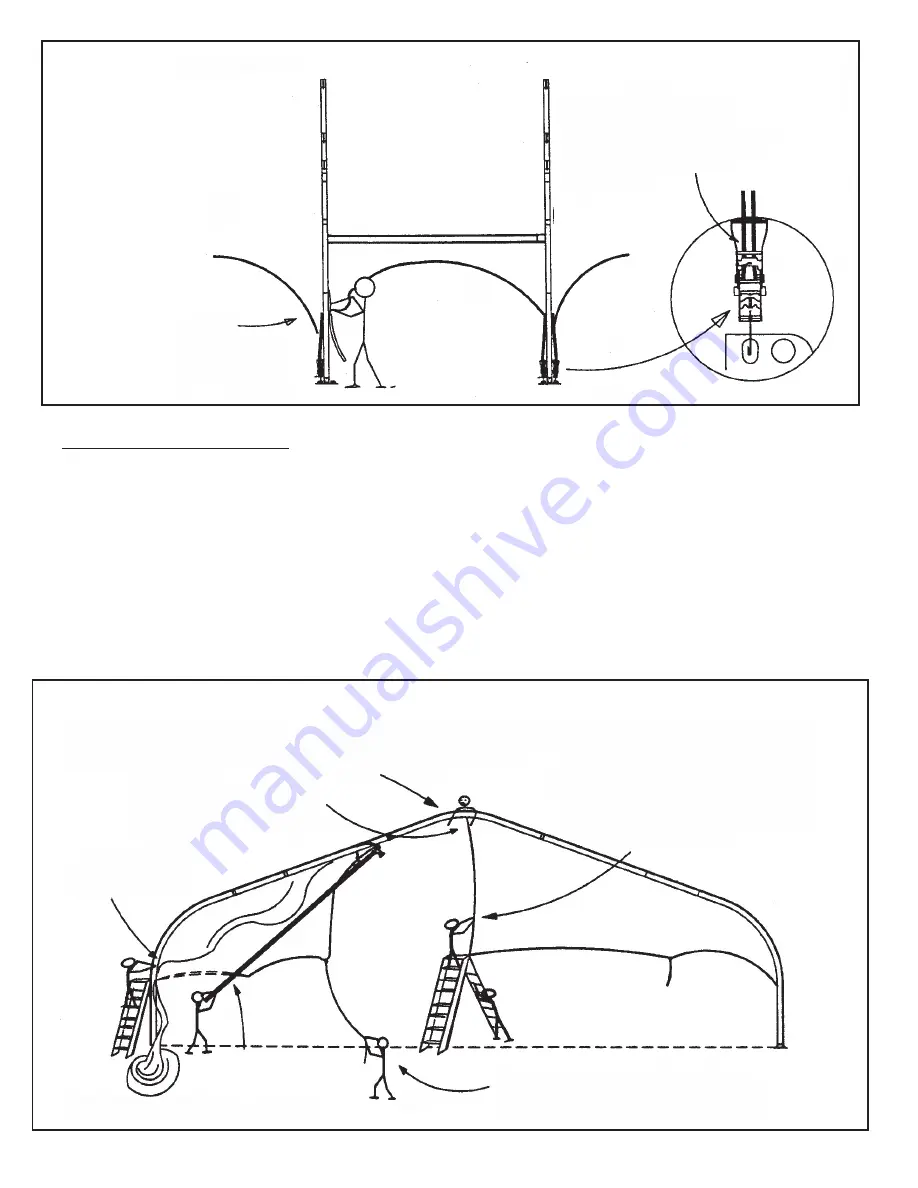
17
Tensioning of Middle Panels: (See Above)
1. Tuck the fabric tails of each panel downward into the beam channel flare until all
middle panel kedar rests within the outer beam channel.
2. Install (2) fabric tensioning winches with hooks into each baseplate, as shown.
3. Insert the tension webs of each middle panel through the slot in the spindle of each
fabric winch and pull all surplus webbing through the winch.
4. Crank the handle of the winch so that the webbing is wrapped around the spindle.
Install Gabled End Fabric Panel (See Top of Page 18)
5. Coordinate the tensioning of all four corners of each middle panel, so that tensioning
is equalized and wrinkles are avoided. Metal pull rings should be equal distance
above the baseplate at all four corners of the panel.
Insert web tail
through spindle.
Ratchet handle up
& down to tension
fabric
Tuck kedar tail
downward into
outer beam channel
Tensioning of Middle Panels
Using a safety line tied off to the frame system, a worker
lays on last middle panel and engages caribiner to join the 2
halves of the gabled end and lace down the first 3 or 4 loops.
2 piece end is joined by caribiners at
top and bottom of lace line.
Feed into Liner
Channel
Lacing is completed from ladder at
ground level. (Minimum 12’ ladder see
step #5, next page. For full lace, use
14’ ladder or taller.
In a strong breeze, attach safety rope to tail of end
panel to avoid “wind-whip” that could damage fabric
or injure workers.
Install Gabled End Fabric Panel (See top of page 18)
Push Purlin tool into metal
ring of fabric to slide panel
up and into Liner channel