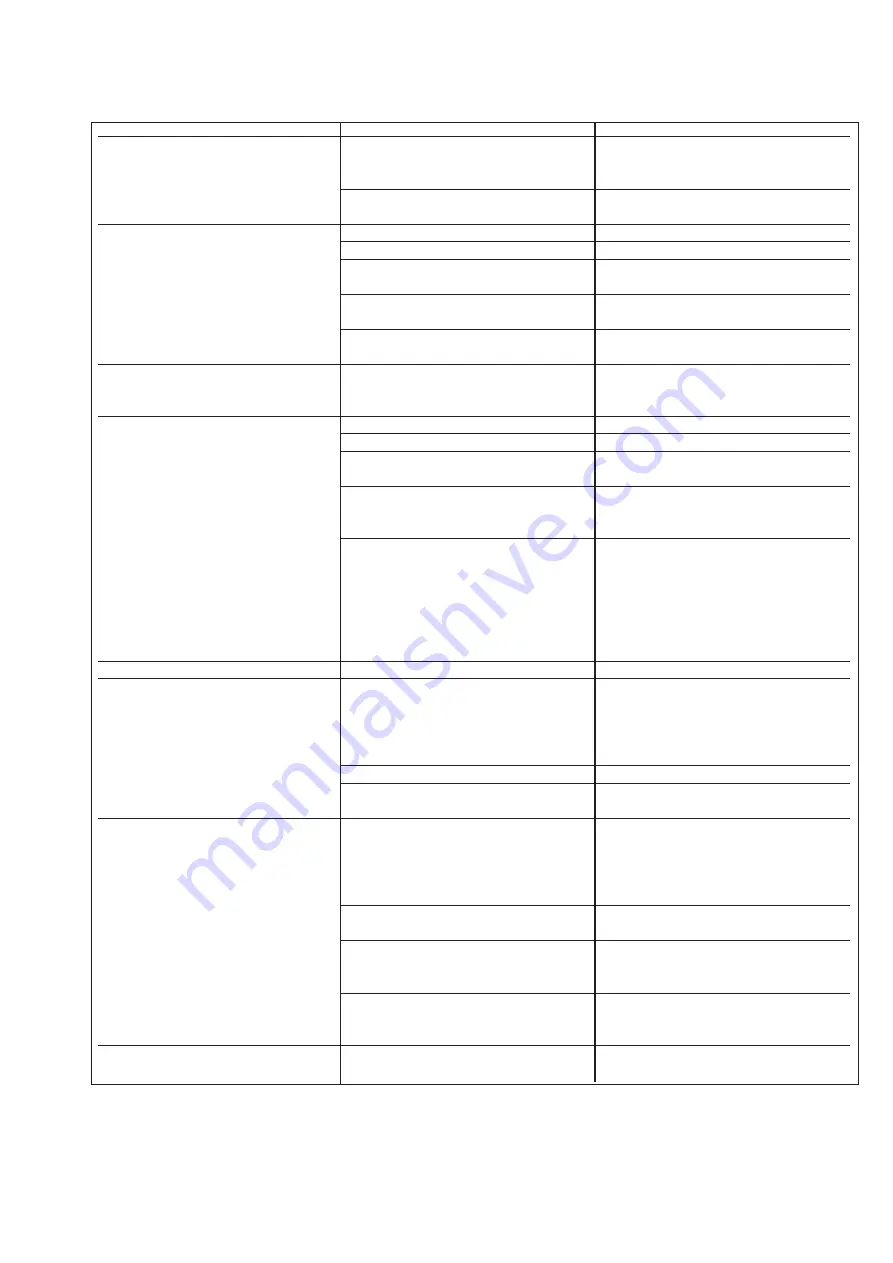
13
16 Trouble shooting checklist
Symptoms
Possible causes
Remedy
Burner will not start
Red ‘mains on’ does not illuminate.
External controls, thermostats, time switch etc.
Adjust controls.
not calling for heat.
Fuse blown.
Check for short circuit in wiring
or individual electrical components.
Red light illuminates.
Fan’s connector plug not fully engaged.
Engage securely.
Loose electrical connection.
Check all connections.
Fan seized or faulty motor.
Replace fan, recommission heater,
checking gas pressure settings.
Sequence controller relay failing
Check vacuum switch is satisfactory,
to pull in and/or hold in.
replace sequence controller.
Vacuum switch not returning to normal
Replace vacuum switch.
(switch off) position.
HB Herringbone system only.
Fan tripped out on overload.
Check overload setting: single phase 3 phase
0.8 amp. Reset button on in control panel.
Check for build up of condensate in fan casing.
Fan starts but burner does not attempt ignition. Insufficient vacuum generated by fan.
Clean fan blades with soft bristle.
Blocked emitter tube.
Clean emitter tube internally.
Combustion chamber cover permitting
Examine condition of sealing gasket, tighten
air leakage.
down lid securely.
Vacuum impulse line between combustion
Fix securely in place.
chamber and vacuum switch insecure
or defective.
Vacuum switch ‘pulls in’ but electronic sequence
Replace burner sequence controller unit but
controller does not proceed to programme
first check that the cause of failure is not a
ignition sequence.
short on output circuit, by measuring resistance
between pins 2 and 7 of burner control unit
plug. A reading of 10,000 ohms indicates short
circuit on gas valve burner indicator light or
associated wiring.
HB Herringbone system only.
Leaks in joint separation in manifold system.
Reseal or reconnect.
Burner proceeds to ignition stage (normally
No spark.
Check electrode for cracks – replace if necessary.
indicated by audible spark valve energised
Check high tension connections are secure.
and ‘burner on’ light illuminated) but burner
Check spark gap is 3.5 ± 0.5mm. If no high
does not light.
tension output from electronic controller,
replace controller.
Gas safety valve faulty or defective.
Replace solenoid operator section of gas valve.
Insufficient gas pressure.
Set burner pressure to that indicated on data
badge (see commissioning).
Burner lights but shuts down after
Inadequate flame signal. This can be verified
Replace electrode. Check connections to
a few seconds.
by connecting a sensitive micrometer in
electrodes and terminal 4 of electric sequence
series with the violet wire which passes through
controller plug. Replace the electronic
the combustion chamber bulkhead. The correct
sequence controller.
reading should be 6µA ± 1µA.
Flame unstable.
Check cleanliness of burner and set burner
pressure as indicated on data badge.
Inadequate gas supply. Observe burner
If gas pressure drops below that indicated on
gas pressure with all heaters operating.
the data badge, examine gas supply pipework
for excessive pressure loss.
Insufficient vacuum at combustion chamber
Clean fan blades with soft bristle brush.
causing vacuum switch to cut off.
Inspect tube internally and clean if necessary
(see servicing instructions).
Heater shuts down after operating
Refer to above.
If problem persists, replace vacuum switch.
for a period of time.