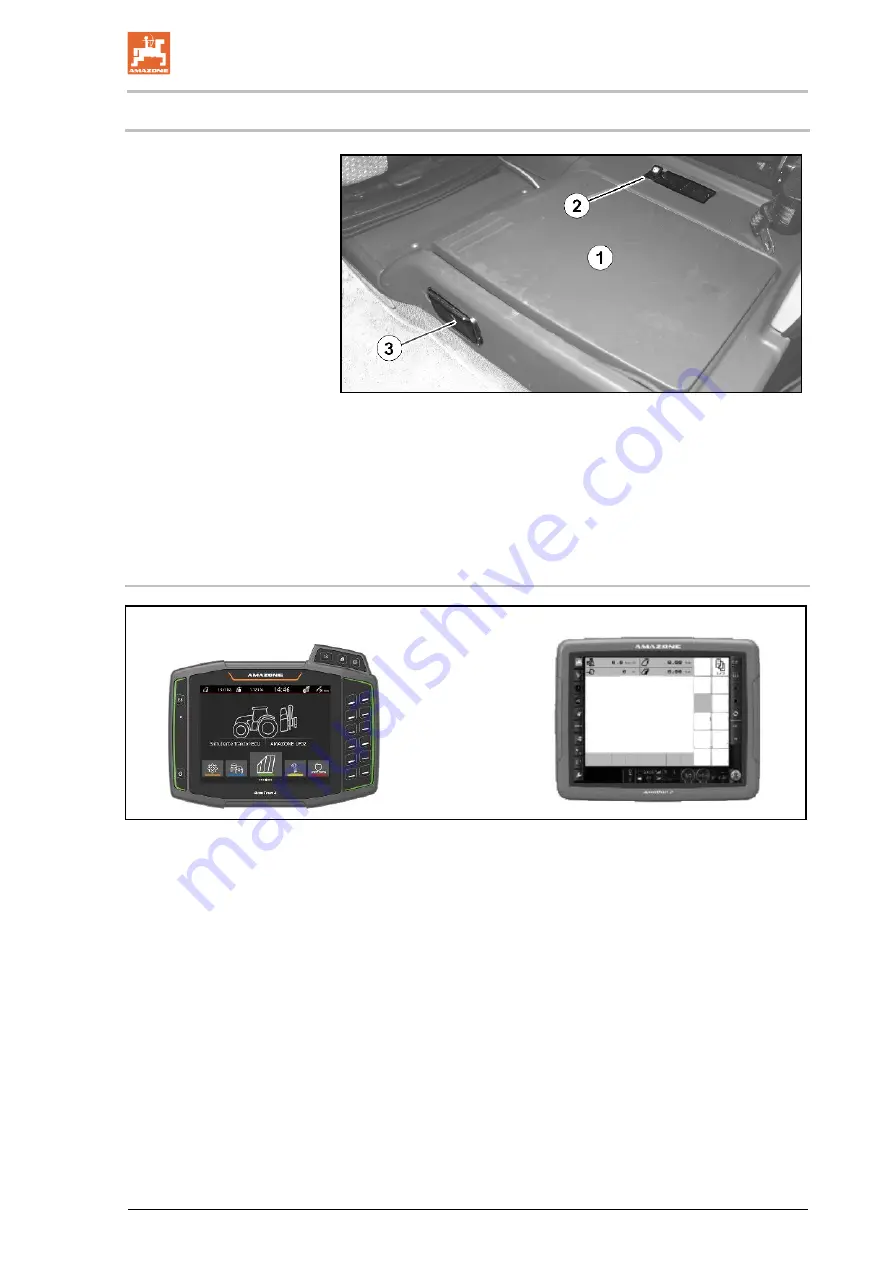
Structure and function, carrier vehicle
Pantera 4504 CP plus BAG0230.2 07.21
81
5.14.9
164B
Cooling compartment and ashtray
Under the helpers seat:
(1) Cooling compartment
(2) Switch for the cooling compartment
(3) Ashtray
5.14.10
165B
AmaTron / AmaPad control terminal to control the field sprayer
AmaTron 4
AmaPad 2
Base functions:
entry of the data in the spraying technology.
entering the job-related data.
controlling the field sprayer to change the spray rate used in
spraying operation.
the operation of all functions on the sprayer boom.
the monitoring of the field sprayer during spraying operation.
GPS options
Fully automatic part width section control
Parallel driving aid (integrated in the GPS switch application)
Summary of Contents for Pantera 4504
Page 2: ...2 Pantera 4504 CP plus BAG0230 2 07 21 Leipzig Plagwitz 1872 ...
Page 20: ...General Safety Instructions 20 Pantera 4504 CP plus BAG0230 2 07 21 ...
Page 263: ...Diagrams and overviews Pantera 4504 CP plus BAG0230 2 07 21 263 ...
Page 277: ...Spray table Pantera BAG0230 2 07 21 277 ...
Page 286: ......