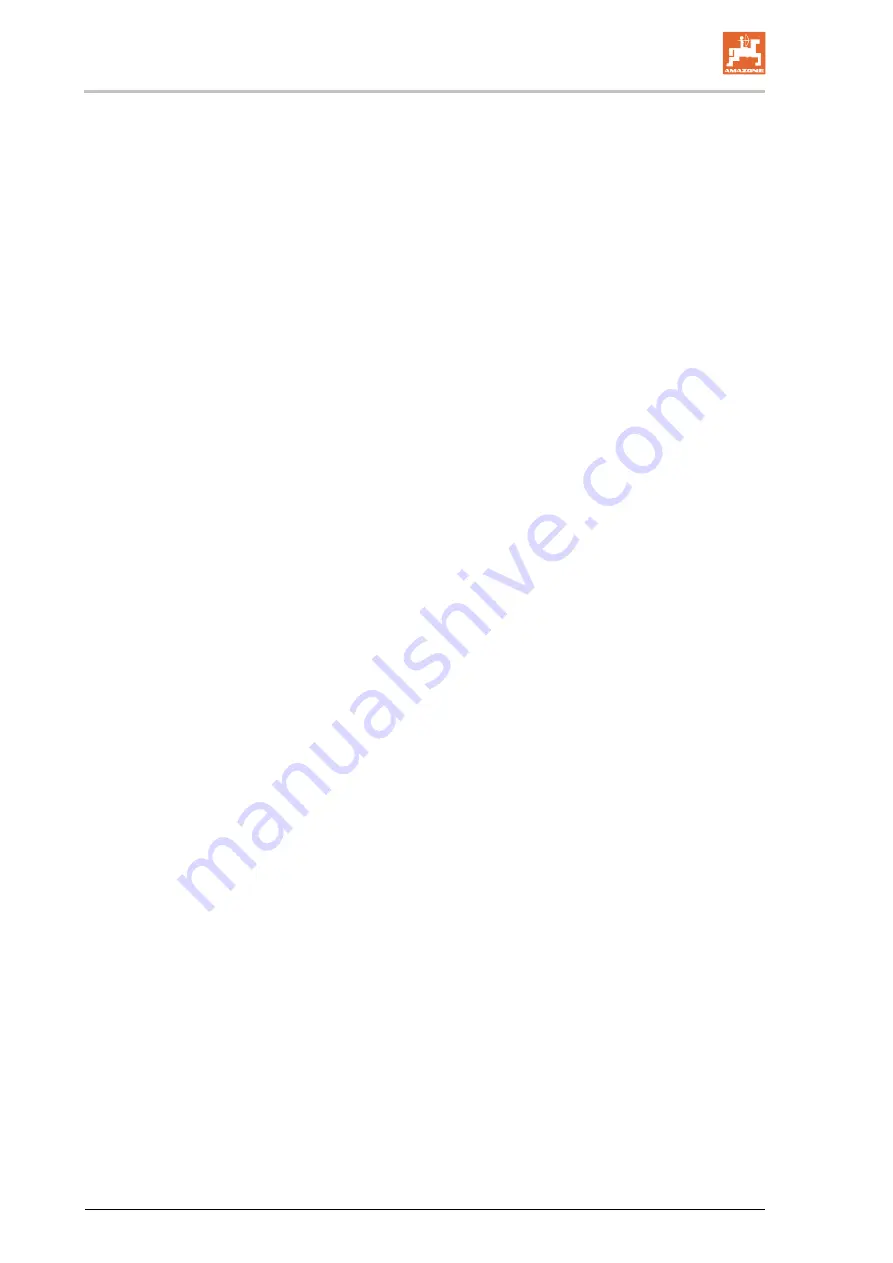
Table of Contents
6
Cenius 4002-2T BAG0100.2 04.13
5.8
Running gear......................................................................................................................... 51
5.9
Tensioned crosspiece ........................................................................................................... 51
5.10
Stand ..................................................................................................................................... 52
5.11
Feeler wheels (Option).......................................................................................................... 52
5.12
Rear harrow (option) ............................................................................................................. 53
5.13
GreenDrill catch crop sowing unit ......................................................................................... 54
5.14
Safety chain for implements without brake system............................................................... 54
6
Commissioning ......................................................................................... 55
6.1
Checking the suitability of the tractor .................................................................................... 56
6.1.1
Calculating the actual values for the total tractor weight, tractor axle loads and load
capacities, as well as the minimum ballast ........................................................................... 56
6.1.2
Requirements for tractor operation with attached machines................................................. 60
6.1.3
Machines without their own brake system ............................................................................ 60
6.2
Securing the tractor/machine against unintentional start-up and rolling ............................... 61
7
Coupling and uncoupling the machine ................................................... 62
7.1
Coupling the machine ........................................................................................................... 63
7.2
Uncoupling the machine........................................................................................................ 65
8
Adjustments............................................................................................... 66
8.1
Working depth of the tines .................................................................................................... 66
8.1.1
Mechanical depth adjustment ............................................................................................... 66
8.1.2
Hydraulic depth adjustment................................................................................................... 67
8.2
Working depth of the levelling unit ........................................................................................ 68
8.3
Adjusting the stripper ............................................................................................................ 68
8.4
Setting the feeler wheels....................................................................................................... 69
9
Transportation ........................................................................................... 70
9.1
Changing from working to transport position ........................................................................ 71
10
Use of the machine ................................................................................... 72
10.1
Changing from transport to working position ........................................................................ 72
10.2
Operation............................................................................................................................... 72
10.3
Headland ............................................................................................................................... 72
11
Faults.......................................................................................................... 73
12
Cleaning, maintenance and repairs ......................................................... 74
12.1
Cleaning ................................................................................................................................ 75
12.2
Lubrication instructions ......................................................................................................... 75
12.3
Maintenance plan - overview ................................................................................................ 78
12.4
Installing and removing the tines........................................................................................... 79
12.5
Changing the coulters ........................................................................................................... 79
12.5.1
Changing the Vario-Clip coulters .......................................................................................... 79
12.6
Replace the tension springs of the overload safety device (workshop work) ....................... 79
12.7
Installing and removing the disc segments (workshop work) ............................................... 80
12.8
Replacing discs (workshop work).......................................................................................... 81
12.9
Tine connection ..................................................................................................................... 81
12.10
Roller connection................................................................................................................... 81
12.11
Disc carrier connection.......................................................................................................... 82
12.12
Hydraulic cylinder for folding ................................................................................................. 82
12.13
Tyres/wheels ......................................................................................................................... 83
12.13.1
Tyre pressures ...................................................................................................................... 83
12.13.2
Mounting tyres (workshop work) ........................................................................................... 84