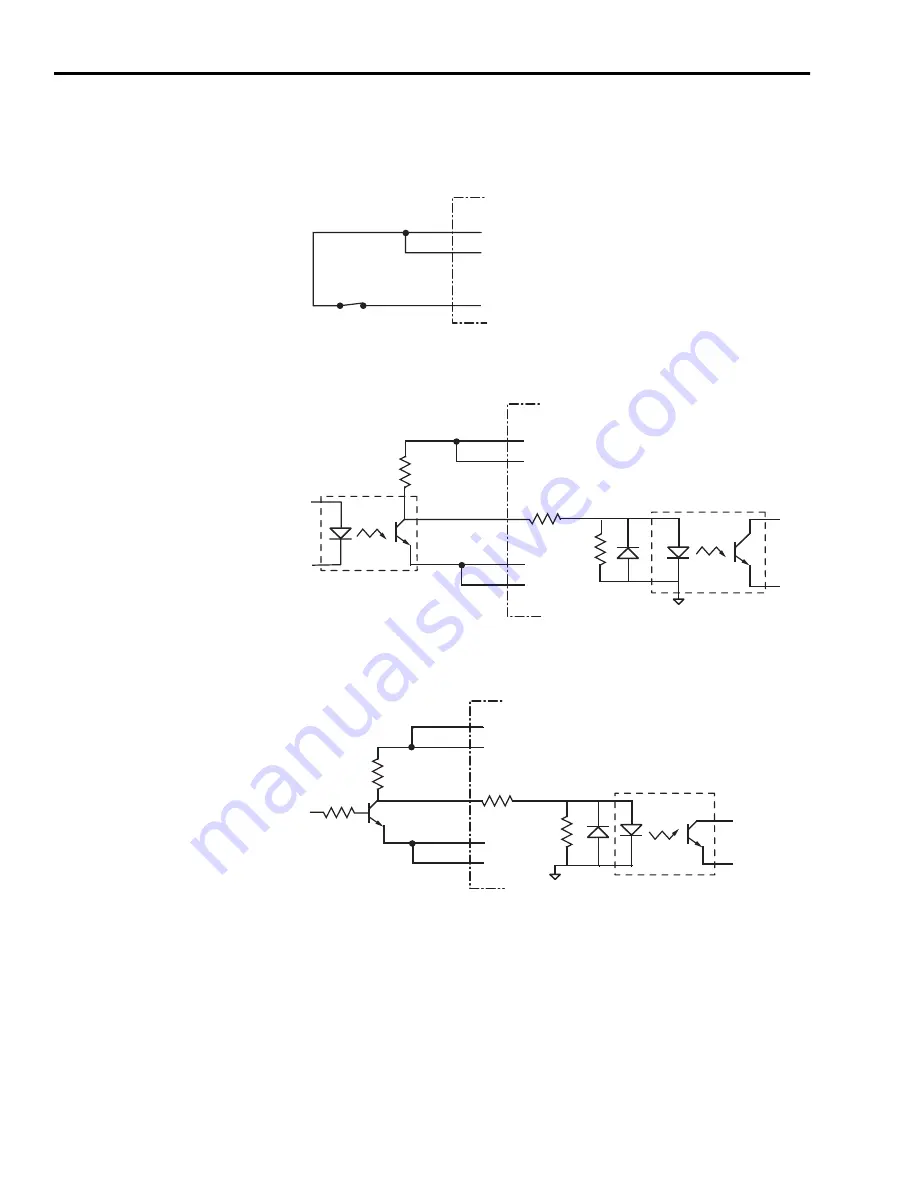
Publication 2098-IN003E-EN-P — April 2004
2-32
Ultra3000 Connector Data
Input Interface Examples for Active Low Inputs
Figure 2.21
Drive Input Connected to Normally Closed Switch
Figure 2.22
Drive Input Connected to Opto-Isolator
Figure 2.23
Drive Input Connected to NPN Transistor
CN1-29
CN1-30
CN1-31
through CN1-38
Ultra3000 Drive
IOPWR
IOPWR
2.7k
Ω
1k
Ω
CN1-29
CN1-30
CN1-27
CN1-28
CN1-31
through CN1-38
R
L
Ultra3000 Drive
IOCOM
IOCOM
IOCOM
IOPWR
IOPWR
2.7k
Ω
1k
Ω
CN1-29
CN1-30
R
L
CN1-27
CN1-28
CN1-31
through CN1-38
Ultra3000 Drive
IOCOM
IOCOM
IOCOM
IOPWR
IOPWR