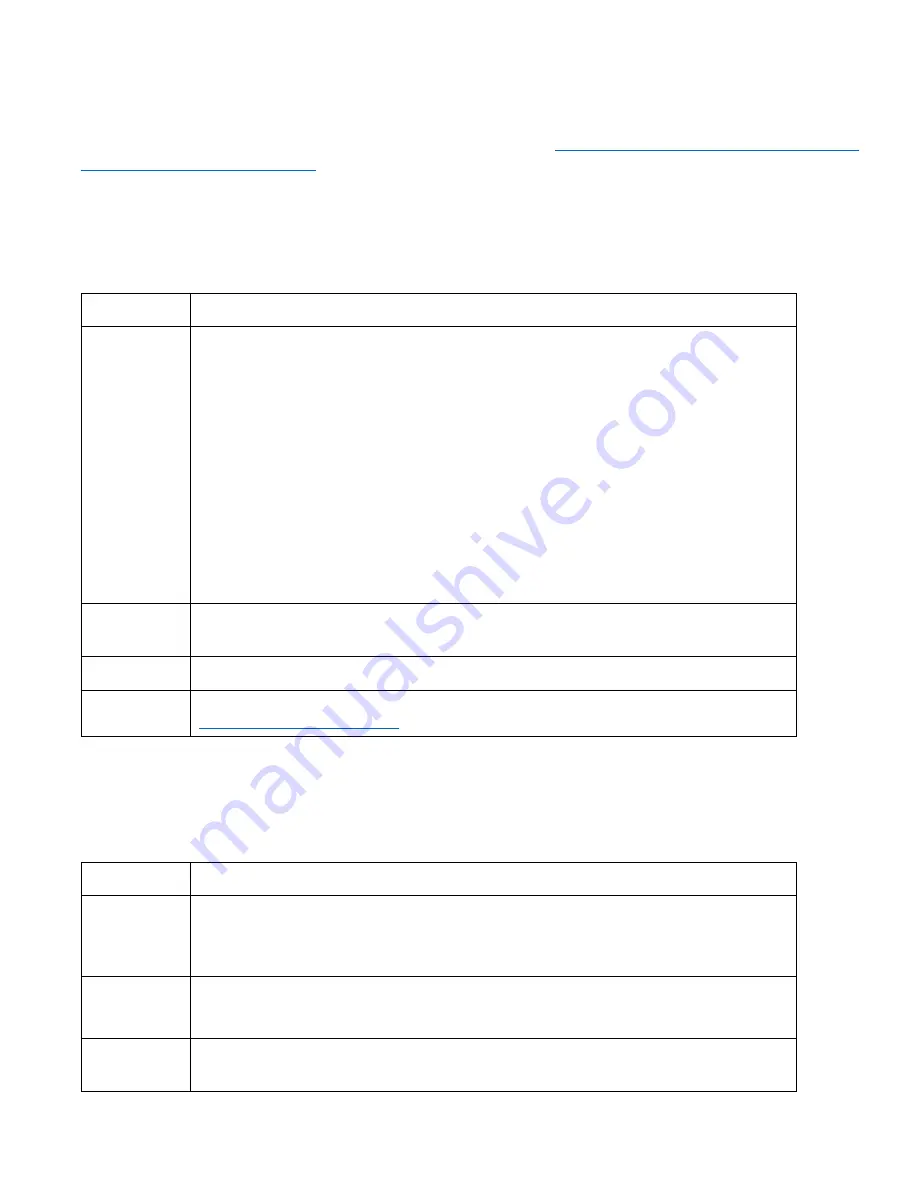
The Force™ 2-Stage Operation Manual
34
Revision Date 4/23/2019
4. System Preventive Maintenance
For Apeks System Manuals and Other Component Manuals visit
http://www.apekssupercritical.com/apeks-
supercritical-operation-manuals/
Included with each system is a small squeeze bottle to help with proper maintenance and cleaning of your
systems CO
2
lines. Ethanol (200 proof) is a typical and acceptable cleaning agent. Please label the bottle
accordingly.
