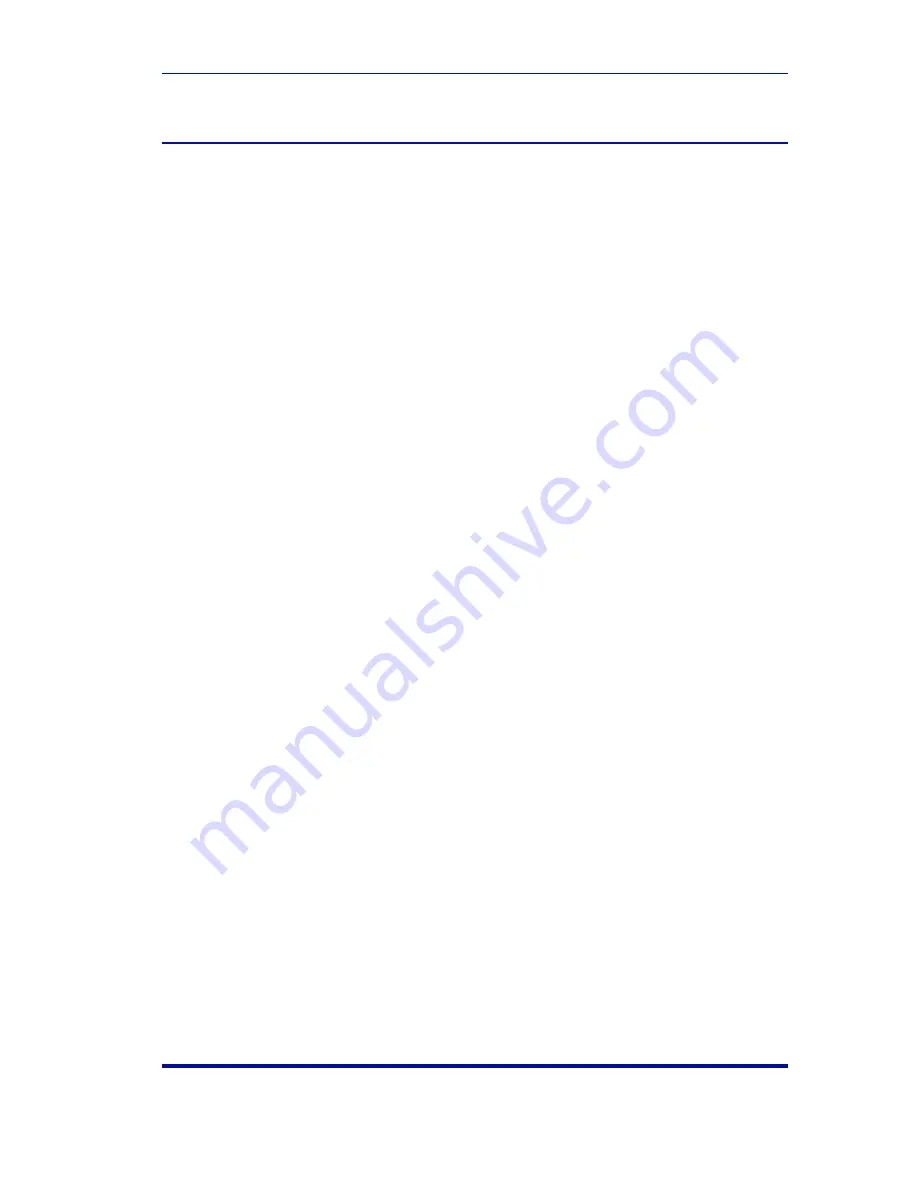
Owner’s Manual
35
Troubleshooting (cont’d)
Tool jams frequently.
z
Incorrect fasteners.
-
Verify that you are using approved fasteners of correct size.
z
Damaged fasteners.
-
Replace w/undamaged fasteners.
z
Magazine or nose screws loose.
-
Tighten screws.
z
Magazine is dirty.
-
Clean magazine.
z
Driver is worn or damaged
-
Install Driver Maintenance Kit.