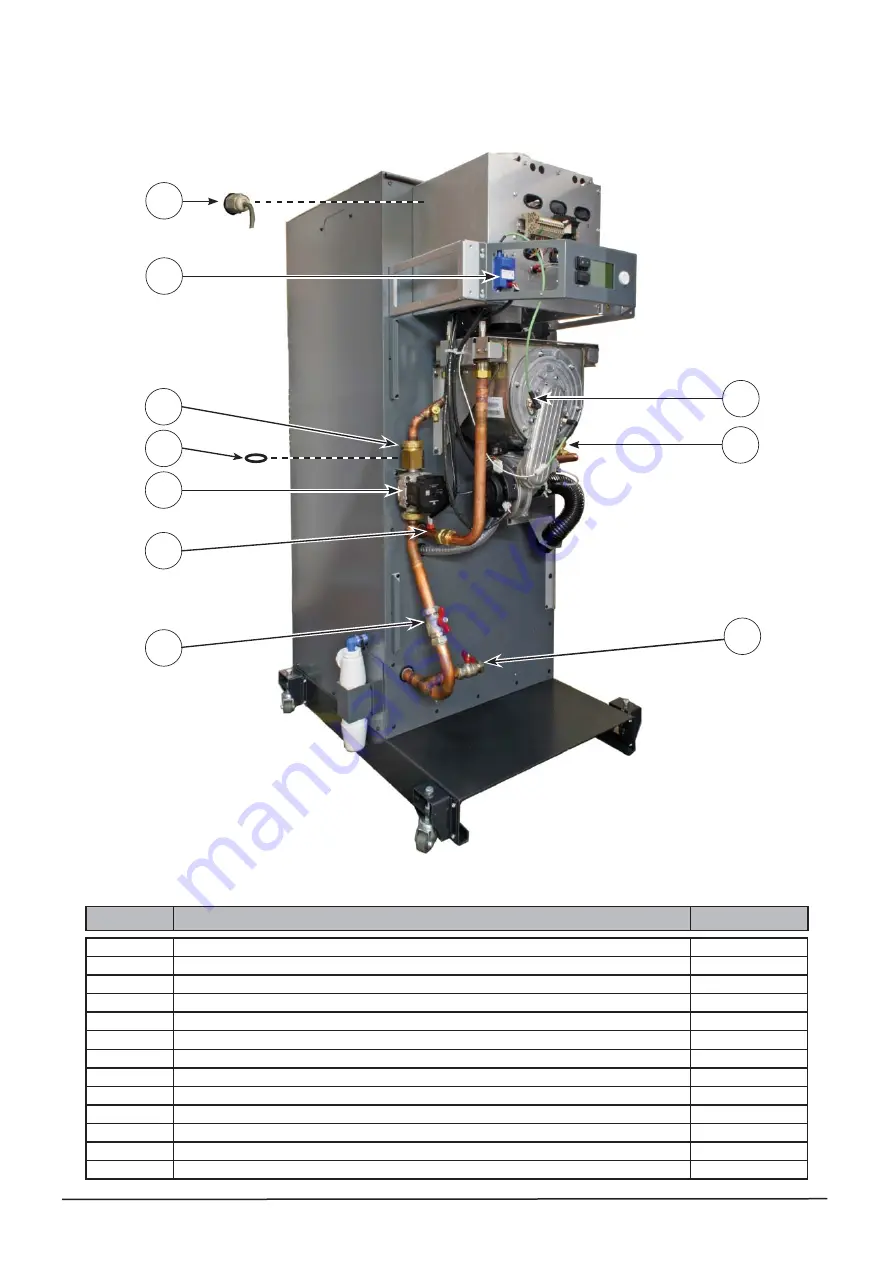
Maintenance
65
MAXXfl o EVO
6.3 COMPONENT ILLUSTRATIONS (CONTINUED)
GENERAL COMPONENTS
300
301
302
304
306
311
305
308
307
Item No.
Description
Part Number
300
CABLE GLAND
7709386
301
SPARK GENERATOR
7709314
302
LEAD FOR SPARK ELECTRODE
7709313
303
PRESS. SENSOR WATER H3
7709328
304
22MM RIGID FAN GAS COCK
7709371
305
NON-RETURN VALVE ASSY
7709287
306
PUMP FOR MAXXfl o EVO
7709310
307
PUMP / NRV GASKET
7720039
308
TEMP. SENSOR CASCADE B10
7709330
309
28MM COMPRESSION TEE
7709368
310
AIR PRESSURE SWITCH (COND. LINE)
7709288
311
28MM ISOLATION VALVE
7709366
312
SPARE DRAIN VALVE 22MM
7727903
312