4.1.
Extraction System Maintenance (Extractor and Separator Stands)
Frequency
Maintenance Item
After Each
Extraction
•
Remove extracted oil from collector cup and separator walls, clean walls and
cup with alcohol.
•
Check separator 2 for oil carryover and clean if necessary.
•
Inspect separator gaskets and grooves prior to reassembly.
•
Clean piping between separator 1 and 2 with alcohol.
•
Clean Separator 2 CO
2
outlet to separator filter.
•
Remove spent material from the extraction vessel by vacuuming it out through
the top flange.
•
Verify the extractor filters are clear and free of debris.
•
Check extraction vessel O-rings and O-rings groove sealing surfaces for
damage – replace if necessary.
•
Inspect the surfaces on Extraction vessel to make sure they are free from dust
and debris. Failure to clean surfaces properly can cause vessel not to seal
properly or damage to the cup seal.
Every 80
Hours
•
Run the system “empty of plant material” for one hour to clean the high-
pressure side of the system and extraction vessel(s).
Yearly
•
Check torque on all screws in electrical panels (see Appendix G).
Resource
Apeks online store:
4.2.
Diaphragm Compressor Maintenance
See Diaphragm Compressor Manual for specific instructions on maintenance items. Below is general
system information.
Frequency
Maintenance Item
Daily
•
Check oil level.
•
Check oil pressure.
•
Listen for abnormal noise or vibration.
•
Check Leak Detection System status.
Every 500
Hours
•
Clean/Change Separator Filter.
•
Check belt tension (See Appendix A).
•
Clean process check valves.
Every 1500
Hours
•
Perform regular oil change.
•
Check torque on all screws in electrical panels (see Appendix G).
Summary of Contents for THE FORCE 2-STAGE
Page 21: ...The Force 2 Stage Operation Manual 21 Revision Date 4 23 2019 2 2 9 3 PLC Analog Inputs...
Page 22: ...The Force 2 Stage Operation Manual 22 Revision Date 4 23 2019 2 2 9 4 PLC Analog Outputs...
Page 46: ...The Force 2 Stage Operation Manual 46 Revision Date 4 23 2019...
Page 47: ...The Force 2 Stage Operation Manual 47 Revision Date 4 23 2019...
Page 48: ...The Force 2 Stage Operation Manual 48 Revision Date 4 23 2019 7 5 Appendix E CO2 Phase Diagram...
Page 53: ...The Force 2 Stage Operation Manual 53 Revision Date 4 23 2019...
Page 54: ...The Force 2 Stage Operation Manual 54 Revision Date 4 23 2019...
Page 55: ...The Force 2 Stage Operation Manual 55 Revision Date 4 23 2019...
Page 56: ...The Force 2 Stage Operation Manual 56 Revision Date 4 23 2019...
Page 57: ...The Force 2 Stage Operation Manual 57 Revision Date 4 23 2019 Z...
Page 58: ...The Force 2 Stage Operation Manual 58 Revision Date 4 23 2019...
Page 59: ...The Force 2 Stage Operation Manual 59 Revision Date 4 23 2019...
Page 60: ...The Force 2 Stage Operation Manual 60 Revision Date 4 23 2019...
Page 61: ...The Force 2 Stage Operation Manual 61 Revision Date 4 23 2019...
Page 62: ...The Force 2 Stage Operation Manual 62 Revision Date 4 23 2019...
Page 63: ...The Force 2 Stage Operation Manual 63 Revision Date 4 23 2019...
Page 64: ...The Force 2 Stage Operation Manual 64 Revision Date 4 23 2019...
Page 65: ...The Force 2 Stage Operation Manual 65 Revision Date 4 23 2019...
Page 66: ...The Force 2 Stage Operation Manual 66 Revision Date 4 23 2019...
Page 67: ...The Force 2 Stage Operation Manual 67 Revision Date 4 23 2019...