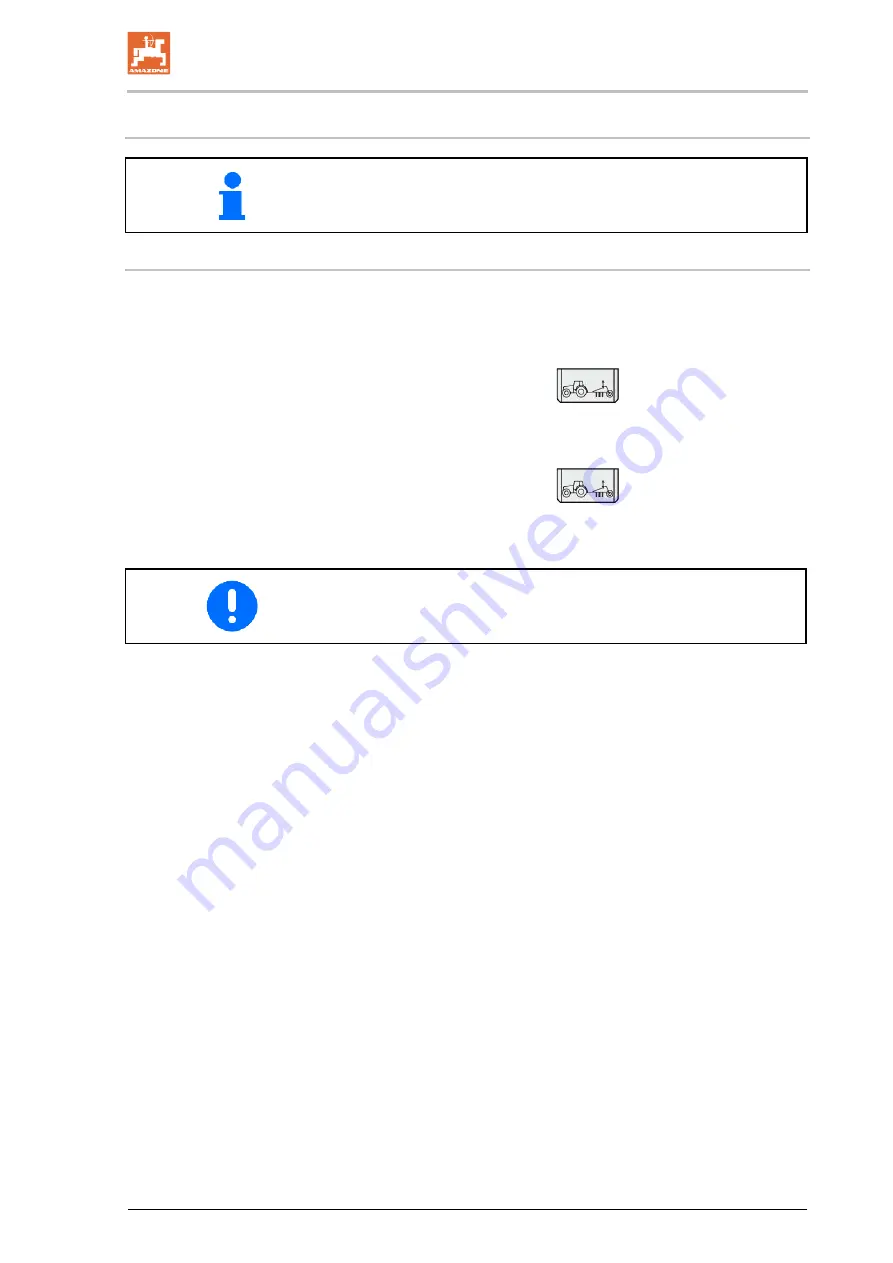
Use of the Implement
Catros02-T BAG0078.3 03.14
63
10.2
Use in the field
The lifting wing spindles of the implement near the upper link of the
tractor must be adjusted so that the frame is parallel to the soil sur-
face longitudinally and transversely during operation!
10.3 Headland
turning
When turning through a curve at the headland, the disk rows must be
raised to prevent transverse stresses.
Before turning in headland:
Activate tractor control unit
.
Raise the implement.
After turning in headland:
Activate tractor control unit
.
Work
now
continues.
Only use in headland when the direction of the implement corre-
sponds to the working direction.
Summary of Contents for Catros 3002-T
Page 75: ...Catros02 T BAG0078 3 03 14 75 ...