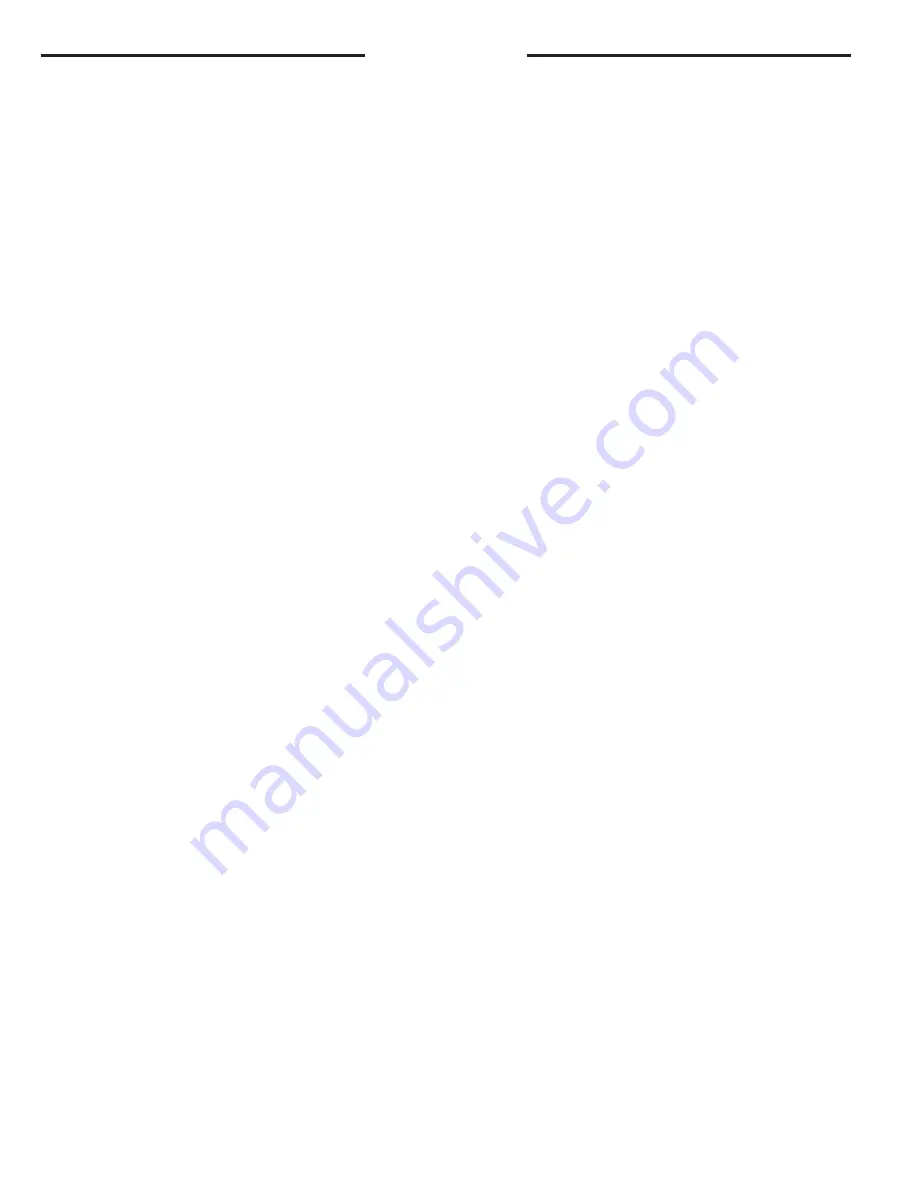
Page 18
Dwg. No. X664209 P01
START - UP
PRE-START QUICK CHECKLIST
●
Is the unit properly located and level with the proper clearance?
See Figure 4.
●
Is the duct work correctly sized, run, taped, insulated, and
weatherproofed with proper unit arrangement? See Ductwork
Installation section.
●
Is the gas piping correctly sized, run, trapped, and purged of air?
See Gas Piping section.
