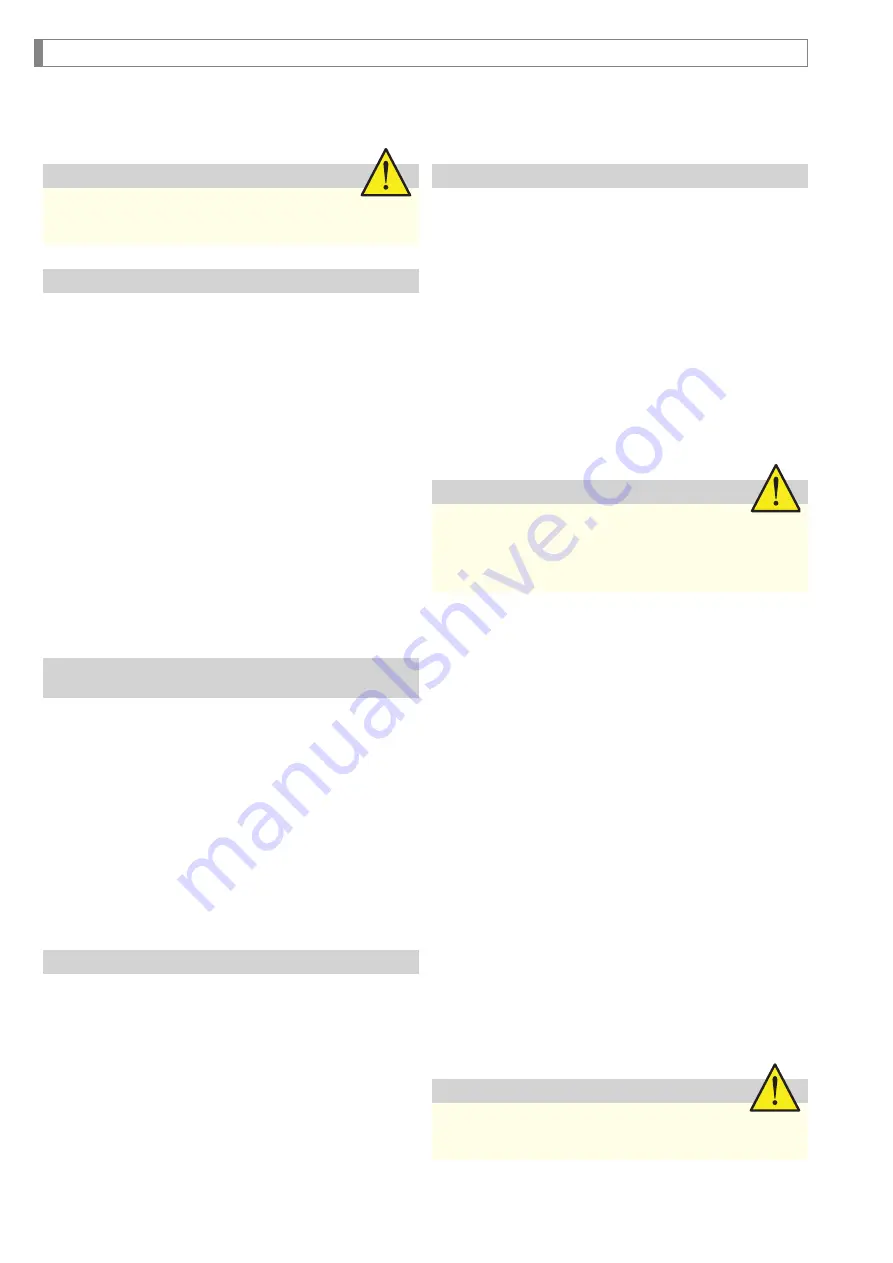
1 4
Electrical installation
General Safety
When using electrical equipment, you should always follow
basic safety precautions, including the following:
· The installation and wiring of this product must comply
with all national, federal, state, municipal, and local codes
that apply.
