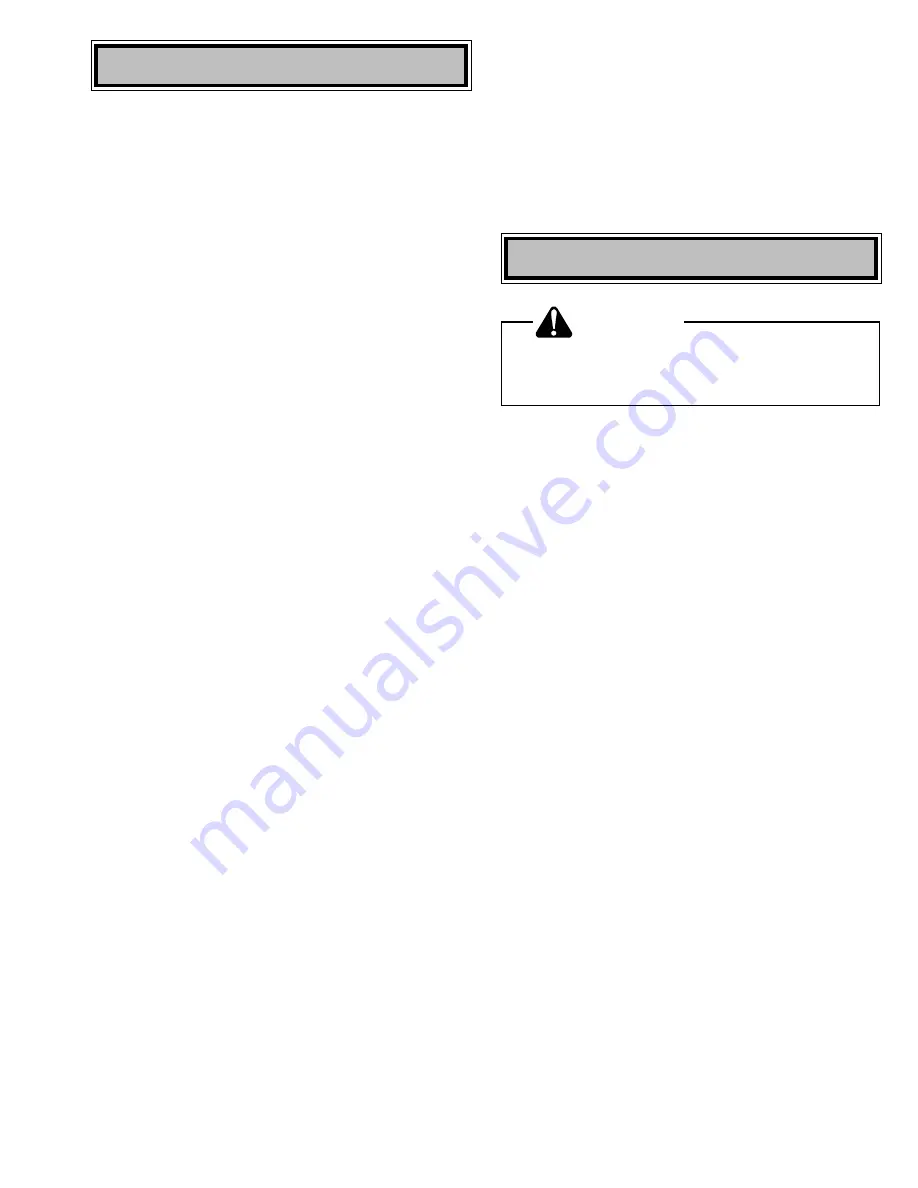
3
3
3. The paint finish of a filter drier must remain intact after
brazing. Repaint or treat with rust preventative, if paint
is chipped or burned.
SWEAT CONNECTIONS AT THE INDOOR COIL
Check the indoor coil liquid and vapor line diameter. A
bushing or coupling may be needed to match the line sizes
used. If mix matching to a restrictor orifice indoor coil,
check the “Specification Sheet” for the proper orifice size
to be used with this outdoor unit.
