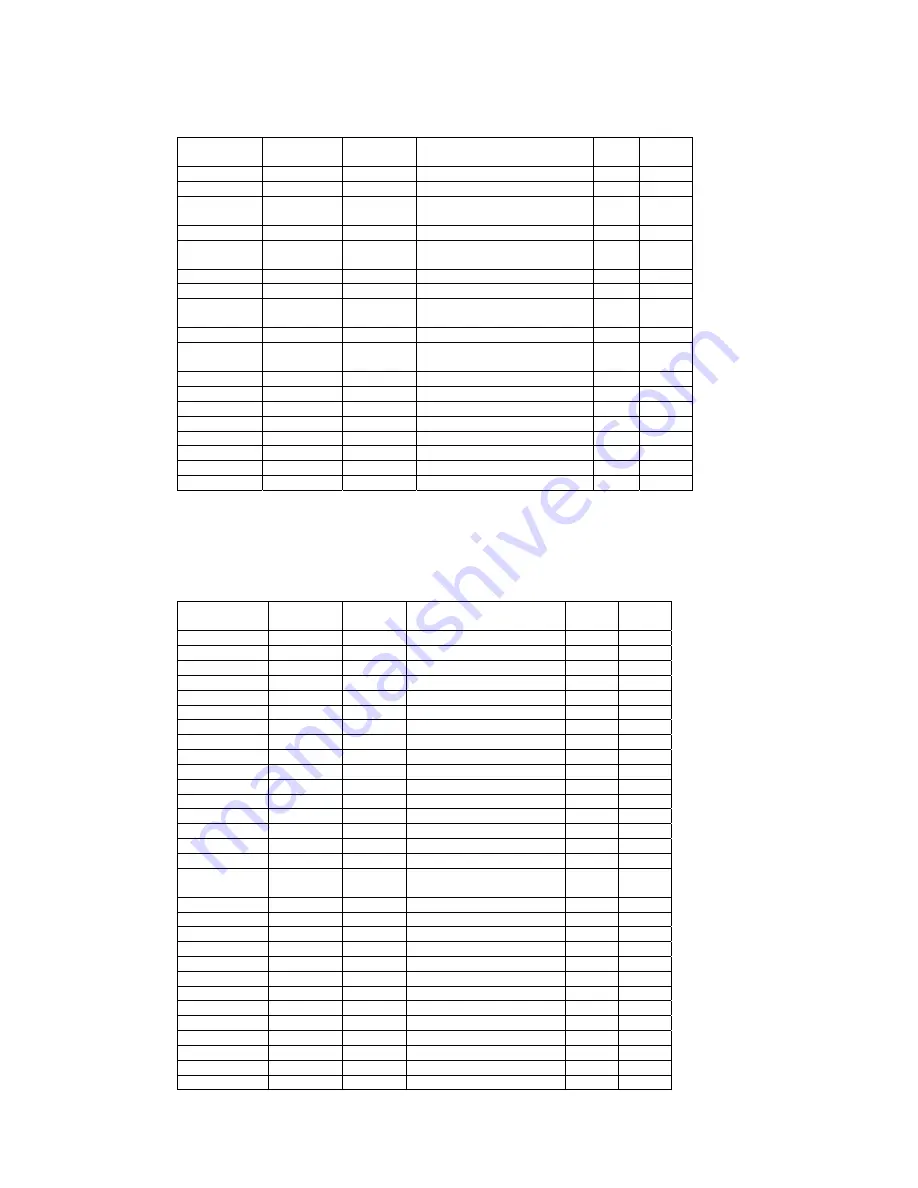
114
Paper Rack
PART NO.: N104-205U SAP: 100000000178
Reference
Number
Part
Number
SAP Parts
Name
QTY/
Assy
QTY
N104-193
5376
RU Removable Lever
1
N104-199U
130415
1~193
Rack Cover R Unit
1
N104-190BA
4537
RU Holding Plate R
Assembly
1
N104-191
4558
RU Support Plate
1
N104-192BA
4549
Tractor Support Plate R
Assembly
1
N104-199
4535 Rack
Cover
R
1
N104-200U
130416
1~194
Rack Cover L Unit
1
N104-190A
4564
RU Holding Plate L
Assembly
1
N104-191
4558
RU Support Plate
1
N104-192A
4579
Tractor Support Plate L
Assembly
1
N104-200
4563 Rack
Cover
L
1
N104-205A
1~195
Paper Rack Assembly
1
N104-205
4597 Paper
Rack
1
N104-206
4601 Sheet
Guide
1
N104-207
4605 Sheet
Guide
B
1
N104-208
4608 Paper
Support
2
N104-258
6534 Remove
Label
1
N104-259
6535
Remove Label B
1
Tractor Assembly
PART NO.: N104-6040A SAP: 100000000179
Reference
Number
Part
Number
SAP Parts
Name
QTY/
Assy
QTY
N104-255
6538
TR
Caution
Label
1
N104-256 130455
6537
TR
Position
Label
2
N104-301
4424
Tractor Cover L
1
N104-302
4425
Tractor Cover R
1
N104-303
4364
Tractor
plate
2
N104-304
4367
Tractor
shaft
1
N104-305
4373
Tractor Guide Shaft
2
N104-306
4426
Tractor Guide B
2
N104-307
4421
Tractor
Bearing
2
N104-308
4422
Tractor
Gear
1
N104-309A
1~198
Tractor R Assembly
1
N104-310
4385
Tractor Sub Frame L
1
N104-311
4402
Tractor sensor Frame
1
N104-312
4388
Tractor Lid L R
2
N104-312A
1~199
Tractor L Assembly
1
N104-314
4394
Tractor sensor PCB
1
N104-314A
1~200
Tractor sensor PCB
Assembly
1
N104-315
4406
Tractor sensor Cover
1
N104-322
6506
Tractor
PCB
Cover
1
N104-324
4398
Tractor Paper Sensor
