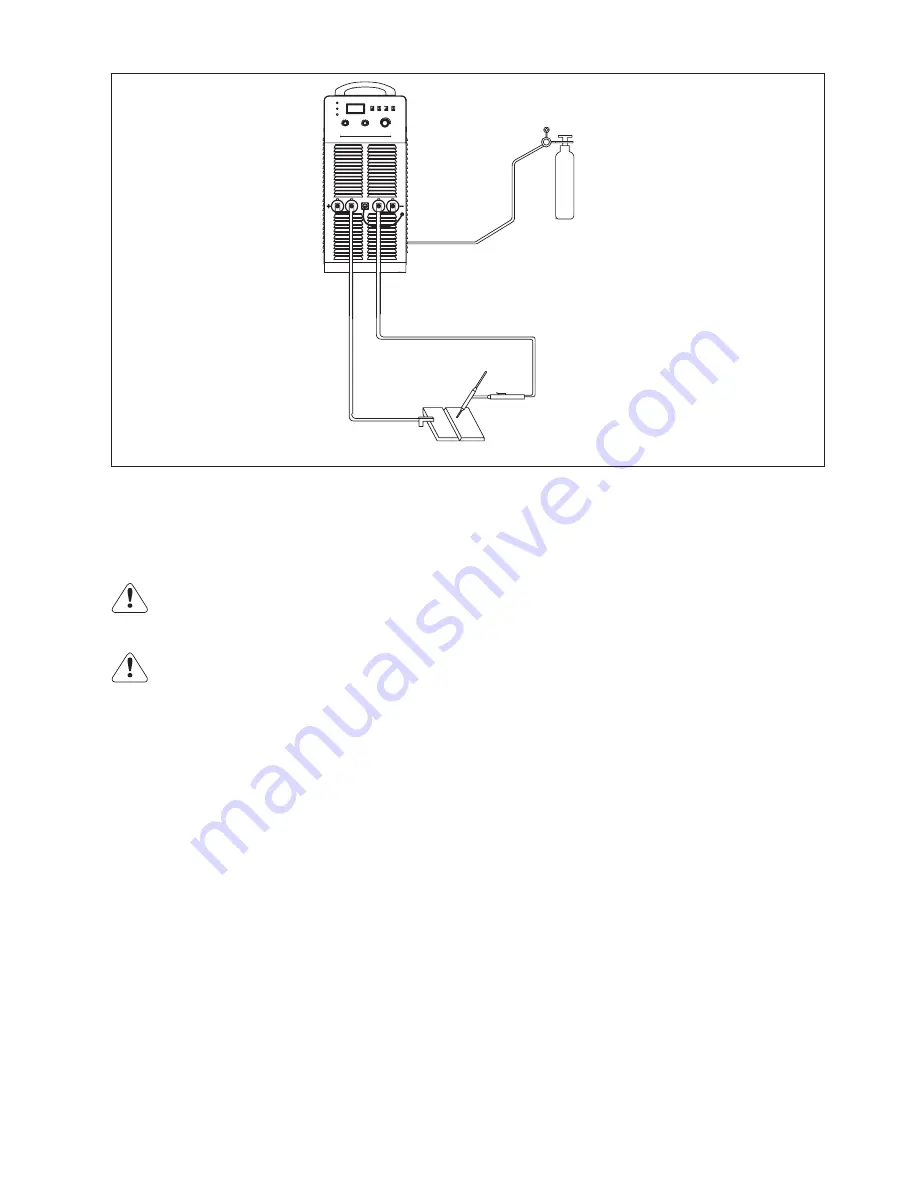
64
Fig. 9-5-1: Installation
Input power supply cable requirement
Please refer to “ARC1000/1250” the relevant “5-5 Installation and operation” in details.
Operating guide
Warning!
Operating the welding machine incorrectly can cause serious injury and damage. Do not use the functions
described here until you have read and completely understood all the following guides:
-“safety rules”
-“before commissioning”
Warning!
Electric shock is very dangerous. As soon as the power source is switch on, the welding electrode is
power on. Make sure that the electrode does not touch any person or conductor or grounded parts (e.g. lifting
appliance etc.)
SMAW welding with basic electrode: E7016/E7018
1.Use short circuit copper block to connect two positive output terminals, then connect welding cable with short
circuit copper block;
2.Use short circuit copper block to connect two negative output terminals, then connect ground cable with short
circuit copper block;
3.Place switch on “ON” position, power on;
4.Choose “Panel control” mode on control panel;
5.Choose “Amp/Volt” switch on “Amp” position;
6.Adjust arc length “L/S/M” switch according to welding cable length;
7.Choose “SMAW/TIG” switch on “SMAW” position;
8.Adjust arc start current, arc force current, welding current according to wire diameter, welding position;
9.Welding
HF TIG welding
1.Screw shielding gas regulator onto the gas cylinder and tighten it; connect gas hose with shielding gas regulator
and gas inlet on welding machine rear panel;
2.Use short circuit copper block to connect two positive output terminals, then connect work piece with short
circuit copper block;
3.Use short circuit copper block to connect two negative output terminals, then connect torch welding cable with
short circuit copper block;
4.Connect gas hose of torch with gas outlet of welding machine front panel;
5.Connect torch control cable with control socket of welding machine front panel;
6.Place switch on “ON” position, power on;
7.Choose “SMAW / TIG / Gouging” switch on TIG position;
8.Choose “Panel control” mode on control panel;
9.Choose “Amp/Volt” switch on “Amp” position;
10.Select 2 step/4 step;
11.Adjust welding current according to plate thickness;
A/V
4
3
2
1
5
6
7
8
9
10
4
3
2
1
5
6
7
8
9
10
OVER
-
HEAT
FAULT
DEFAUL T
PHASE
ARC FO
RCECURRENT
WE LDING
CURRE N T
ARC ST AR
T ING CURRE NT
SMAW
TIG
A
V
2-STEP
4-S TEP
ARC LE N GTH
M
S
L
GOU GIN G
TIG1000
Inverter MM A /TIG Arc W e lding M a chine
Workpiece