II. Safe Refrigerant Handling
WARNING
To avoid possible explosion, death, or
injury; practice safe handling of
refrigerants.
While these items will not cover every conceivable situa-
tion, they should serve as a useful guide:
Refrigerants are heavier than air. They can “push out”
the oxygen in your lungs or in any enclosed
space. To avoid possible death or difficulty in
breathing:
–
Never sniff refrigerant.
–
Never purge refrigerant into an enclosed room or
space. In fact, all refrigerants must, by law, be
reclaimed.
–
If an indoor leak is suspected, thoroughly ventilate
the area before beginning work.
–
Liquid refrigerant can be very cold. To avoid
possible frostbite or blindness, avoid contact and
wear gloves and goggles. If liquid refrigerant does
contact your skin or eyes, get medical help imme-
diately.
–
Always follow Environmental Protection Agency
(EPA) regulations. Never burn refrigerant, as
poisonous gas will be produced.
To avoid a possible explosion, use refrigerant cyl-
inders properly:
–
If you must heat a cylinder for faster charging,
partly immerse it in warm water. Never apply
flame or steam to the cylinder.
–
Store cylinders in a cool, dry place. Never use a
cylinder as a platform or a roller.
–
Never add anything other than R-22 to an R-22
cylinder.
–
Never fill a cylinder more than 80% full of liquid
refrigerant.
–
When removing refrigerant from a system, use
only returnable (not disposable) service cylinders.
Check the cylinder for its pressure rating and
hydrostatic test date. Check the cylinder for any
damage which may lead to a leak or explosion. If
in doubt, do not use the cylinder.
I. Refrigerant Piping
REFRIGERANT LINE SIZING
See unit “Specification Sheet” for required line sizes. Be
sure to use the correct size as using smaller vapor lines
can decrease unit performance. These sizes are suitable
for line lengths of fifty feet or less. It also assumes that the
indoor coil will not be more than forty feet above or below
the outdoor unit. Longer runs and greater lifts are not
recommended.
ROUTING OF REFRIGERANT LINES
All of the vapor line must be insulated. The insulation must
include a vapor barrier.
The liquid line must be outside of the vapor line’s insula-
tion.
If part of the liquid line must run through an area that will
be hotter than 120°F, then that portion of the liquid line
must be insulated.
Avoid burying refrigerant lines. If you must bury them, first
dig the trench so that it gradually slopes toward the
compressor (at least 1 inch per 10 feet). Then, insulate the
liquid and suction lines separately. Enclose all under-
ground portions of the refrigerant lines in waterproof
material (conduit or pipe). If the lines must pass under or
through a concrete slab, be sure they are adequately
protected.
Seal the holes where the refrigerant piping enters the
building.
Be careful not to kink or dent the refrigerant lines. Kinked
or dented lines will cause poor performance or compressor
damage.
FILTER DRIER INSTALLATION
1. A filter drier must always be installed with a new
outdoor unit for the compressor warranty to be in
effect.
2. Units are shipped with a bi-flow liquid line filter drier
and it must be installed in the liquid line either near the
outdoor unit or near the indoor coil.
3. A bi-flow filter drier equivalent to a Sporlan HPC-163-
S-HH is recommended for clean up after a compressor
burnout.
SWEAT CONNECTIONS AT THE UNIT
IMPORTANT: To avoid overheating of the service valve
while brazing, wrap the valve body with a wet rag, or use a
thermal heat trap compound as recommended by the
compound manufacturer.
1. The ends of the refrigerant lines must be cut square,
deburred, cleaned, and be round and free from nicks
or dents. Any other condition increases the chance of
a refrigerant leak.
2. After brazing, quench the joints with water or a wet
cloth. This will also help prevent overheating of the
service valve.