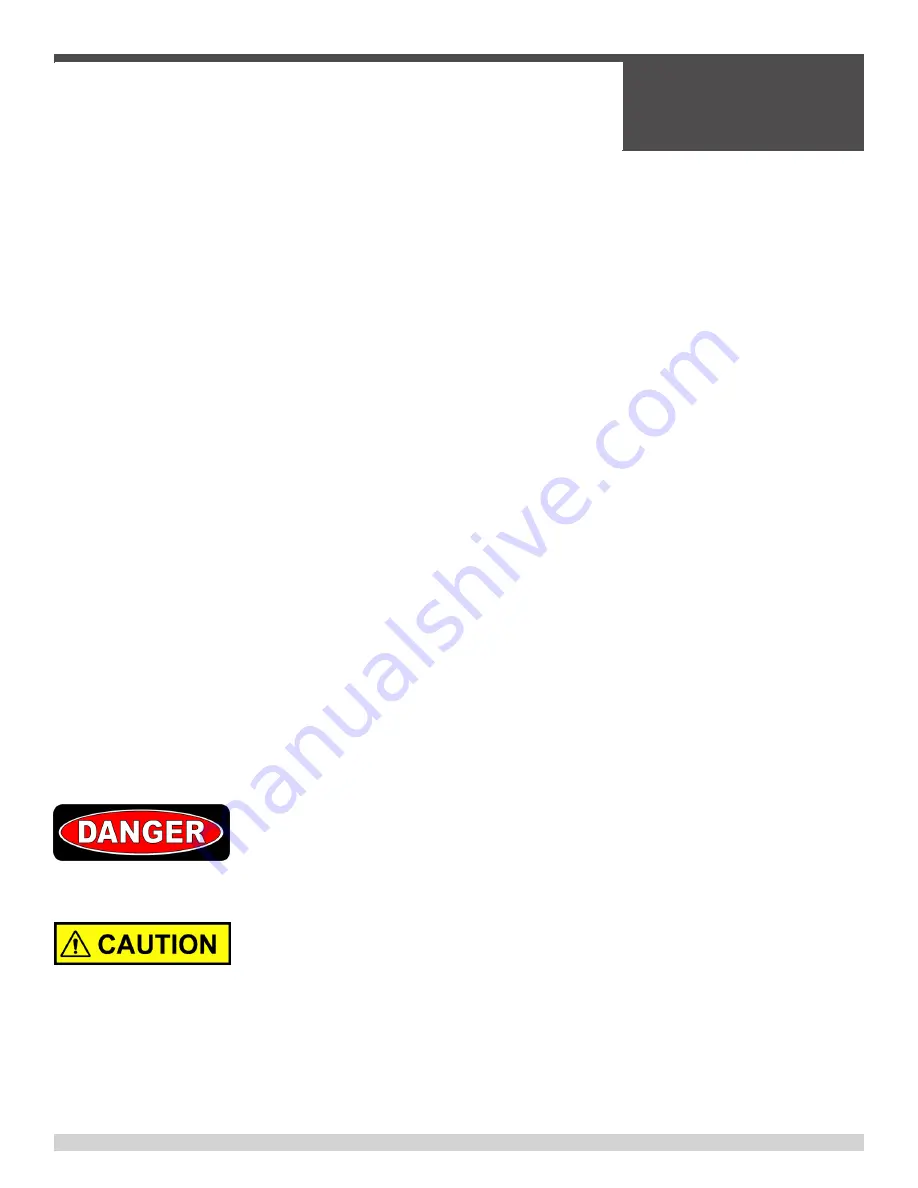
SECTION 1
SAFETY
050362
Page 27
ALWAYS
make sure the trailer is equipped with a safety chain.
ALWAYS
properly attach trailer’s safety chains to towing vehicle.
ALWAYS
make sure the vehicle and trailer directional, backup, brake and trailer lights are connected and working
properly.
DOT Requirements include the following:
• Connect and test electric brake operation.
• Secure portable power cables in cable tray with tie wraps.
The maximum speed for highway towing is 55 MPH unless posted otherwise. Recommended off-road towing is not
to exceed 15 MPH or less depending on type of terrain.
Avoid sudden stops and starts. This can cause skidding, or jack-knifing. Smooth, gradual starts and stops will im
-
prove towing.
Avoid sharp turns to prevent rolling.
Trailer should be adjusted to a level position at all times when towing.
Raise and lock trailer wheel stand in up position when towing.
Place chock blocks underneath wheel to prevent rolling while parked.
Place support blocks underneath the trailer’s bumper to prevent tipping while parked.
Use the trailer’s swivel jack to adjust the trailer height to a level position while parked.
CLEANING SAFETY
DO NOT
use gasoline, other fuels, or any flammable solvent to clean parts, especially in enclosed areas. Fumes from
fuels and solvents can casuse serious health problems if you are exposed to them over an extended period of time.
DO NOT
attempt to clean or service screed while machine is running.
General Safety, continued
Summary of Contents for SSE12
Page 1: ...OPERATIONS PARTS MANUAL SSE12 SCREED Manual Part 064633 I REVISION B ...
Page 17: ...SECTION 1 SAFETY 050362 Page 17 SECTION 1 SAFETY ...
Page 18: ...SECTION 1 SAFETY 050362 Page 18 State Regulations Proposition 65 Warning ...
Page 19: ...SECTION 1 SAFETY 050362 Page 19 Federal Regulation Respiratory Hazard ...
Page 30: ...SECTION 1 SAFETY 050362 Page 30 Notes ...
Page 31: ...SECTION 2 OPERATIONS 050362 Page 31 SECTION 2 OPERATIONS ...
Page 41: ...SECTION 3 SERVICE 050362 Page 41 SECTION 3 SERVICE ...
Page 43: ...SECTION 4 PARTS 050362 Page 43 SECTION 4 Parts ...
Page 70: ...SECTION 4 PARTS 050362 Page 70 4 13 End Mount Engine Assembly Illustration ...