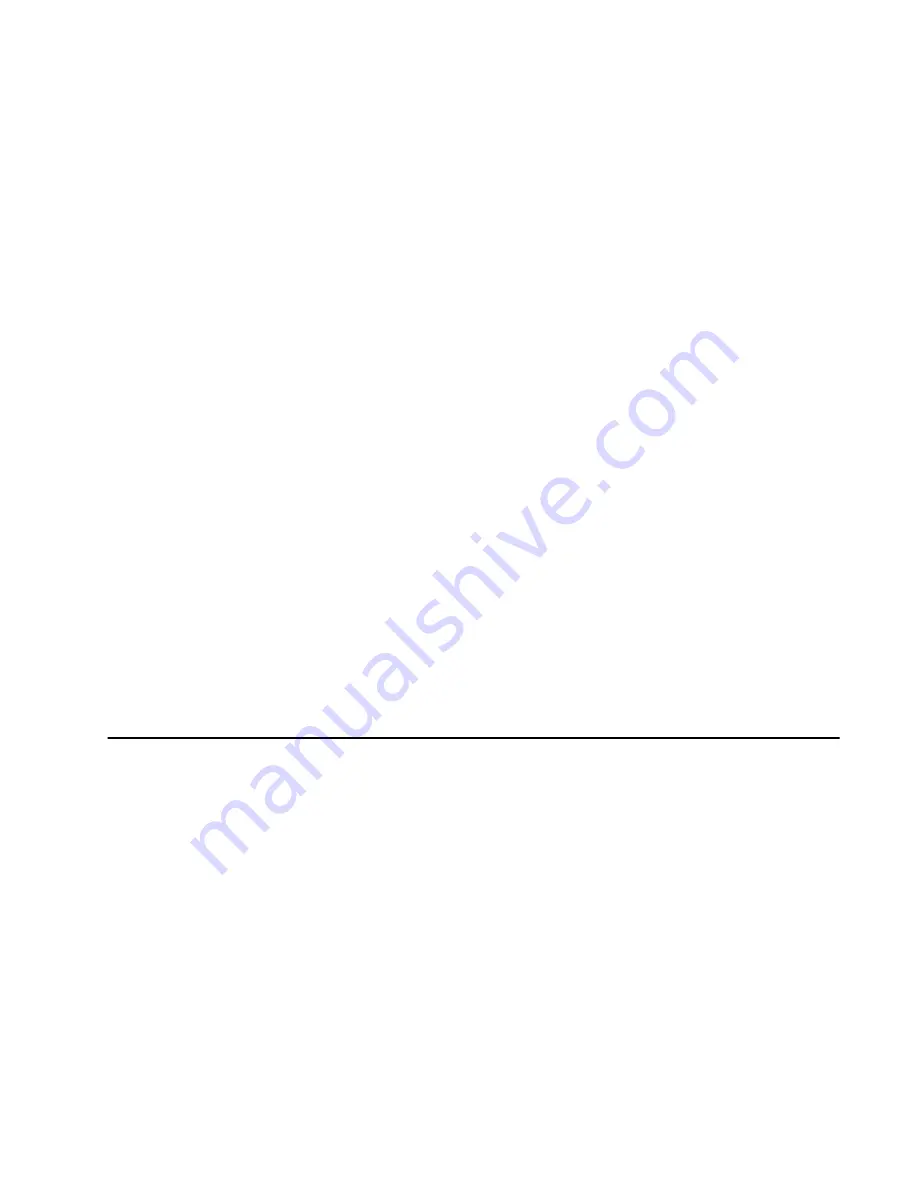
61
Input/Output (I/O) Board Input Description (“Red” light emitting diode [L.E.D.])
1.
FDRC – (RED L.E.D.)
This L.E.D. will indicate the status of the Front Doors. If the doors are closed,
then the L.E.D. is ON.
2.
FDRO – (RED L.E.D.)
