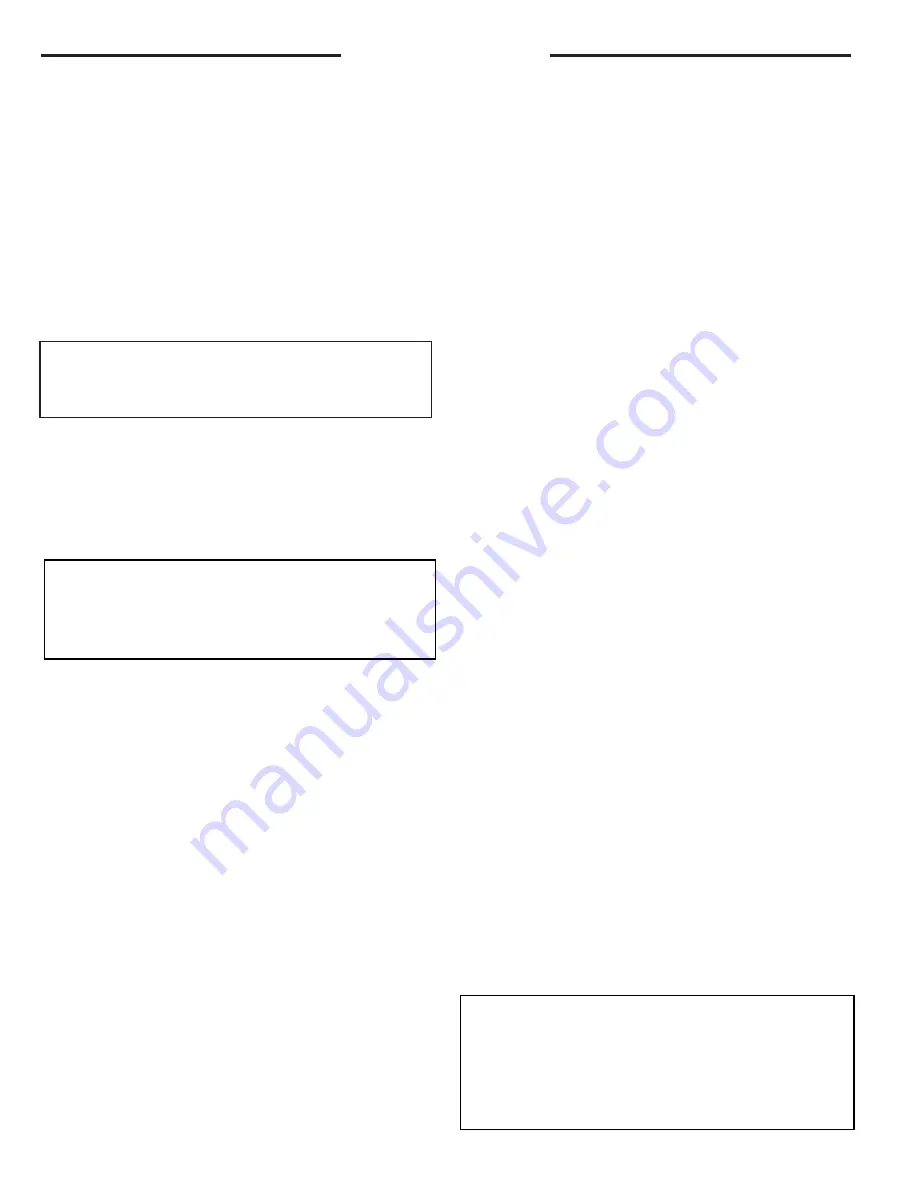
Page 22
Dwg. No. X664209 P01
ROUTINE MAINTENANCE BY OWNER
You can do some of the periodic maintenance functions for your
YCX-G unit yourself; this includes replacing the disposable or
cleaning the permanent air filters, cleaning the unit cabinet,
cleaning the condenser coil, and conducting a general unit
inspection on a regular basis.
When the system is in constant operation. In new homes,
check the filters every week for the first four (4) weeks.
If you have disposable-type filters, replace them with new filters
of the same type and size. Do not attempt to clean disposable
filters.
Permanent-type filters can be cleaned by washing them with a
mild detergent and water. Make sure that the filters are thor-
oughly dry before reinstalling them in the unit (or duct system).
