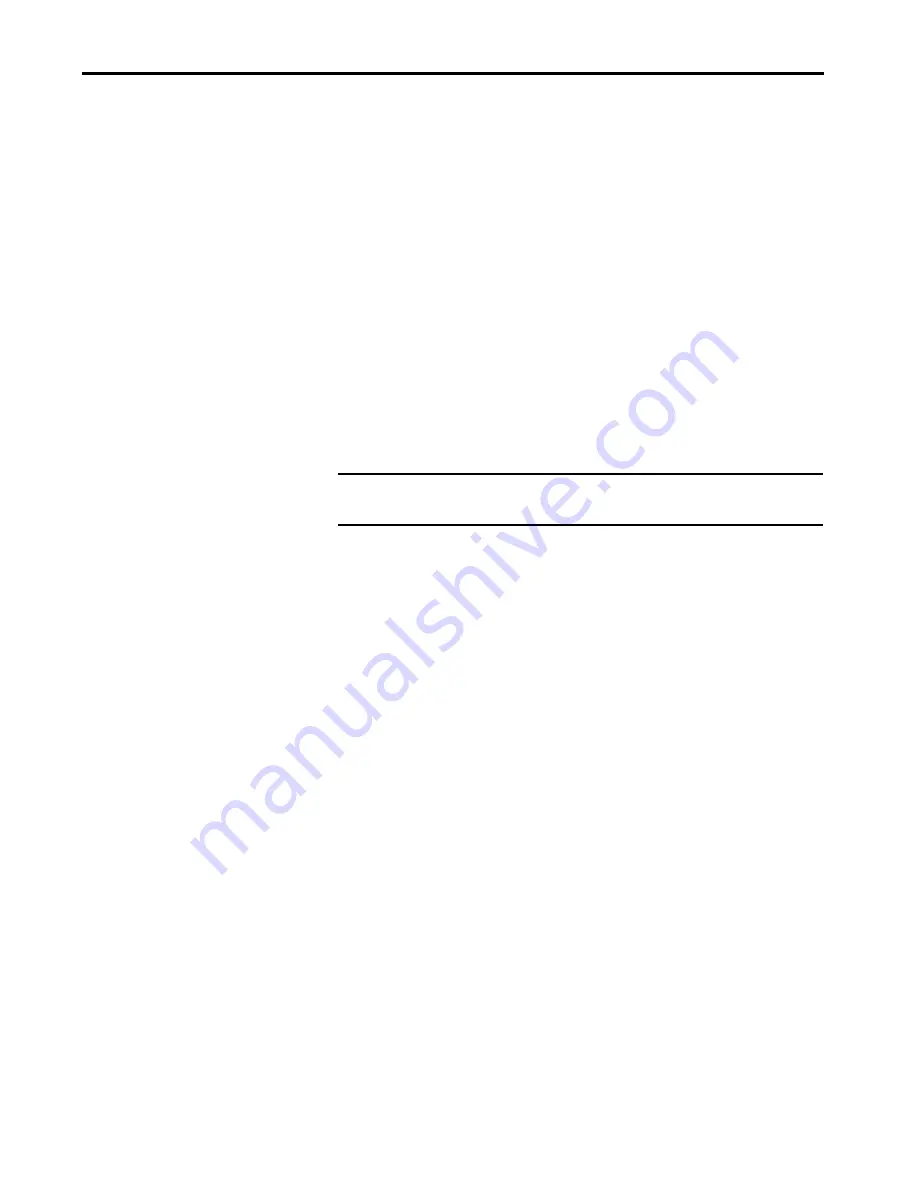
Rockwell Automation Publication 7000-UM203C-EN-P - September 2018
11
Safety Concept
Chapter 2
Performance Level and Safety Integrity Level (SIL) CL3
For safety-related control systems, Performance Level (PL), according to ISO
13849-1, and SIL levels, according to IEC 61508 and EN 62061, include a
rating of the system’s ability to perform its safety functions. All of the safety-
related components of the control system must be included in both a risk
assessment and the determination of the achieved levels.
Refer to the ISO 13849-1, IEC 61508, and EN 62061 standards for complete
information on requirements for PL and SIL determination.
Functional Proof Tests
The functional safety standards require that functional proof tests be
performed on the equipment used in the system. Proof tests are performed at
user-defined intervals and are dependent upon the Probability of Failure on
Demand (PFD) and Probability of a Dangerous Failure occurring per Hour
(PFH) values.
PFD and PFH Definitions
Safety-related systems can be classified as operating in either a Low Demand
mode, or in a High Demand/Continuous mode.
• Low Demand mode: where the frequency of demands for operation
made on a safety-related system is no greater than one per year or no
greater than twice the proof-test frequency.
• High Demand/Continuous mode: where the frequency of demands for
operation made on a safety-related system is greater than once per year or
greater than twice the proof test interval.
The SIL value for a low demand safety-related system is directly related to
order-of-magnitude ranges of its average probability of failure to satisfactorily
perform its safety function on demand or, simply, average PFD. The SIL value
for a High Demand/continuous mode safety-related system is directly related
to the PFH.
Safety Parameter Data
PFH calculations are based on the equations from Part 6 of IEC 61508.
MTTF
d
and DC
avg
values are based on EN ISO 13849-1.
This table provides data for a 12-year mission time only if the safety function is
demanded at least once every 6 months, and demonstrates the worst-case effect
of various drive configuration changes on the data.
IMPORTANT
Your specific application determines the time frame for the proof test
interval.
Summary of Contents for PowerFlex 7000 Series
Page 41: ......