●
Is the condensate line properly sized, run, trapped, and pitched?
●
Is the filter of the correct size and number? Is it clean and in place?
●
Is the wiring properly sized and run according to the unit wiring
diagram?
●
Are all the wiring connections, including those in the unit, tight?
●
Has the unit been properly grounded and fused with the recom-
mended fuse size? See Wiring Data.
●
Is the thermostat level, correctly wired, well located, and set for
the proper heat anticipation?
●
Have the air conditioning systems been checked at the service
ports for charge and leak tested if necessary?
●
Does the condenser fan and indoor blower turn free without
rubbing, and are they tight on the shafts?
●
Has the indoor blower speed been determined and the proper
speed been set? See the Unit Wiring Diagram.
●
Has all work been done in accordance with applicable local and
national codes?
●
Are all covers and access panels in place to prevent air loss and
safety hazards?
STARTING THE UNIT IN THE COOLING MODE
CAUTION: Before starting the system on the cooling cycle, turn the
thermostat switch to OFF and close the unit disconnect switch. This
procedure energizes the compressor crankcase heater, vaporizing
any liquid refrigerant in the crankcase. This is a precaution against
foaming at startup which could damage the compressor bearings.
Allow the heater to operate a minimum of eight (8) hours.
NOTE: See the section on “Sequence of Operation” for a
description of the cooling operating sequence.
To start the unit in the cooling mode, set the thermostat system
switch to COOL and move the thermostat COOL indicator to a
setting below room temperature. The condenser (outdoor) fan
motor compressor and evaporator (indoor) fan motor will operate
automatically.
OPERATING PRESSURES
After the unit has operated in the cooling mode for a short period of
time, install pressure gauges on the gauge ports of the discharge
and suction line valves. Check the suction and discharge pressures
and compare them to the normal operating pressures provided in
the unit’s SERVICE FACTS.
NOTE: Do not use the pressures from the unit's SERVICE FACTS
to determine the unit refrigerant charge. The correct charge is
shown on the unit nameplate. To charge the system accurately,
weigh in the charge according to the unit nameplate.
VOLTAGE
With the compressor operating, check the line voltage at the unit.
The voltage should be within the range shown on the unit name-
plate. If low voltage is encountered, check the size and length of the
supply line from the main disconnect to the unit. The line may be
undersized for the length of the run.
COOLING SHUT DOWN
Place the system selector in the OFF position or reset thermostat at
a setting above room temperature.
Do not de-energize the main power disconnect except when unit is
to be serviced. Power is required to keep the heat pump compres-
sor warm and boil off refrigerant in the compressor.
HEATING CYCLE
NOTE: See Sequence of Heating Operation.
These units are equipped with a solid-state ignition control that
lights the burners each time the thermostat calls for heat. The
burners are extinguished during the OFF cycle.
The gas heating section of the unit can be started using the following
procedure:
1. Be sure the thermostat is at its lowest setting and the power to
the unit is off.
a. Turn the main shutoff valve on the gas supply line ON.
b. Turn or switch the manual valve on the combination gas
valve ON position.
2. Be sure the burner compartment access panel is in place.
a. Turn on the electrical power to the unit.
b. Turn the thermostat to the highest setting in the heating
cycle.
3. As the thermostat calls for heat, the system cycles as follows:
a. The combustion blower is energized.
b. The pressure switch is closed.
c. The gas valve opens and the ignitor lights the burner.
d. Cycle the thermostat on and off a few times to check out the
control system and burner operation characteristics.
4. With the burners operating, check the manifold pressure with a
manometer. Do not exceed recommended pressures.
5. Adjust the unit to obtain an air temperature rise with that
specified on the unit nameplate.
6. NOTE: For manifold pressures and orifice sizes for gas with
other BTU ratings, contact the local gas utility. Manifold
pressure should be 3.5 inches water column (+0.1). Input must
not exceed the value shown on the rating plate.
7. Set the heat anticipator of the thermostat to equal the amperage
draw of the gas valve, approximately 0.7.