This L.E.D. will indicate the status of the Front Doors. If the doors are open,
then the L.E.D. is ON.
3.
TBOL – (RED L.E.D.)
This L.E.D. will indicate the status of the Basket (tumbler) Overload Contact.
If the contact is closed, then the L.E.D. is ON. If it faults open, then the L.E.D.
is OFF.
4.
FNOL – (RED L.E.D.)
This L.E.D. will indicate the status of the Fan Overload Contact. If the contact
is closed, then the L.E.D. is ON. If it faults open, then the L.E.D. is OFF.
5.
RDWN – (RED L.E.D.)
This L.E.D. will indicate the status of the Rear Tilt. If the rear of the dryer is
down, then the L.E.D. is ON (optional).
6.
FDWN – (RED L.E.D.)
This L.E.D. will indicate the status of the Front Tilt. If the front of the dryer is
down, then the L.E.D. is ON (optional).
7.
RDRC – (RED L.E.D.)
This L.E.D. will indicate the status of the Rear Doors. If the doors are closed,
then the L.E.D. is ON.
OUTPUTS: (GREEN)
1.
R_HEAT - Rear Heat
2.
AUDIO ALERT - Horn On
3.
FWD - Basket (Tumbler) Forward
4.
REV - Basket (Tumbler) Reverse
5.
AIR JET - Air Jet On
6.
FAN - Blower Fan On
7.
F_HEAT - Front Heat
8.
PRG1 - Programmable Output #1
9.
PRG2 - Programmable Output #2
10. PRG3 - Programmable Output #3
11. PRG4 - Programmable Output #4
12. OCL1 - Open Collector Output #1
13. OCL2 - Open Collector Output #2
14. OCL3 - Open Collector Output #3
15. OCL4 - Open Collector Output #4
16. OCL5 - Open Collector Output #5
17. OCL6 - Open Collector Output #6
18. OCL7 - Open Collector Output #7
19. OCL8 - Open Collector Output #8
20. EOC - End Of Cycle Light
INPUTS: (RED)
1.
FDRC - Front Door Closed
2.
FDRO - Front Door Open
3.
TBOL - Basket (Tumbler) Overload
4.
FNOL - Fan Overload
5.
RDWN - Rear Down
6.
FDWN - Front Down
7.
RDRC - Rear Door Closed
8.
RDRO - Rear Door Open
9.
FAN - Blower Fan On
10. RBHL - Rear Burner High Limit
11
R_SS - Rear Sail Switch
12. FBHL - Front Burner High Limit
13. F_SS - Front Sail Switch
14. EXHL - Exhaust High Limit
15. DRY - Dry Enable Bit
16. LINT - Lint Drawer
17. R_HE - Rear Heat Enable
18. F_HE - Front Heat Enable
19. 24VIN - Control Voltage 24 Volts AC
20. SPR5 - Spare Input #5
21. SPR4 - Spare Input #4
22. SPR3 - Spare Input #3
23. SPR2 - Spare Input #2
24. SPR1 - Spare Input #1
25. RVLV - Rear Gas Valve
26. FVLV - Front Gas Valve
27. 24IN - Board 24 Volt AC
28. +5V - Regulated Voltage
29. Model - Communication
Summary of Contents for AD-310
Page 11: ...7 310 NON TILT GAS MODEL B DIMENSIONS AND COMPONENT LOCATION ...
Page 12: ...8 310 NON TILT STEAM MODEL ...
Page 14: ...10 1 Reassembly Instructions For Gas Dryer Shipped In Two 2 Pieces ...
Page 16: ...12 2 Reassembly Instructions For Steam Dryer Shipped In Two 2 Pieces ...
Page 22: ...18 ...
Page 23: ...19 ...
Page 24: ...20 ...
Page 64: ...60 B I O BOARD INPUT AND OUTPUT L E D INDICATORS ...
Page 80: ...76 ...