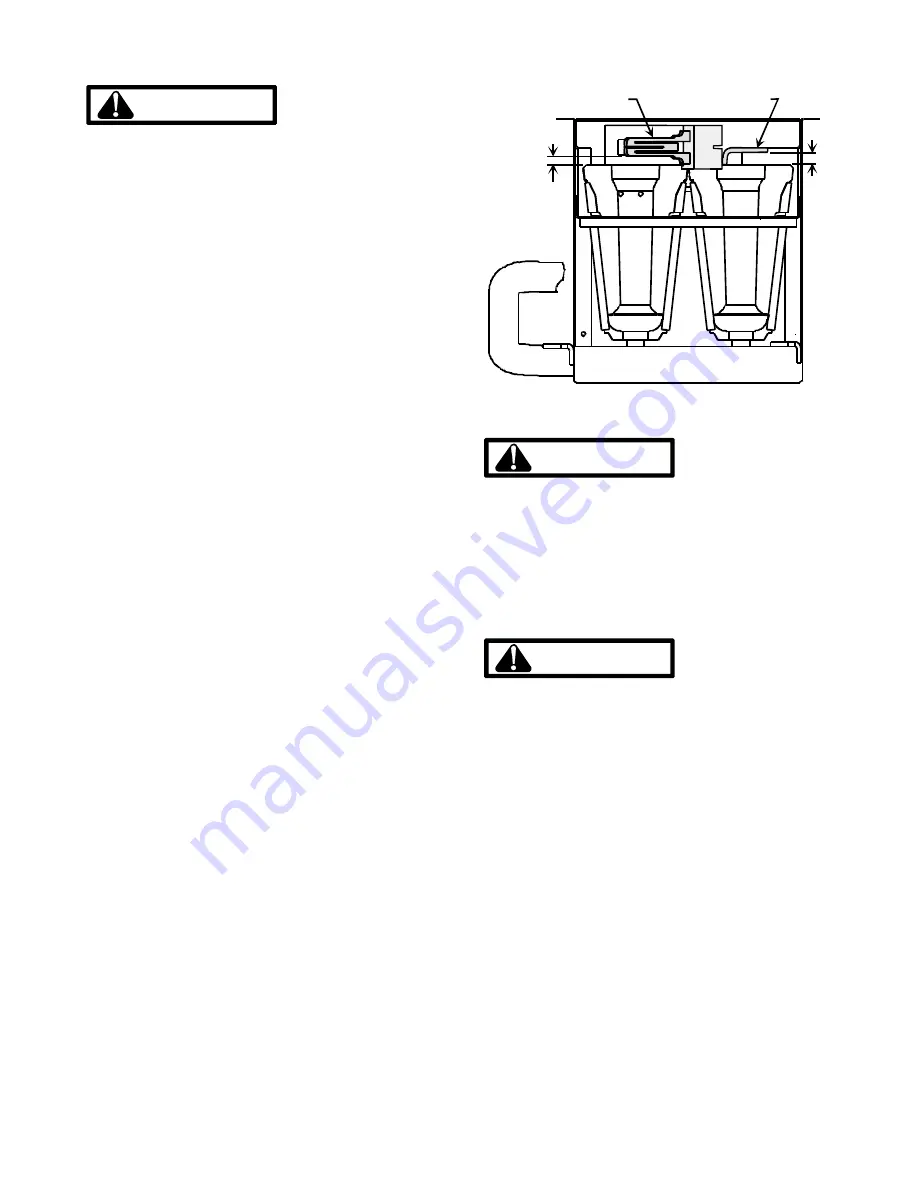
83
Rev. 2
SERVICING
WARNING
LINE VOLTAGE NOW PRESENT.
These tests must be completed within a given time frame
due to the operation of the ignition control. See "Sequence
of Operation" section for timing chart.
1. Check for 120 volts from Line 1 (BK6 wire) to line 2 neu-
tral (WH-33 wire) at the ignition control. No voltage - check
the door switch connections and wire harness for conti-
nuity.
2. Check for 24 volts from W to C at the thermostat con-
nections on the ignition control. No voltage - check trans-
former, room thermostat, and wiring.
3. Check for 120 volts to the induced draft blower by mea-
suring voltage between IND (VT-55) and neutral. No volt-
age - check for pressure switch stuck closed. If pres-
sure switch in N.O. position replace ignition control.
4. If voltage is present in Steps 1 through 3 and the in-
duced draft blower is operating, check for 120 volts to
the ignitor during the 17 second preheat cycle. If the
flame switch has not transferred, the control will con-
tinue to power the ignitor until the flame switch trans-
fers, or for 90 seconds. Voltage will be present for one
second after the gas valve has opened. Measure voltage
between terminals IGN (RD-22) and neutral. No voltage -
check pressure switch.
5. Seventeen seconds after a call for heat begin checking
for 24 volts to the gas valve. Measure voltage from termi-
nal 5 (YL-8 wire) to terminal 3 (RD-5) on the gas valve.
No voltage - check flame switch and ignitor position.
6. If proof of flame was established 120 volts will be pro-
vided to the air circulation blower 45 seconds after the
gas valve opens. Check for 120 volts from the CIR termi-
nal (WH) wire to the heat terminal on the ignition control.
No voltage - replace ignition control.
Note: If cycling the ignition control during testing, the flame
switch must be allow to cool and switch back to the N.C.
position before the next ignition attempt.
S-14
CHECKING FLAME SENSOR - FLAME REC-
TIFICATION - IGNITION CONTROL MOD-
ULE
A flame sensing device is used in conjunction with the igni-
tion control module to prove combustion. If proof of flame is
not present the control will de-energize the gas valve and
"retry" for ignition or lockout.
The following drawings illustrate from a bottom view, the ap-
proximate distances for the ignitor and flame sensor to the
gas inshot burner. You will note they are in the main burner
stream, not in the carry over ports as shown in the following
figure.
1/4
± .1/16
3/8"
± .1/16"
Ignitor
(All Models)
Flame Sensor
(50A50 models)
Models with Integrated Ignition Control & Flame
Sensor Probe
WARNING
Disconnect Electrical Power Supply:
1. Disconnect the flame sensor BU-36 wire from the sen-
sor terminal.
2. Connect a micro-amp meter in series with this wire and
the sensor terminal.
3. Be sure the negative side of the meter is to BU-36 wire
and the positive side of the meter is to sensor terminal.
WARNING
LINE VOLTAGE NOW PRESENT.
4. Place the unit into a heating cycle.
5. As soon as flame is established a micro-amp reading
should be evident once proof of flame (micro-amp read-
ing) is established, the hot surface ignitor will be de-
energized.
6. The Integrated Ignition controls will have 1 to 4 micro-
amps. If the micro-amp reading is less than the mini-
mum specified, check for high resistance wiring con-
nections, sensor to burner gap, dirty flame sensor, or
poor grounding.
7. If absolutely no reading, check for continuity on all com-
ponents and if good - replace ignition control module.
Note: Contaminated fuel or combustion air can create a
nearly invisible coating on the flame sensor. This coating
works as an insulator causing a loss in the flame sense
signal. If this situation occurs the flame sensor must be
cleaned with emery cloth or steel wool.