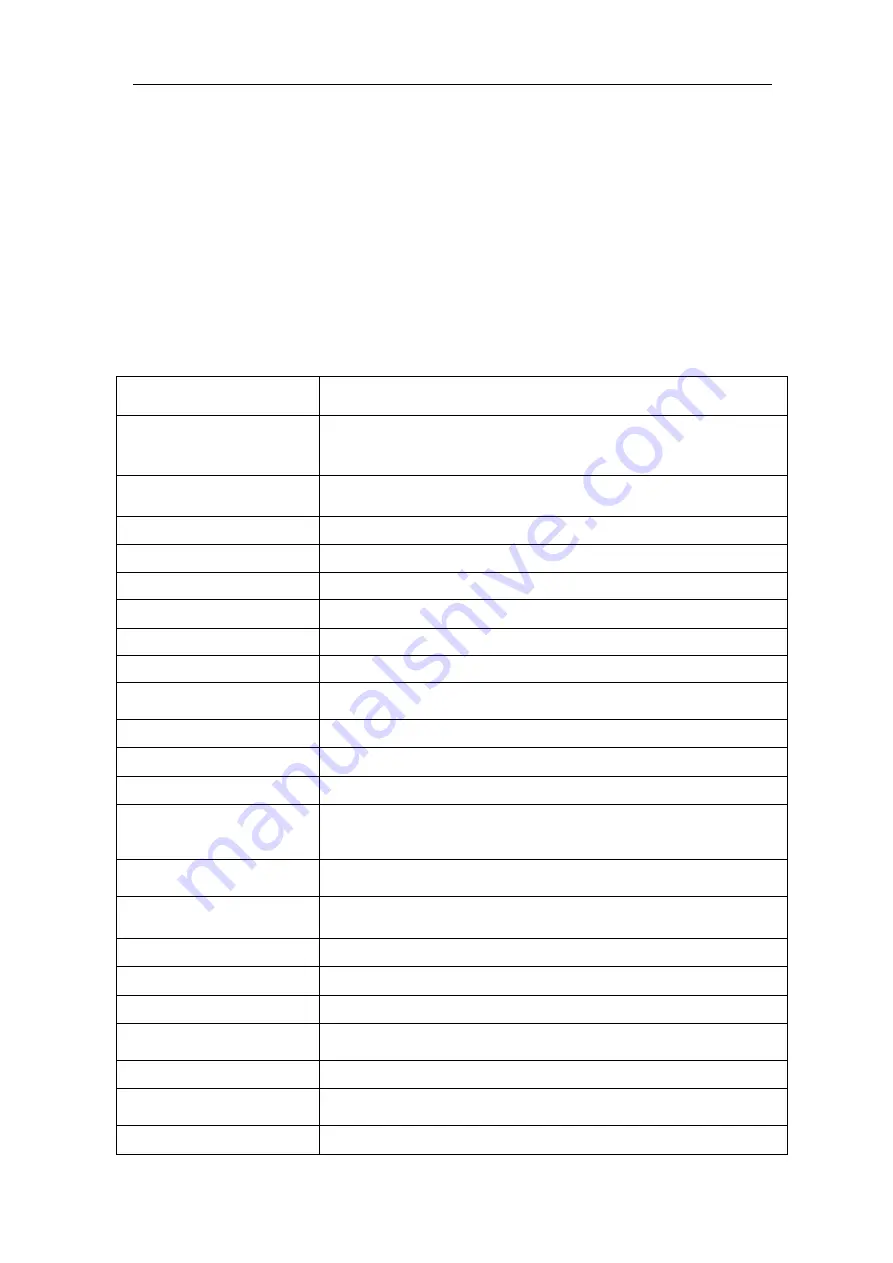
1
1 General Information
1.1 General
GPS/F-1006
Series Computerized Control System for Industrial Sewing Machines: 1)
Adopt the world leading AC servo control technology on main shaft motor, which features
high torque, good efficiency, stable speed and low noise; 2) Diversified design of control
panel can meet the special requirement of users on attachment; 3) System adopts German
style structure, which offers easy installation and maintenance to users; 4) The control
software can be updated through remote communication system, which helps users to
improve the function of products constantly.
1.2 Functions & Parameters
Type of Controller
*36)
Computeized Pattern Sewing Machine
Sewing Range
X(Lateral Direction) Y(Longitudinal Direction)
:
100 x 60
:
Max. Sewing Speed
:
2700rpm(Sewing pitch below 3mm)
:
Stitch Length
0.1
~
12.7mm(Min. Resolution: 0.10mm)
Type of Feeding Motion
Intermittent feed (Pulse Motor 2-shaft Driving)
Needle Bar Stroke
41.2mm
Needle
DP×5
、
DP×17
Lift of Feeding Frame
Standard 18mm Max. 22mm(Pneumatic type Max. 25mm)
Needle Bar Stroke
Standard 4mm(0
~
10mm)
Lift of Intermediate
Presser
20mm
Shuttle
Double-capacity Semi-rotary Shuttle
Memory of Pattern Data
U Disk
Pause
Stop the machine during the process of sewing
Enlarging / Reducing
Function
Allows a pattern to be enlarged or reduced on the X axis and Y
axis independently when sewing a pattern. Scale : 1% to 400%
times (0.1% for each step)
Enlarging/ Reducing
Method
Method for enlarging or reducing length of stitch form
Sewing Speed Limitation
:
200
~
2500rpm(100rpm for each step)
:~
Pattern Selection
Pattern No. selection method
Bobbin Thread Counter
UP/DOWN method (0 to 9,999)
Sewing Counter
UP/DOWN method (0 to 9,999)
2
nd
Origin Setting
Using jog keys, a 2nd origin (needle position after a sewing
cycle) can be set in the desired position within the sewing area.
Sewing Machine Motor
Servo Motor
Needle Highest Position
Stop Function
After the completion of sewing, the needle can be brought up to
its highest position
Power 500W
www.garudan.cz
Summary of Contents for GARUDAN GPS/F-1006 Series
Page 2: ...w w w g a r u d a n c z...
Page 4: ...w w w g a r u d a n c z...
Page 47: ...39 w w w g a r u d a n c z...
Page 105: ...w w w g a r u d a n c z...
Page 109: ...101 10 3 3 1006 Control System Diagram w w w g a r u d a n c z...