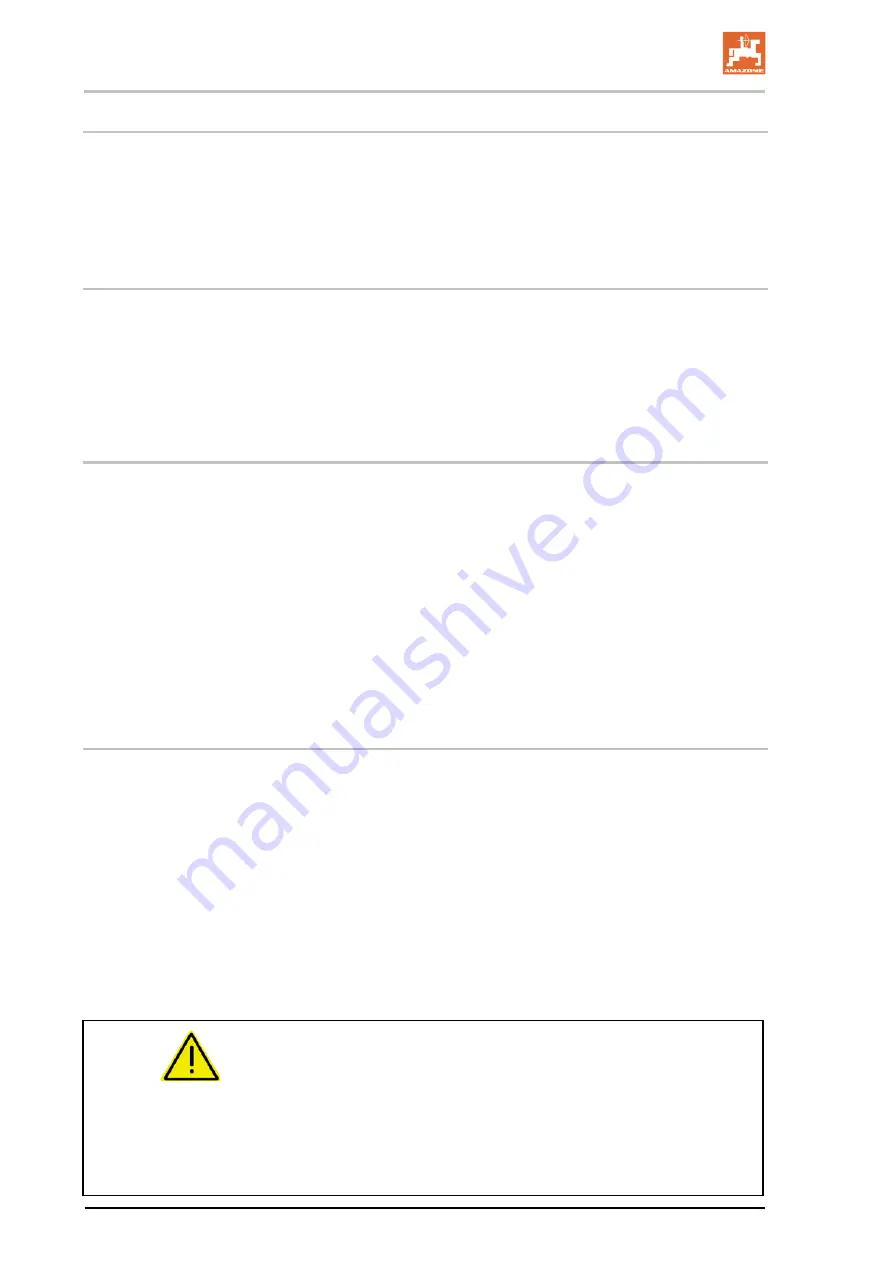
General safety instructions
2.7
Safety measures in normal operation
Only operate the machine if all the safety and protection equipment is
fully functional.
Check the machine at least once a day for visible damage and check
the function of the safety and protection equipment.
2.8
Dangers from residual energy
Note that there may be residual mechanical, hydraulic, pneumatic and
electrical/electronic energy at the machine.
Use appropriate measures to inform the operating personnel. You can
find detailed information in the relevant sections of this operating
manual.
2.9
Maintenance and repair work, fault elimination
Carry out prescribed setting, maintenance and inspection work in a
timely manner.
Secure all media such as compressed air and the hydraulic system
against unintentional start-up.
Carefully fix and secure larger subassemblies to lifting gear when
carrying out replacement work.
Regularly check that bolted connections are firmly secured and tight-
en if necessary.
When the maintenance work is completed, check the function of the
safety devices.
2.10
Constructive changes
You may make no changes, expansions or modifications to the ma-
chine without the authorisation of AMAZONEN-WERKE. This is also
valid when welding support parts.
Any expansion or modification work shall require the written approval
of AMAZONEN-WERKE. Only use the modification and accessory
parts released by AMAZONEN-WERKE so that the operating permit,
for example, remains valid in accordance with national and interna-
tional regulations.
Vehicles with an official type approval or with equipment connected to
a vehicle with a valid type approval or approval for road transport
according to the German road traffic regulations must be in the state
specified by the approval.
WARNING
Risk of being crushed, cut, caught, drawn in or struck if support-
ing parts break.
It is forbidden to:
•
Drill holes in the frame or on the chassis.
•
Increasing the size of existing holes on the frame or the chassis.
•
Welding support parts.
14
Catros BAG0155.4 05.19
Summary of Contents for Catros 4002-2TS
Page 115: ...Cleaning maintenance and repairs Catros BAG0155 4 05 19 115...
Page 116: ......