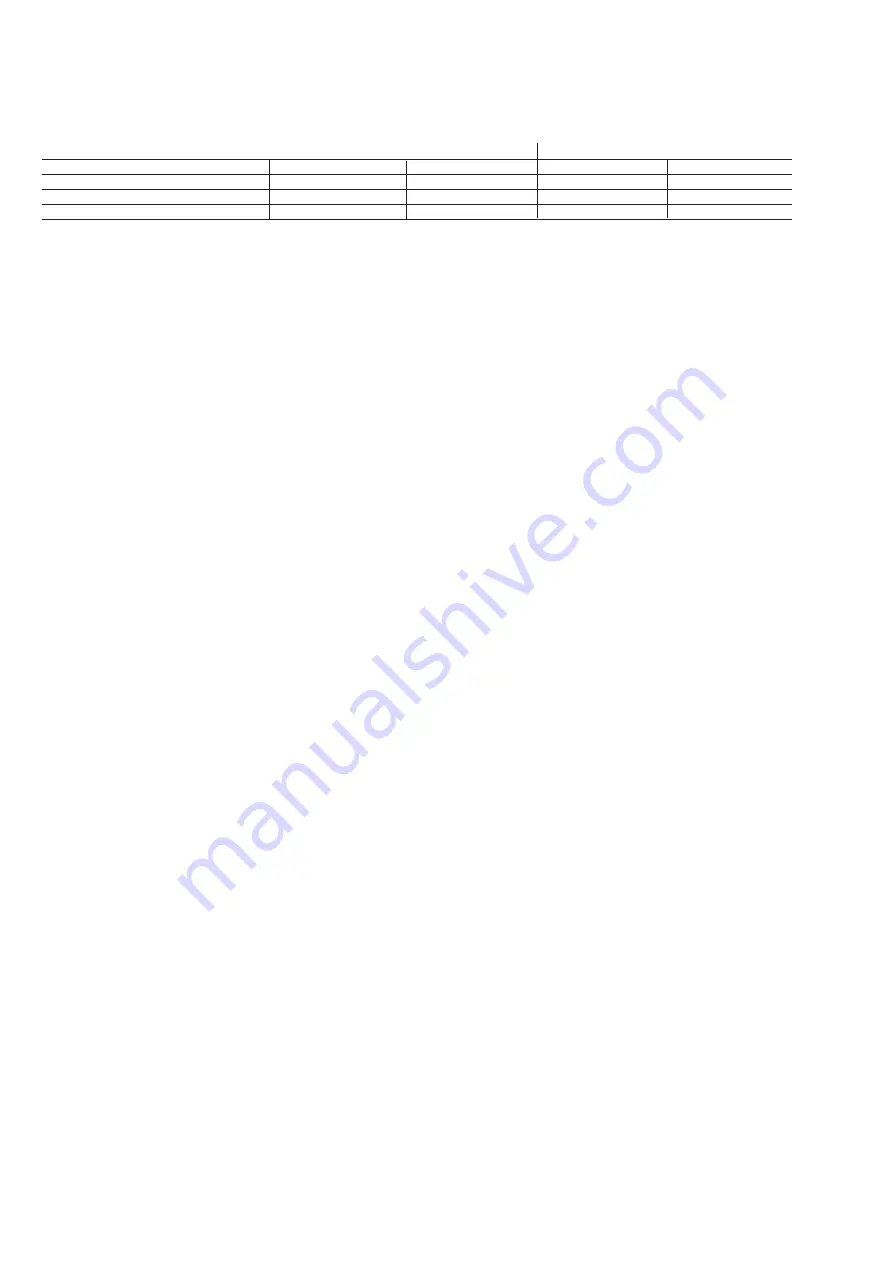
6
The Vision Compact heater may be installed
with or without a flue to atmosphere pro-
viding the air supply and building ventila-
tion requirements as stated in BS 6896:
1991 are complied with and providing due
consideration is given to the possibilities of
condensation forming on cold surfaces
when used as an unflued heater.
Where a ball guard is fitted to the heater a
downdraught diverter (Supplied as an
optional extra by Ambi-Rad) must be fitted
to the induced fan outlet by means of the
screws and clamp plates provided.
Unflued installation
Permanent ventilation required is as follows:
Natural ventilation
(To be fitted at high and low level with
minimum distance between of 3m).
Low level, when air change rate is less than
33m
3
/h/kW of total rated input, either:
1.4cm
2
for each 1m
3
/h/kW below
33m
3
/h/kW or 46cm
2
/kW of total rated
input.
High level, above areas where personnel are
working is as above.
Mechanical ventilation
Minimum proven air flow is 33m
3
/h/kW of
total rated heated input.
If the heater is installed without a flue,
ensure that combustion gases do not
impinge on combustible materials. The
maximum permitted temperature for such
materials is 50˚C. EN416.
The heater must have a baffle plate
(supplied) fitted to the fan outlet if it is to
be unflued.
Flued installations
Individually flued
A downdraught diverter (Supplied as an
optional extra by Ambi-Rad) must be fitted
to the induced fan outlet by means of the
screws and clamp plates provided.
The fan flued adaptors are designed to
accept 5” twin wall (recommended) or 5”
single wall, subject to necessary
precautions to prevent condensation
forming within the flue.
On individually flued heaters, the flue must
be terminated vertically and correctly sealed.
The maximum length of flue is 7m.
Draught diverter spillage checks
With the appliance in operation carry out a
flow visualisation check using a smoke
producing device e.g smoker match, puffer
or joss stick. The device shall produce an
even trace so that the flow can be observed
and the venting of the combustion products
assessed.
Check the flue performance at the draught
diverter. All of the smoke, apart from the
odd wisp which may be discounted, should
be drawn into the flue and removed to the
outside air.
If spillage occurs leave the appliance
operating for a further 10 minutes and
re-check. If there is still spillage switch off
the appliance and rectify the fault.
For further details see BS 5440-1:2000.
Permanent ventilation is required as follows:
Natural ventilation
(Preferably at low level) Up to and including
60kW: 4.5cm
2
/kW.
Over 60kW:270cm
2
+ 2.25cm
2
/kW in excess
of 60kW total rated input.
Forced ventilation
Minimum proven air flow is 2.35m
3
/h/kW of
total rated input. For detailed information
please refer to BS: 6896:1991, Installation of
Gas fired Overhead Radiant Heaters for
Industrial and Commercial heating (2nd and
3rd) family gases.
For calculation method for flue sizing see
Appendix.
Herringbone flue system
Where a number of individual heaters are to
be flued together via a herringbone system,
each heater must be fitted with a
herringbone damper assembly. The damper
assembly enables the correct vacuum to be
set for the heater, and is sized to accept
100mm diameter manifold pipe (all supplied
by Ambi-Rad at the design stage. Please
refer to the Herringbone Information
Manual (GB/HB/134/1103 if designing and
installing herringbone flue systems.
All flue pipes wether individual or
herringbone system should be adequately
supported at regular intervals from the
building structure and terminates externally
with a certified terminal.
10 Flue connection
Model
VC20
VC12
Gas type
G20
G31
G20
G31
Mass flow rate of flue gases (kg/s)
0.0113
0.0105
0.0077
0.0077
Flue gas temperature (˚C) @ fan outlet
234
228
163
164
Flue pressure (Pa) Positive
184
184
144
144
Flue technical details