· Properly ground the enclosure to an adequate earth
ground.
· Do not modify any factory wiring. Connections should only
be made to the terminals described in this section.
· All connections to the unit must use conductors with an
insulation rating of 300 V minimum, rated for 105 ºC
(212 ºF), a minimum flammability rating of VW-1, and be
of appropriate gauge for the voltage and current required
(see specifications).
· Do not allow moisture to enter the electronics enclosure.
Conduit should slope downward from the unit housing.
Install drip loops and seal conduit with silicone rubber
product.
Disconnect requirements for permanently
installed equipment
A dedicated disconnecting device (circuit breaker) must be
provided for the proper installation of the unit. If inde-
pendent circuits are used for power input and main relay
outputs, individual disconnects are required.
Disconnects must meet the following requirements:
· Located in close proximity to the device
· Easily accessible to the operator
· Appropriately marked as the disconnect for the device and
associated circuit
· Sized appropriately to the requirements of the protected
circuit (See specifications)
Installation
There are two versions of the junction box enclosure. Both
versions have four small holes, which are used for factory-
wiring the sensors to the junction box. In addition, the junc-
tion box has one or two large holes for wiring the junction
box to other junction boxes and the signal processor:
· One large hole (conduit installation); the large hole accom-
modates a 3/4" conduit fitting.
· Two large holes (non-conduit installation); the two large
holes are equipped with PG13.5 cable fittings. Cable trays
for non-conduit installations are required.
Electrical installation
Caution
Very high voltage is present. Remove power from the unit
before installing, removing or making adjustments.
Guidelines
· The procedure below assumes the conduit/cable tray has
been installed.
·
Seal all conduit fittings against water entry. Install drain
holes at conduit/cable tray lowest elevation(s) to allow
condensation to drain.
· Use Belden 3-conductor shielded interconnect cable or
equivalent to wire junction boxes together and to the
signal processor, for lengths up to 305 m (2,000').
· When wiring cable to junction box terminals, strip back 3"
(76 mm) of cable sheathing to expose the three conductor
wires and shield wire inside. Strip 1/4" (6 mm) of insula-
tion from the end of each of the conductor wires. Spread a
generous bead of sealant around the sides of the PG 13.5
cable fittings. Install the fittings in the two large holes.
1. See
Figure 4:
Route the 3-conductor cable through the
fitting into the junction box farthest from the signal
processor. Connect wires from the cable to the TB2
terminal in the junction box: black wire to B, white wire
to W, and red wire to R. Connect the cable shield wire to
the Shield terminal between TB1 and TB2.
2. Route the cable through conduit/cable tray to the next
junction box. Estimate the required length of cable to
the terminal strip, allowing a little extra for strain relief.
Cut the excess cable. Connect wires from the cable to
the TB1 terminal in the junction box: black wire to B,
white wire to W, and red wire to R. Connect the cable
shield wire to the Shield terminal between TB1
and TB2.
3.
Route another 3-conductor cable through the fitting into
this junction box, and attach wires to the TB2 terminal:
black wire to B, white wire to W, and red wire.
4. Repeat Steps 2 and 3 until all junction boxes for the ves-
sel are wired together.
5. Route the cable from the last junction box through
conduit to the signal processor. Refer to the signal pro-
cessor manual for wiring the junction box to the signal
processor. One vessel takes up one channel in the signal
processor—the channel shows the average value from
all the Load Stands supporting the vessel.
Caution
All wiring routed between Junction Boxes and Signal
Processor must be continuous (no splices)
Caution
Use only Sikaflex™ 1A polyurethane sealant, Sikaflex™
ProSelect Construction sealant or Dow Corning™ RTV 739
or RTV 738. Other sealants may contain acetic acid, which
is harmful to sensors and electronics.
Summary of Contents for Load Stand II
Page 23: ...23 Notes ...
Page 24: ...2 4 Notes ...