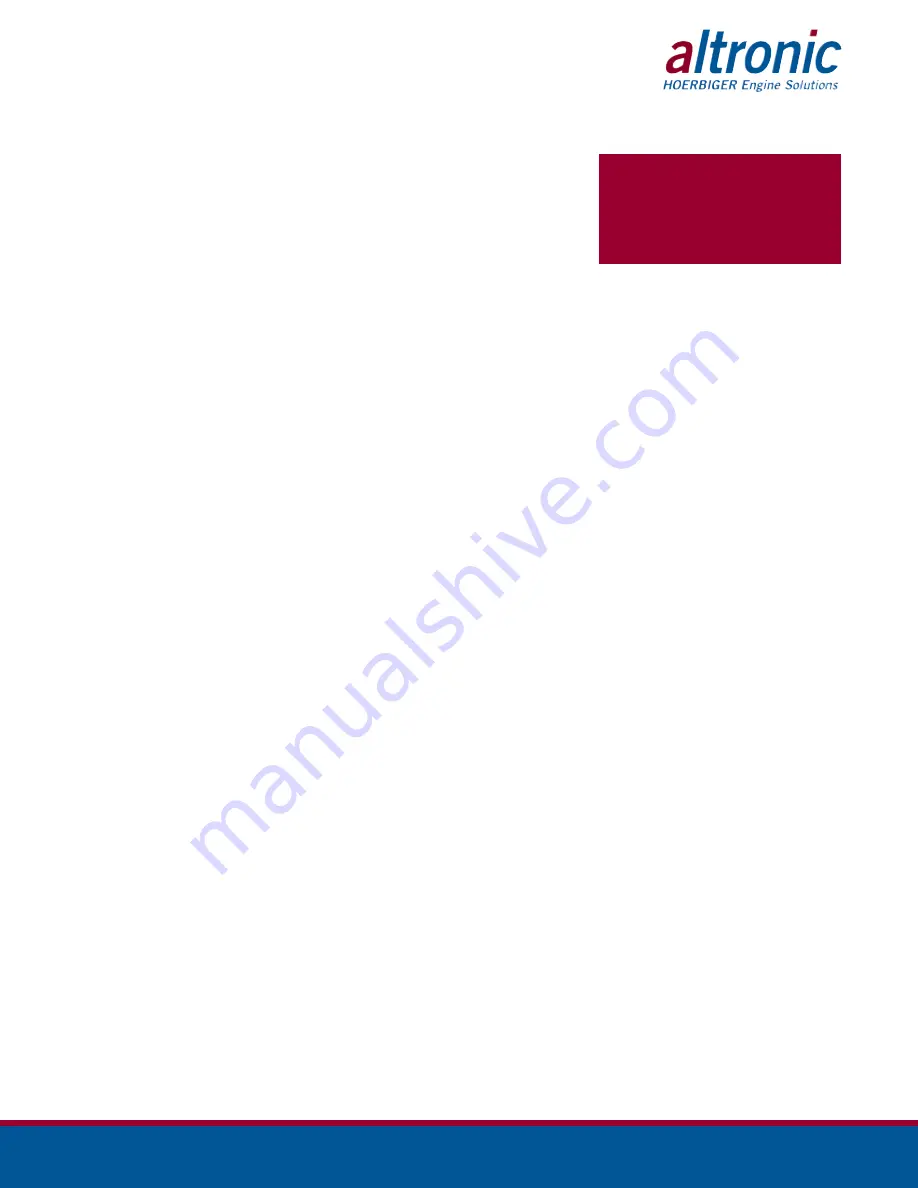
EPC-250 IOI 6-18 All rights reserved © ALTRONIC, LLC 2018
2
1.0 SYSTEM DESCRIPTION
1.1
The Altronic EPC-250 engine performance controller is a device designed to
maximize engine performance and efficiency. The controller is specifically
designed to control ignition timing and air/fuel ratio on spark-ignited, turbo-
charged, fuel-injected gas engines allowing for the total replacement of tradi-
tional pneumatic control systems. The EPC-250 is intended as a direct field
replacement for the existing legacy EPC-200 with little to no wiring retrofit.
The user-friendly interface allows easy configuration of the legacy EPC-200
functionality thru a touch screen display. Visual representation of control
parameters via trending can also be displayed on the touch screen to aid in
engine tuning.
1.2
In addition to Engine RPM, up to four other analog inputs can be used as control
variables. The additional four analog inputs can be scaled to represent desired
engineering units.
1.3
The EPC-250 operator interface is built around an 8.4" TFT 23K VGA
640 x 480 pixel LCD display high performance core with integrated function-
ality. The application’s configuration is stored in a non-volatile memory (32MB
flash). The EPC-250 incorporates a SD Memory card to increase memory
capacity, collect trending and data logging information, and store larger con-
figuration files.
1.4
EPC-250 TYPICAL CONTROL FUNCTIONS
A. IGNITION TIMING RETARD
Ignition Timing Retard vs. Engine Speed
Ignition Timing Retard vs. Fuel Manifold Pressure
Ignition Timing Retard vs. Air Manifold Pressure
Ignition Timing Retard vs. Air Manifold Temperature
Ignition Timing Retard vs. Pilot Manifold Pressure
Ignition Timing Retard vs. Exhaust Manifold Temperature
The operating values for the functions above are calculated separately accord-
ing to user entered curves, and the combined net effect is implemented by the
EPC-250 Controller in a PID format.
B. AIR/FUEL RATIO
Air Manifold Pressure vs. Fuel Manifold Pressure
Air Manifold Pressure vs. Engine Speed
Air Manifold Pressure vs. Exhaust Temperature
Air Manifold Pressure vs. Pilot Manifold Pressure
Air Manifold Pressure vs. Air Manifold Temperature
The operating values for the functions above are calculated separately accord-
ing to user entered curves, and the combined net effect is implemented by the
EPC-250 Controller.
C. AUXILIARY OUTPUT FUNCTIONS (typical)
Spare ................................................................................ (0utput 1)
Speed OP2 ........................................................................ (0utput 2)
Speed OP3 ........................................................................ (0utput 3)
Timer 1 ............................................................................. (0utput 4)
Timer 2 ............................................................................. (0utput 5)
Over Crank ........................................................................ (0utput 6)
Spare ................................................................................ (0utput 7)
Fault ................................................................................. (0utput 8)
WARNING: Deviation from these
instructions may lead to improper en-
gine/machine operation which could
cause personal injury to operators or
other nearby personnel.