1
N104K-M02
4379
Tractor Main Frame L
1
N104K-M08
4386
Tractor Knob L
1
N104K-M10
4408
Tractor Main Frame R
1
N104K-M11
4413
Tractor Sub Frame R
1
N104K-M12
4414
Tractor Knob R
1
4382
Tractor
Pulley
2
4383
Tractor Driving Belt
2
4390
Tractor
Pin
4
4391
Tractor
Spring
2
6404
Binder
1
Summary of Contents for Accel-7350
Page 1: ...1 Accel 7350 Dot Matrix Printer Service Manual Document 130034 ...
Page 24: ...23 Wiring Diagram ...
Page 25: ...24 Control Diagram ...
Page 36: ...35 Extra Dot Printing Improper character ...
Page 37: ...36 Incorrect Printing Irregular print data ...
Page 38: ...37 No LCD Display Half of the LCD lights up ...
Page 39: ...38 No LCD Display Completely blank ...
Page 40: ...39 Control Keys Not Functioning ...
Page 41: ...40 No Buzzer Abnormal Ribbon Feeding Causing abnormal carriage movement ...
Page 42: ...41 No Line Feed or Inconsistent Line Feeding ...
Page 43: ...42 Carriage Error ...
Page 44: ...43 ...
Page 46: ...45 Cover Open Error Will Not Cancel With Cover Closed ...
Page 47: ...46 No Fanfold Paper Reverse Line Feed ...
Page 48: ...47 Printing Does Not Stop After Paper Is Ejected ...
Page 49: ...48 Not Powering Up ...
Page 94: ...93 Indicator Circuit ...
Page 95: ...94 I F Circuit ...
Page 96: ...95 Slide SW Circuit ...
Page 97: ...96 Power Circuit ...
Page 98: ...97 Exploded View 1 6 Following pages require Legal size paper for printing ...
Page 99: ...98 Exploded View 2 6 ...
Page 100: ...99 Exploded View 3 6 ...
Page 101: ...100 Exploded View 4 6 ...
Page 102: ...101 Exploded View 5 6 ...
Page 103: ...102 Exploded View 6 6 ...
Page 119: ...126 ...