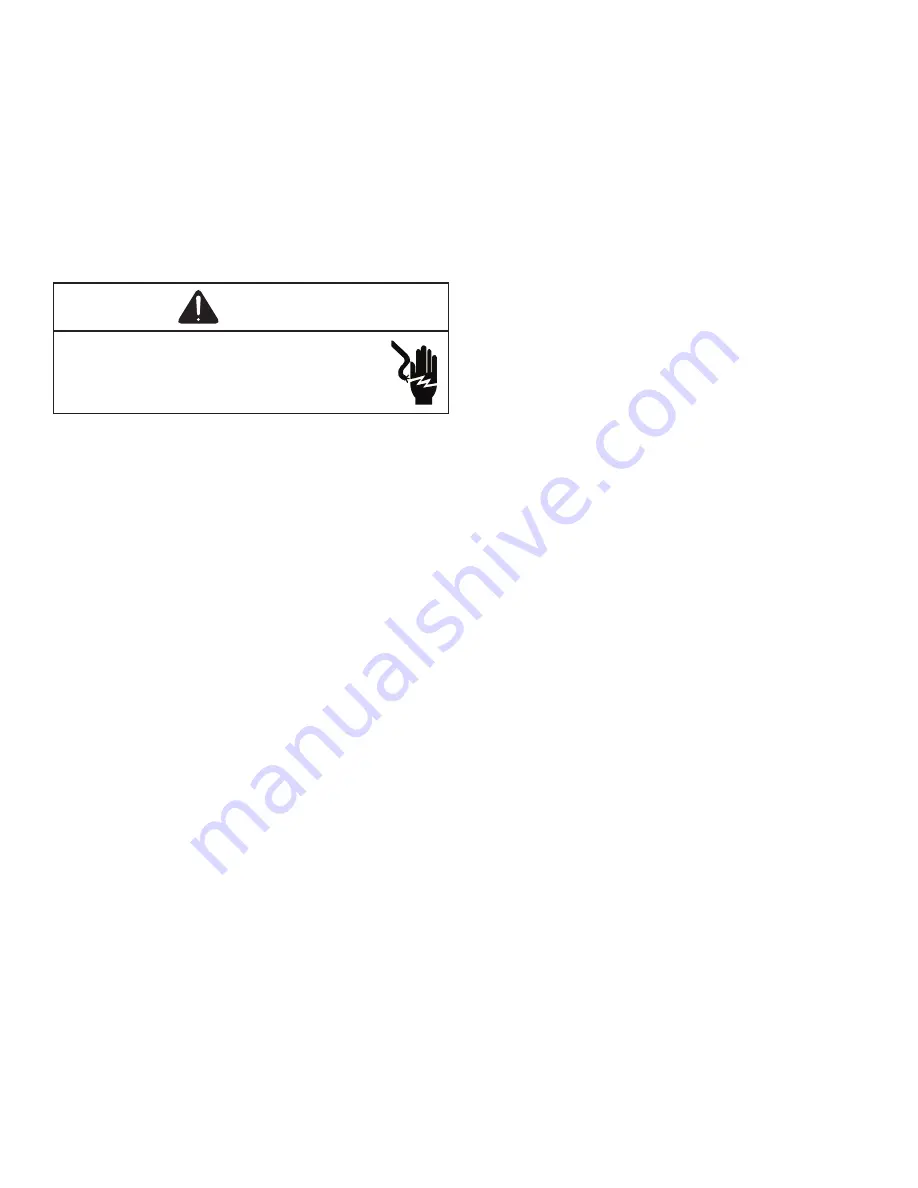
SCHEDULED MAINTENANCE
10
Package gas units require regularly scheduled
maintenance to preserve high performance standards,
prolong the service life of the equipment, and lessen the
chances of costly failure.
In many instances the owner may be able to perform some
of the maintenance; however, the advantage of a service
contract, which places all maintenance in the hands of a
trained serviceman, should be pointed out to the owner.
WARNING
High Voltage!
Disconnect all power before servicing or
installing. Multiple power sources may be present.
Failure to do so may cause property damage,
personal injury or death.
ONCE A MONTH
1.
Inspect the return filters of the evaporator unit and
clean or change if necessary.
NOTE:
Depending on
operation conditions, it may be necessary to clean
or replace the filters more often. If permanent type
filters are used, they should be washed with warm
water and dried.
2. When operating on the cooling cycle, inspect the
condensate line piping from the evaporator coil.
Make sure the piping is clear for proper condensate
flow.
ONCE A YEAR
Qualified Service Personnel Only
1. Clean the indoor and outdoor coils.
2. Clean the cabinet inside and out.
3. Motors are permanently lubricated and do not require
oiling. TO AVOID PREMATURE MOTOR FAILURE,
DO NOT OIL.
4. Manually rotate the outdoor fan and indoor blower to
be sure they run freely.
5. Inspect the control panel wiring, compressor
connections, and all other component wiring to be
sure all connections are tight. Inspect wire insulation
to be certain that it is good.
6. Check the contacts of the compressor contactor. If
they are burned or pitted, replace the contactor.
7. Using a halide or electronic leak detector, check all
piping and etc. for refrigerant leaks.
TEST EQUIPMENT
Proper test equipment for accurate diagnosis is as
essential as regular hand tools.
The following is a must for every service technician and
service shop:
1. Thermocouple type temperature meter - measure dry
bulb temperature.
2. Sling psychrometer - measure relative humidity and
wet bulb temperature.
3. Volt-Ohm Meter - testing continuity, capacitors, motor
windings and voltage.
4. Accurate Leak Detector - testing for refrigerant leaks.
5. High Vacuum Pump - evacuation.
6. Electric Vacuum Gauge, Manifold Gauges and
high vacuum hoses - to measure and obtain proper
vacuum.
7. Accurate Charging Cylinder or Electronic Scale -
measure proper refrigerant charge.
8. Inclined Manometer - measure static pressure and
pressure drop across coils.
Other recording type instruments can be essential in
solving abnormal problems, however, in many instances
they may be rented from local sources.
Proper equipment promotes faster, more efficient service,
and accurate repairs with less call backs.