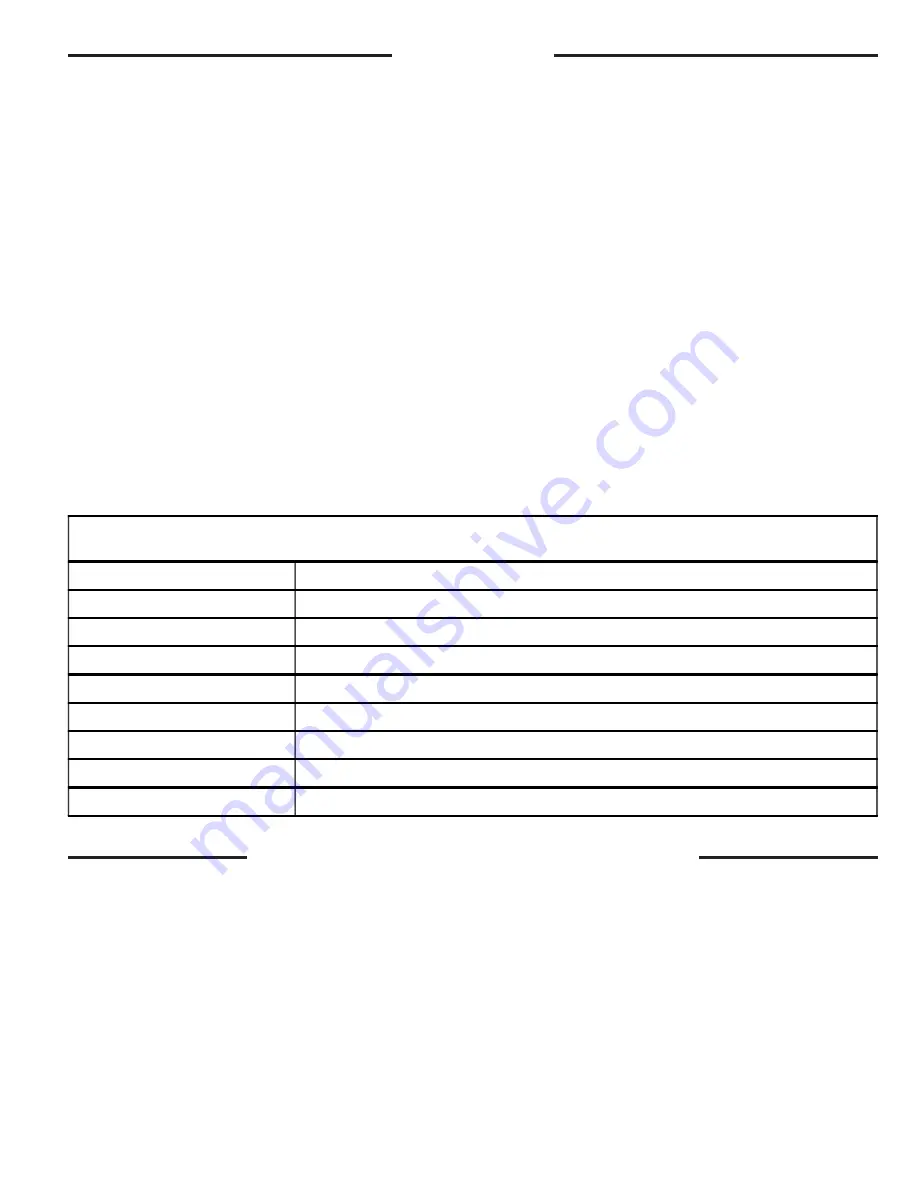
Dwg. No. X664209 P01
Page 19
FINAL INSTALLATION CHECKLIST
START - UP
8. Set the thermostat at the desired temperature setting and the
unit will function automatically.
STARTING THE UNIT IN THE GAS HEATING MODE
1. Check to make sure all grilles and registers are open and all unit
access doors are closed before start-up.
2. Purge the gas supply line of air by opening the union ahead of
the unit. When the odor of gas is detected, retighten the union
and wait five (5) minutes before proceeding.
3. Set the wall thermostat to its lowest position and place the fan
switch in the AUTO or ON position.
4. Open the main gas valve(s) and turn on the unit power supply.
5. Reset the heating temperature lever on the room thermostat at
the highest value above room temperature. The combustion
blower motor should energize. The main burners should light
within 20-25 seconds. Initial start may be delayed somewhat if
the unit has not been purged and air is trapped in the gas line.
NOTE: Blue smoke produced by the heat exchanger during the
initial burner firing is caused by a thin film of oil on the surface
of the heat exchanger. This oil will burn off quickly.
6. Cycle the thermostat OFF and ON a few times at a rate of not
more than once every thirty (30) seconds. Check both the
control operation and the burner operating conditions.
MANIFOLD PRESSURE
1. Connect a manometer to the pressure tap at the outlet side of
the unit’s gas valve. Read the manifold pressure with the main
burners firing.
2. If the manifold pressure reading does not match the value
indicated on the unit nameplate, the unit pressure regulator
must be adjusted as follows:
a. Remove the cover screw on the gas regulator located on the
front side of the unit’s gas valve.
b. Turn the adjusting screw clockwise to increase manifold
pressure or counterclockwise to decrease manifold pres-
sure.
3. Check the temperature rise during furnace operation to insure
that it falls within the range specified on the unit nameplate.
4. If the temperature rise noted is outside of the specified limits,
adjust the indoor air flow to cause the temperature rise of the
heat exchanger to fall within the required range.
●
Does the unit run and operate as described in the section on
“Sequence of Operation” in response to the room thermostat?
●
Are the condenser fan and indoor blower operating correctly with
proper rotation and without undue noise?
●
Is the compressor operating correctly and has the system been
checked with a charging chart?
●
Has the voltage and running current been checked to determine
if it is within limits?
●
Has the thermostat been checked for calibration and the air
discharge grilles adjusted to balance the system?
●
Has the ductwork been checked for air leaks and condensation?
●
Has the furnace manifold pressure been checked and adjusted
if necessary?
●
Has the heating air temperature rise been checked?
●
Has the unit been checked for tubing and sheet metal rattles?
Are there any other unusual noises to be checked?
●
Are all covers and panels in place and properly fastened?
●
Has the owner or maintenance personnel been given this manual
and the warranty? Has the owner or maintenance been in-
structed on proper operation and maintenance of this unit?
IGN LED DIAGNOSTIC INDICATOR
FLASHING SLOW
NORMAL CALL FOR HEAT
CONTINUOUS ON
NORMAL
CONTINUOUS OFF
CHECK POWER / INTERNAL FAILURE
2 FLASHES
SYSTEM LOCKOUT ( NO FLAME )
3 FLASHES
PRESSURE SWITCH PROBLEM
4 FLASHES
HIGH LIMIT (TCO) OPEN
5 FLASHES
FLAME SENSED WITH GAS VALVE OFF
6 FLASHES
FLAME ROLLOUT SWITCH (FL) OPEN
7 FLASHES
W1 & W2 SWAPPED