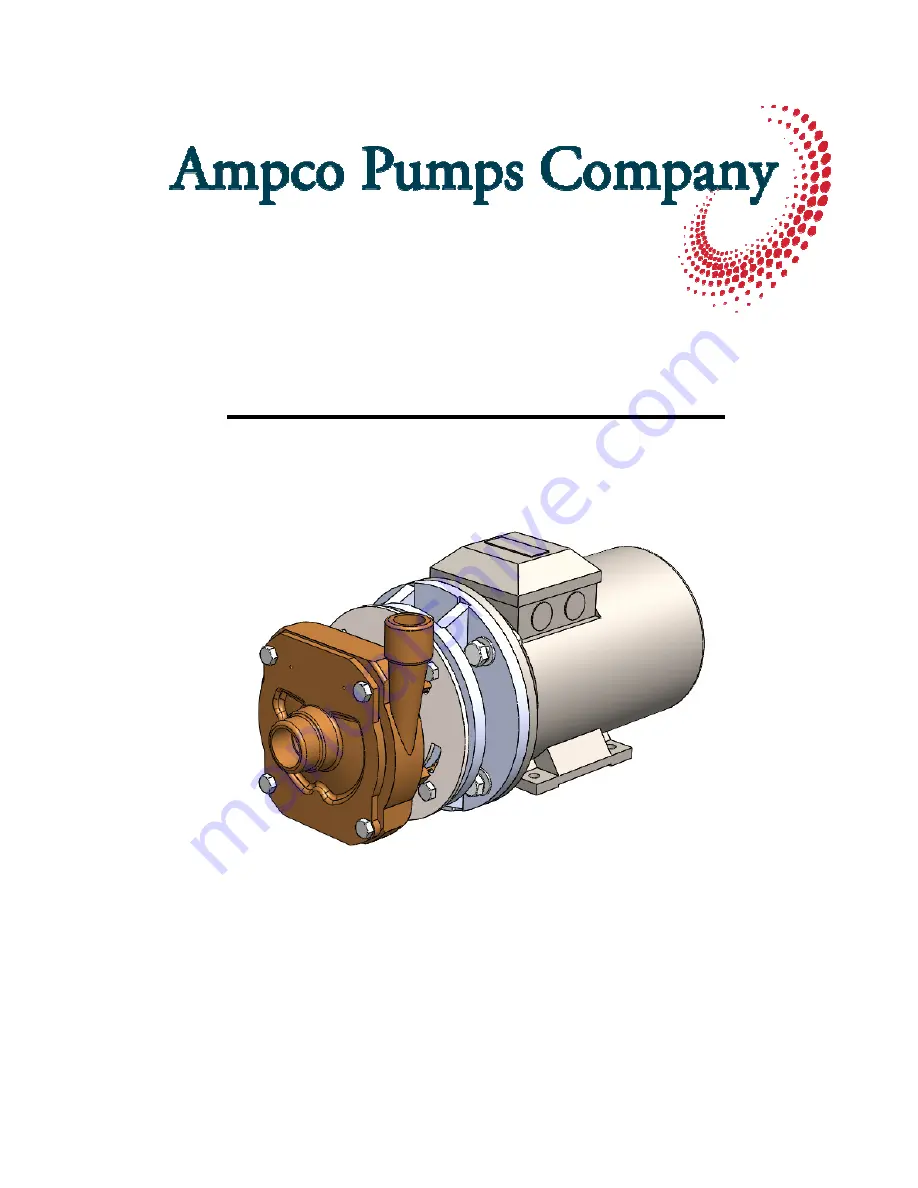
Ampco Pumps Company K-Series Metric Maintenance Manual M-033 Rev A 11.16
K-Series: Metric Components
Service Manual
This service manual includes installation, operation, and maintenance instructions for
Ampco Pump Company’s K-Series with IEC frame motor. Failure to learn the correct
procedures for installing and servicing the pump from this manual could result in equipment
failure.