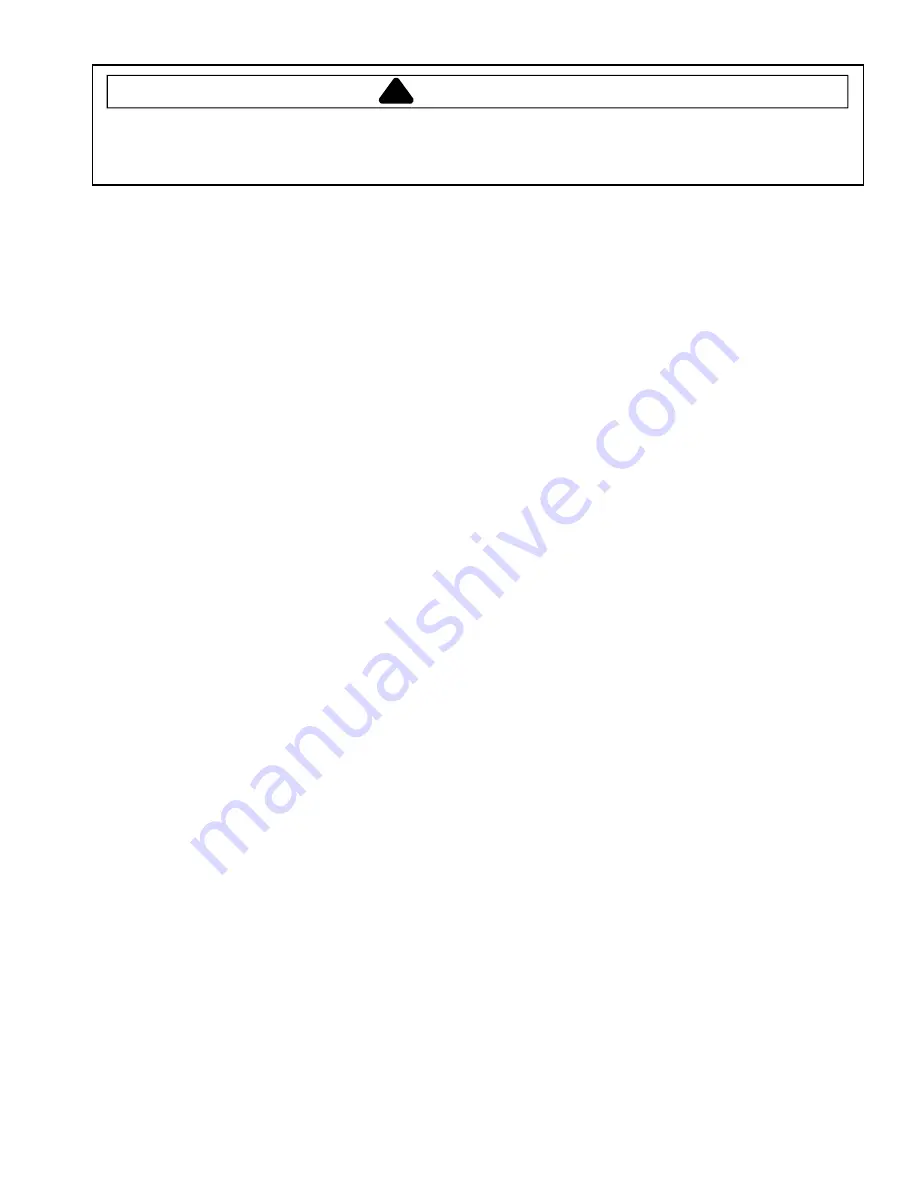
December 1997
49
RS1300003 Rev. 0
Charging
NOTE: Do not use captured or recycled refrigerant in
Amana units. Captured or recycled refrigerant
voids any warranty.
NOTE: Charge system with exact amount of refrigerant.
See technical data sheet or refer to unit serial
plate for correct refrigerant charge. Inaccurately
charged system will cause future problems.
To charge system:
1. Close valves “A” to vacuum pump and “C” to vacuum
gauge and “E” to low side manifold gauge.
2. Set scale on dial-a-charge cylinder for corresponding
HFC134a pressure reading.
3. Open valve “F” to charging cylinder and let exact
amount of refrigerant flow from cylinder into system.
Close valve.
Low side gauge pressure should rise shortly after
opening charging cylinder valve as system pressure
equalizes through capillary tube.
If pressure does not equalize, a restriction typically
exists at capillary/drier braze joint.
4. If pressure equalizes, open valve “E” to low side
manifold gauge and pinch off high side drier process
tube.
5. Start compressor and draw remaining refrigerant
from charging hoses and manifold into compressor
through compressor process tube.
6. To check high side, pinch-off drier process tube.
Close valve “D” to high side gauge. If high side
pressure rises, repeat high side pinch-off and open
valve “D”. Repeat until high side pinch-off does not
leak.
7. Pinch-off compressor process tube and remove
charging hose. Braze stub closed while compressor is
operating.
8. Disconnect power. Remove charging hose and braze
high side drier process tube closed.
9.
Recheck for refrigerant leaks.
Service Procedures
!
WARNING
To avoid risk of electrical shock, personal injury, or death, disconnect electrical power source to unit and discharge
capacitor through a 10,000 ohm resistor before attempting to service, unless test procedures require power to be
connected. Ensure all ground wires are connected before certifying unit as repaired and/or operational.
Refrigerant Charge
Refrigerant charge in all capillary tube systems is
critical and exact amount is required for proper
performance. Factory charges are shown on serial
plate. Do not use refrigerant other than shown on
serial plate.