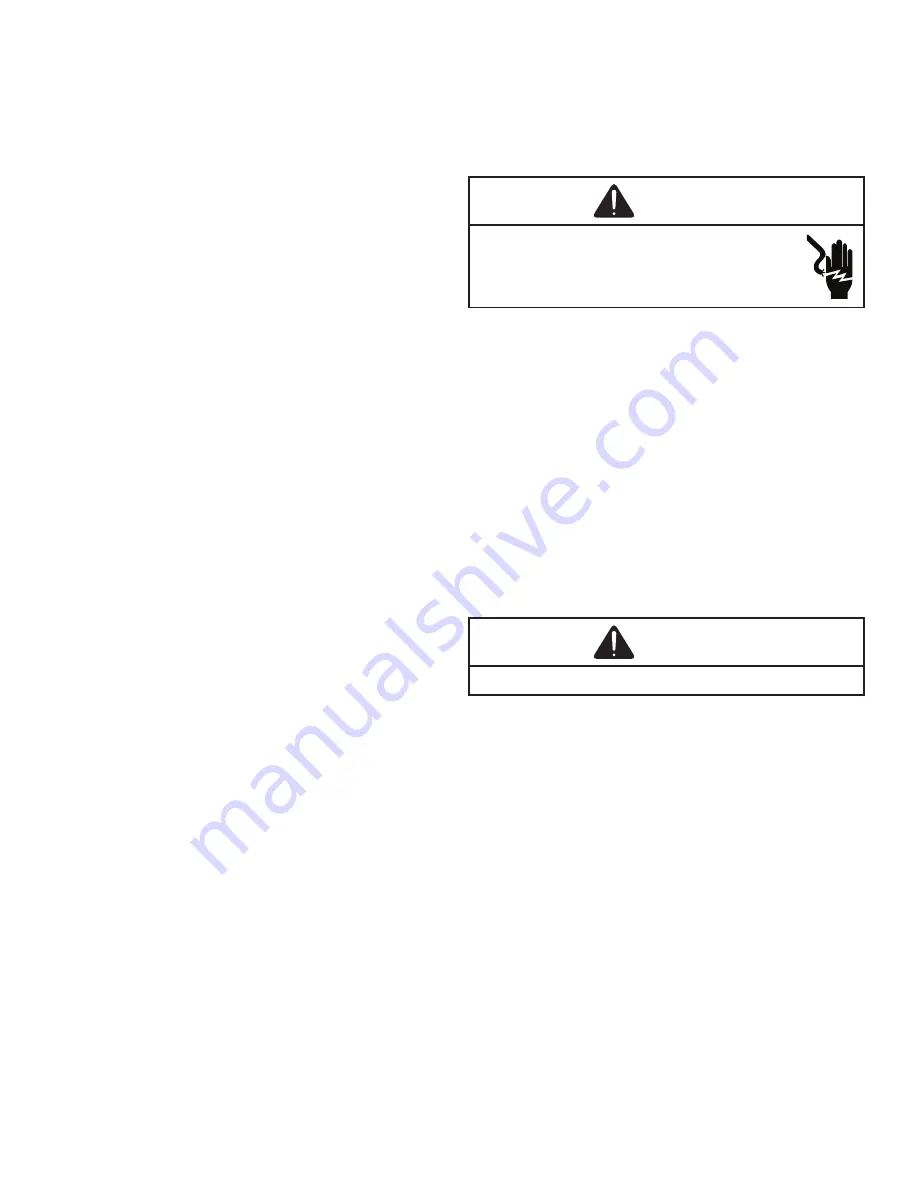
SERVICING
18
Unloader Test Procedure
(2 Stage Compressors Only)
A nominal 24-volt direct current coil activates the
compressor internal unloader solenoid. The input control
circuit voltage must be 18 to 28 volt ac. (remove) The
coil power requirement is 5 VA. The external electrical
connection is made with a molded plug assembly. This plug
contains a full wave rectifier to supply direct current to the
unloader coil. The measured DC voltage at the connectors
in the plug should be 15 to 27 volt dc.
Unloader Test Procedure
If it is suspected that the unloader is not working, the
following methods may be used to verify operation.
1. Operate the system and measure compressor
amperage. Cycle the unloader ON and OFF at 10
second intervals. The compressor amperage should
increase when switching from part-load to full-load
and decrease when switching from full-load to part-
load. The percent change depends on the operating
conditions and voltage, but should be at least 25
percent.
2. If step one does not give the expected results, shut
unit off. Apply 18 to 28 volt ac to the unloader molded
plug leads and listen for a click as the solenoid pulls
in. Remove power and listen for another click as the
unloader returns to its original position.
3.
If clicks can’t be heard, shut off power to the unit
and remove the control circuit molded plug from
the compressor and measure the unloader coil
resistance (connections on the compressor).
The solenoid coil should have continuity and not
be grounded or have infinite resistance. If the
coil resistance is infinite, zero, or grounded, the
compressor must be replaced.
4. Next check the molded plug.
A. Voltage check: Apply control voltage to the
plug wires (18 to 28 volt ac). The measured dc
voltage at the female connectors in the plug
should be around 15 to 27 vdc.
B. Resistance check: Measure the resistance from
the end of one molded plug lead to either of the
two female connectors in the plug. One of the
connectors should read close to zero ohms while
the other should read infinity. Repeat with other
wire. The same female connector as before
should read zero while the other connector again
reads infinity. Reverse polarity on the ohmmeter
leads and repeat. The female connector that
read infinity previously should now read close to
zero ohms.
C. Replace plug if either of these test methods
doesn’t show the desired results.
Operation Test
If the voltage, capacitor, overload and motor winding test
fail to show the cause for failure:
WARNING
High Voltage!
Disconnect all power before servicing or
installing. Multiple power sources may be present.
Failure to do so may cause property damage,
personal injury or death.
1. Remove unit wiring from disconnect switch and wire
a test cord to the disconnect switch.
NOTE: The wire size of the test cord must equal the
line wire size and the fuse must be of the proper size
and type.
2. With the protective terminal cover in place, use the
three leads to the compressor terminals that were
disconnected at the nearest point to the compressor
and connect the common, start and run clips to the
respective leads.
3. Connect good capacitors of the right MFD and
voltage rating into the circuit as shown.
4. With power ON, close the switch.
WARNING
Line voltage now present.
A. If the compressor starts and continues to run,
the cause for failure is somewhere else in the
system.
B. If the compressor fails to start - replace.
Locked Rotor Test
If fuse, circuit breaker, ground fault protective device, etc.
has tripped, this is a strong indication that an electrical
problem exists and must be found and corrected. The
circuit protective device rating must be checked and its
maximum rating should coincide with that marked on the
equipment nameplate.
Before checking for locked rotor, the compressor terminals
should be checked for open windings (see Resistance Test)
and the run capacitor and start capacitor (if used) should
be checked thoroughly (see Checking Capacitor).