NOTE: It may be necessary to replace permanent filters
annually if washing fails to clean the filter or if the filter shows
signs of deterioration. Be sure to use the same type and size
as was originally installed.
CONDENSER COIL
Unfiltered air circulates through the unit's condenser coil and can
cause the coil’s surface to become clogged with dust, dirt, etc.
To clean the coil, vertically (i.e., with the fins) stroke the coil
surface with a soft-bristled brush.
Be sure to keep all vegetation away from the condenser coil
area.
MAINTENANCE
MAINTENANCE PERFORMED BY SERVICEMAN--
COOLING SEASON
To keep your unit operating safely and efficiently, the manufac-
turer recommends that a qualified serviceman check the entire
system at least once each year and any other time that you feel
one is needed. Your serviceman should examine these areas of
your YCP-F unit:
●
filters (for cleaning or replacement)
●
motors and drive system components
●
economizer gaskets (for possible replacement)
●
safety controls (for mechanical cleaning)
●
electrical components and wiring (for possible replacement
and connection tightness)
●
condensate drain (for cleaning)
●
unit duct connections (to see that they are physically sound
and sealed to the unit casing)
●
unit mounting support (for structural integrity)
●
the unit (for obvious unit deterioration)
MAINTENANCE PERFORMED BY SERVICEMAN--
HEATING SEASON
Complete the unit inspections and service routines described
below at the beginning of each heating season.
●
Visually inspect the unit to ensure that the airflow required for
combustion and condenser coil is not obstructed from the unit.
●
Inspect the control panel wiring to verify that all electrical
connections are tight and that the wire insulation is intact.
●
Check the operation of the gas ignition system as follows:
Turn off the gas supply with the unit operating to verify that the
gas valve closes and that a reignition cycle is initiated by the
unit.
●
Visually inspect the inside of the burners and the burner ports
for deposit buildup and corrosion. Wipe and brush the inside
of the burner and the burner ports and then clean with a dry
cloth. If the deposit buildup or corrosion is excessive, replace
the burners.
FLUE CLEANING
Before each heating season, the flue should be inspected for
signs of flaking rust and soot deposits. Dirty flues should be
cleaned by qualified service personnel ONLY using the
following procedure:
1. Turn the room thermostat to the OFF position. Turn the main
power disconnect OFF. Turn the manual gas valve OFF.
2. Remove the flue cap, the lower access panel, and the upper
access panel.
3. Remove the combustion blower assembly from the fluebox.
Remove the flue box and the flue restrictors.
4. Remove all wires from the gas value while carefully noting
their location.
5. Disconnect the gas supply line from the valve.
6. Remove the manifold retaining screws and pull the burner-
manifold assembly from the heat exchanger.
7. Remove the inlet turbulators being careful not to break or
damage them.
8. Wipe the flue box and flue baffles clean with a clean, dry
cloth.
9. CAUTION: Never use combustible cleaning fluids on
any part of the furnace.
10. Replace all gaskets with new ones.
11. Replace all damaged or broken turbulators with new ones.
12. Reassemble the unit by reversing Steps 2 through 7 above.
Take care that all gaskets seat properly.
13. Check all wires for correct installation by referring to the
unit’s electrical wiring diagram.
14. Leak test all gas line connections with a soap and water
solution or the equivalent.
15. Reinstall the top and bottom access panels and the flue
stack.
16. Visually inspect the unit to ensure that the airflow opening for
combustion is not obstructed.
17. Follow the start-up procedure above to place the unit back in
service.
▲
WARNING:
DO NOT OPERATE THE UNIT
WITHOUT THE EVAPORATOR FAN ACCESS PANEL IN
PLACE. REINSTALL THE ACCESS PANEL AFTER
PERFORMING ANY MAINTENANCE PROCEDURES ON THE
FAN. OPERATING THE UNIT WITHOUT THE ACCESS
PANEL PROPERLY INSTALLED MAY RESULT IN SEVERE
PERSONAL INJURY OR DEATH.
▲
WARNING:
TO PREVENT AN EXPLOSION
OR POSSIBLE INJURY, DEATH AND EQUIPMENT DAMAGE,
DO NOT STORE COMBUSTIBLE MATERIALS, GASOLINE
OR OTHER FLAMMABLE VAPORS OR LIQUIDS NEAR THE
UNIT.