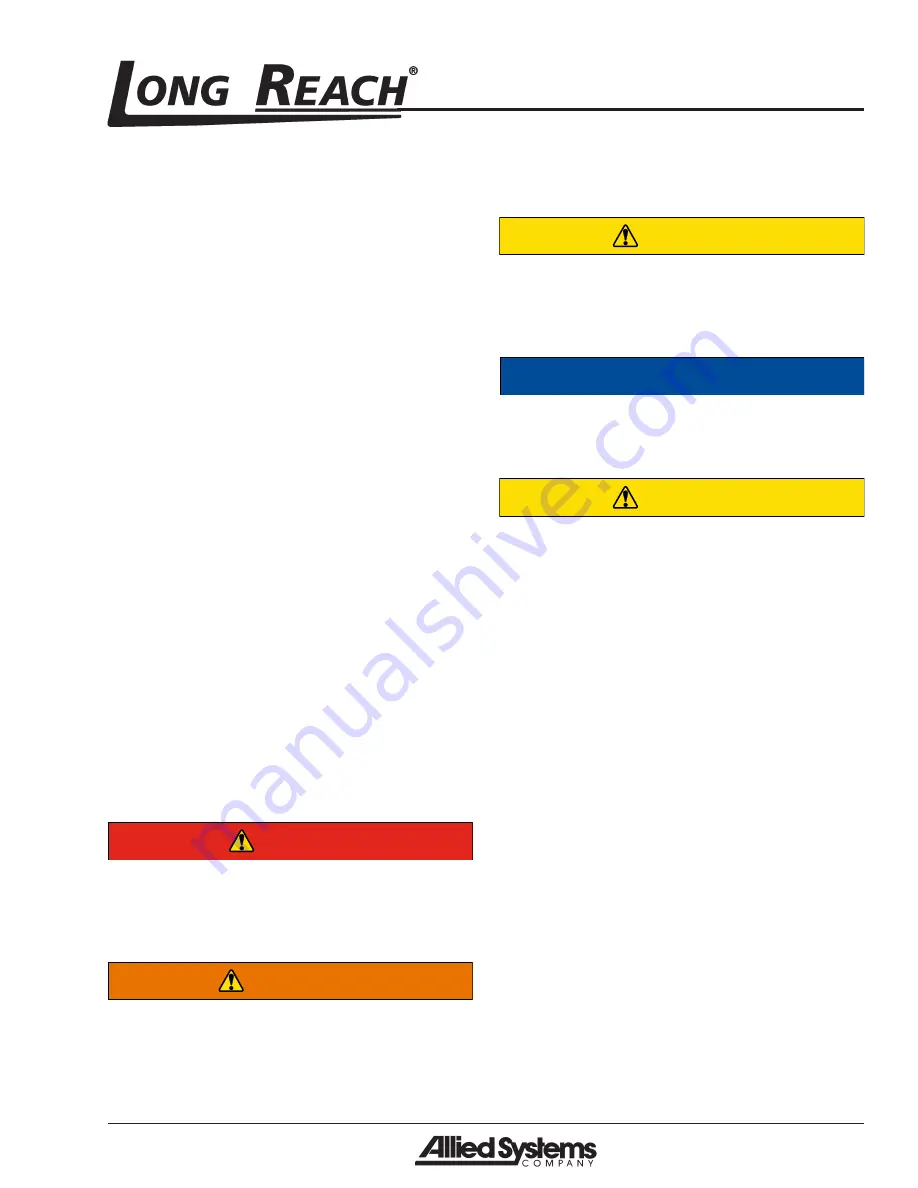
5
45-053, REV. 5/18
SECTION 3 SAFETY SUMMARY
Safety Information
Safety is Everyone’s Responsibility
Whether you are new on the job or a seasoned veteran,
these safety tips may prevent injury to you, to others, or
to the materials you are handling. Always be alert, watch
out for others, and follow these suggestions:
Attachments handle material, not people.
Safety starts with common sense, good
judgement, properly maintained equipment,
careful operation, and properly trained
operators.
The safety instructions and warnings, as documented
in this manual and shipped with the machine, provide
the most reliable procedures for the safe operation and
maintenance of your Long Reach attachment. It’s your
responsibility to see that they are carried out.
Safety Regulations
Know your company’s safety rules. Some companies
have site-specific directions and procedures. The meth-
ods outlined in your operator's manual provide a basis for
safe operation of the machine. Because of special condi-
tions, your company’s material handling procedures may
be somewhat different from those shown in this manual.
Safety Symbols
The following terms define the various precautions and
notices:
DANGER
Indicates a hazardous situation which,
if not avoided, WILL result in death or
serious injury. Carefully read the message
to prevent serious injury or death.
WARNING
Indicates a hazardous situation which,
if not avoided, could result in death or
serious injury. Carefully read the message
to prevent serious injury or death.
CAUTION
Indicates a hazardous situation which,
if not avoided, could result in minor or
moderate injury. Carefully read the message
to prevent minor or moderate injury.
Notice
Describes information that is not related to
personal injury, but may cause equipment
damage or void the warranty.
CAUTION
All possible safety hazards cannot be
foreseen so as to be included in this
manual. Therefore, the operator must
always be alert to possible hazards that
could endanger personnel or damage to
the equipment.
Obey the following warnings before using
your machine to avoid equipment damage,
personal injury or death.
Operation Warnings
•
You must be trained to operate this equipment prior
to operation. Be extremely careful if you do not nor-
mally operate this machine. Reorient yourself to the
machine before starting, then proceed slowly.
•
Always operate an attachment from the driver’s seat.
•
Always lower the attachment if you need to leave the
lift truck. A lift truck supporting a load requires your
full attention.