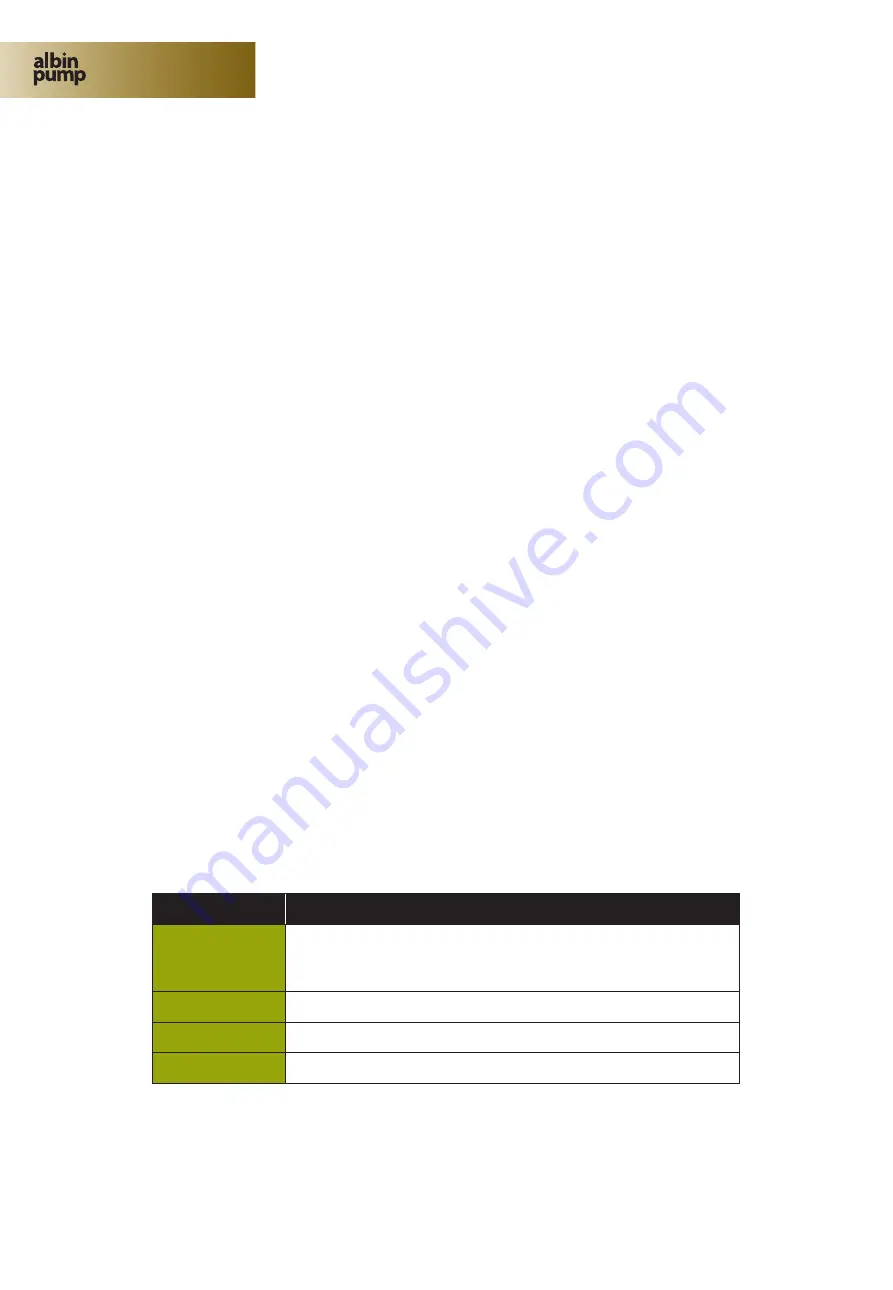
22
AD
since 1928
AD
since 1928
4.5 - HOW TO START, OPERATE AND STOP THE PUMP
Open the fluid discharge and suction valves. Gradually increase the air pressure with the pres-
sure regulator until the pump starts to cycle and the suction and discharge lines are filled.
Now, by adjusting the regulator, the stroking speed can be controlled, until the required
flow is obtained. Adjusting of the shut-off valve in the discharge line will also effect the flow.
There are many ways to stop the pump :
1 - Close the fluid discharge shut-off valve. The pressure built up in the discharge line will not exceed
the air inlet pressure. Pump will cycle slowly but no additional liquid is entering the pump. Pump will
restart as soon as the valve is opened again.
2 - Close the air supply shut-off valve.
3 - Reduce the air pressure with the pressure regulator so air supply pressure is less than the fluid
discharge pressure.
4.6 - ROUTINE MAINTENANCE
Ensure that the suction pipes/hoses are free from debris. It is advised to run the pump with a com-
patible fluid (e.g. water) prior to production start-up to ensure the system is correctly installed and
there is no leakage.
*
Use fixed shaft at flooded installations
Regular inspections are the best means for preventing unscheduled pump down time.
Each pump application has a unique service requirement. To predict and prevent future maintenance
problems it is advised to check the pump after a few weeks running time. After this inspection it is
possible to make up a preventative maintenance schedule.
Size
Action
Diaphragms
Replace if cracks occur in the carrier rubber and/or PTFE layer. In-
spection is recommended at every 15 million cycles - repeatably.
Dependant of application
Muffler
Replace if clogged with impurities.
Shaft bushing
Replace if worn.
Screws/nuts
Check they are correctly tightened – see section 4.1.
AD Instruction Manual-2011EE-GB.indd 22
25/07/11 09:46