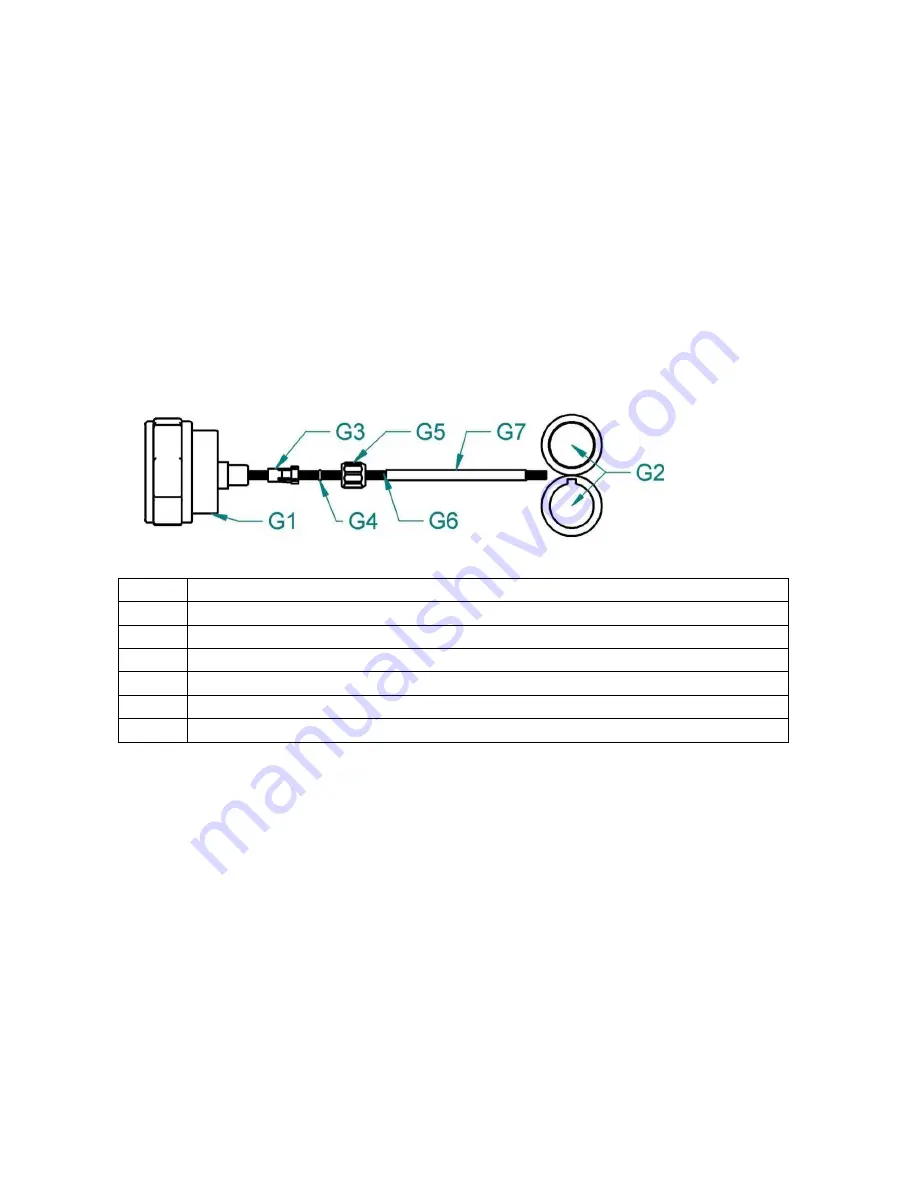
11/23
ALFA IN a.s. ©
www.alfain.eu
3. If there is a suitable groove on the roll, rotate the roll and place it back on
the shaft and secure it by screwing the element
E5
.
ADJUSTING THE MACHINE FOR WELDING OF ALUMINIUM
For feeding the AL wire it is necessary to use roll with the “U” profile - see
paragraph OVERVIEW ROLLS WIRE FEED. To prevent problems with feeding
use wires with diameter. 1.0 mm of AIMg3 or AlMg. Wire of alloy Al99, 5 or AlSi5
are too soft and easily will cause problems with movement.
For the aluminum welding it is also necessary to provide the torch tefl. liner and
special current nipple. We do not recommend you to use the torch longer than 3
m. Great attention must be paid to adjust the contact power of rolls – it must not
be too high, otherwise there is a deformation of the wire.
As a protective atmosphere is necessary to use argon.
Picture
4
– Customization of the feed for the aluminium wire
G1
EURO connector
G2
Rolls
G3
Liner terminal for 4,0mm, 4,7mm outer diameter
G4
O-ring 3,5 x1, 5mm to prevent escape of gas
G5
Nut
G6
Liner tefl.
G7
Sustain pipe for teflon and plastic liner
INSERTING THE WIRE
1. Open the side cover of the wire feeder space
2. Put the wire spool on the wire spool holder
D1
and fix it with the fixing nut
D2
. If a spool (size of 15 or 18 kg) is used, put on each side of the spool
adapter
D3
. The hole in the back of the adapter must fit into the pin on the
wire spool holder!
3. Cut off the curved or damaged end of welding wire and lead it through the
inlet liner
E3,
and the roll into the liner inside the EURO torch connector
(about 5 cm). Make sure, that you use the suitable groove.
4. Put the pressure arm
E2
down in that way, that the teeth or the gear fit and
fix it by setting the lever
E1
into vertical position.
5. Adjust the pressure nut that way that it provides constant movement of
wire but it does not deform wire. The adjusting screw is located under the
plastic screw
E1
.