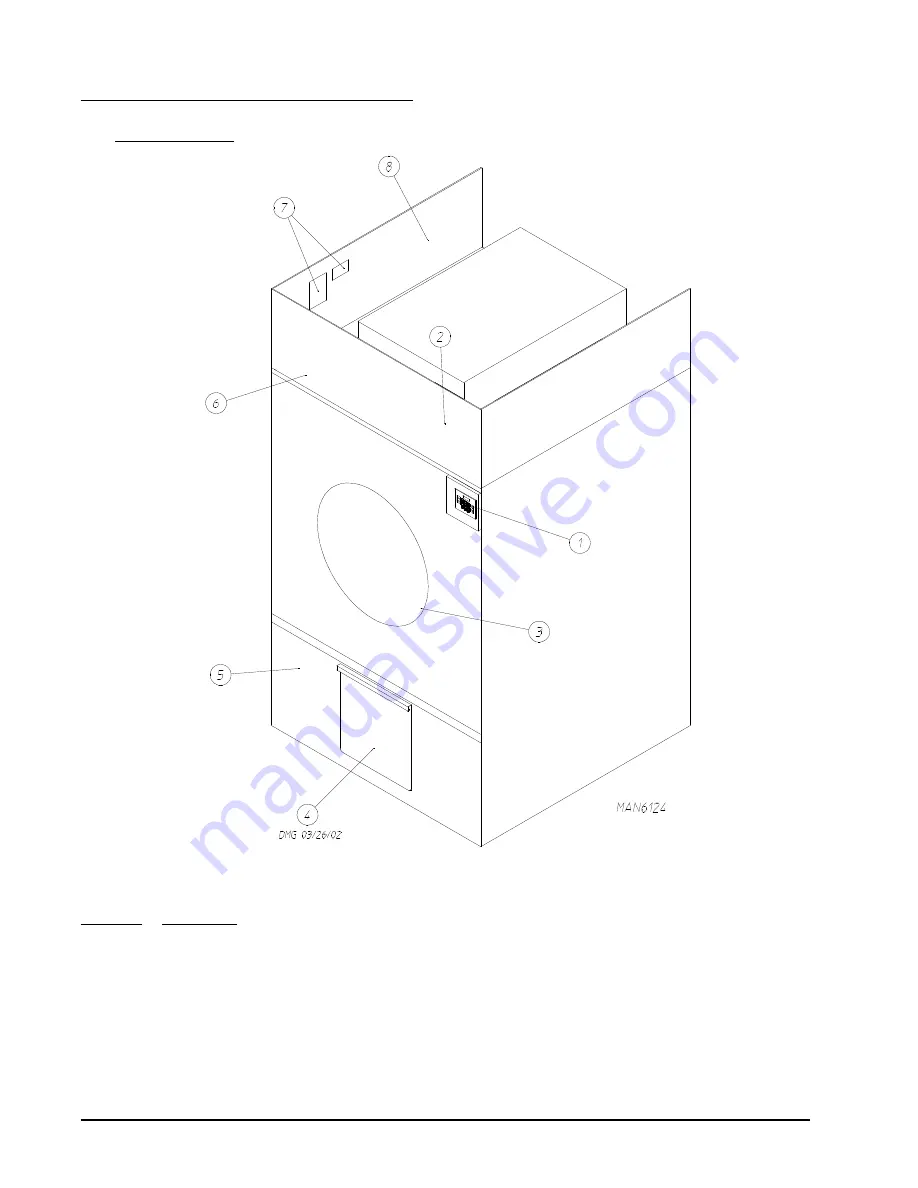
12
American Dryer Corp.
113289 - 6
D. COMPONENT IDENTIFICATION
1. Dryer Front View
Illus. No.
Description
1
Microprocessor Control/Keypad Panel Assembly (controls)
2
Control (top access) Door Assembly
3
Main Door Assembly
4
Lint Drawer
5
Lint Door
6
Wire Diagram (located behind control door)
7
Data Label and Installation Label
8
Top Console (module) Assembly
Summary of Contents for AD-202
Page 10: ...6 American Dryer Corp 113289 6 202 SPECIFICATIONS WITH MANUAL VERTICAL DOOR ...
Page 11: ...113289 6 www adclaundry com 7 202 SPECIFICATIONS STEAM WITH OPTIONAL STEEL STEAM COIL ...
Page 13: ...113289 6 www adclaundry com 9 202DR SPECIFICATIONS WITH MANUAL VERTICAL DOOR ...
Page 15: ...113289 6 www adclaundry com 11 202 AGA SPECIFICATIONS WITH MANUAL VERTICAL DOOR ...
Page 35: ...113289 6 www adclaundry com 31 ...
Page 62: ...ADC Part No 113289 6 02 07 15 ...