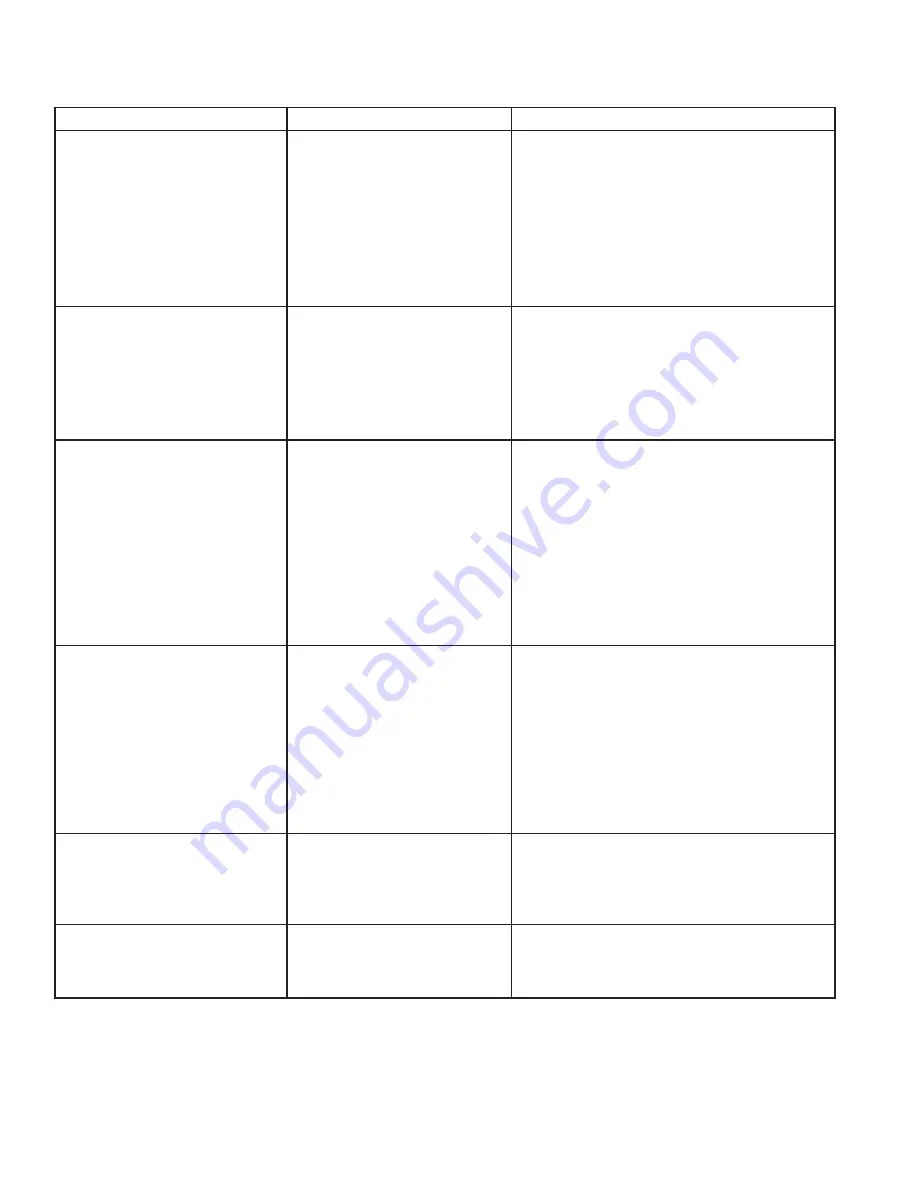
42
ICE CEA/CGA1012–1060 Wall Mount AC I&O Manual
03/2021 Rev.1
5.2 Failure Symptoms Guide
PROBLEM/SYMPTOM
LIKELY CAUSE(S)
CORRECTION
A. Unit does not run.
1. Power supply problem.
1. Check power supply for adequate phase and voltage.
Check wiring to unit and external breakers or fuses.
NOTE: An internal anti-short-cycle
timer will prevent the unit
from starting for .2 to 8
minutes following start-up.
2. Tripped internal disconnect.
2. Check internal circuit protection devices for continuity.
3. Shut off by external thermostat or
thermostat is defective.
3. Check operation of wall-mounted thermostat.
4. Unit off on high or low pressure limit. 4. Reset pressure switch.
5. Internal component or connection
failure.
5. Check for loose wiring. Check components for failure.
B. Unit runs for long periods or continu-
ously; cooling is insufficient.
1. Dirty filter or reduced airflow
1. Check air filter(s). Check blower operation. Remove
airflow restriction.
2. Low refrigerant.
2. Check for proper charge and possible refrigerant leak.
3. Component failure.
3. Check internal components, especially compressor for
proper operation.
4. Unit undersized for job.
4. Add additional units for greater capacity.
C. Unit cycles on high/low pressure
limit.
1. Loss or restriction of airflow.
1. Check blower assembly for proper operation. Look
for airflow restrictions, e.g.. the air filter. Check blower
motor and condenser fan.
2. Restriction in refrigerant circuit.
2. Check for blockage or restriction, especially filter drier
and capillary tube assembly.
3. Refrigerant overcharge (following
field service)
3. Evacuate and recharge to factory specifications.
4. Defective pressure control.
4. Check limit cutout pressures. Control is set to actuate at
approximately 60 PSIG (low pressure) and 650 PSIG (high
pressure)
D. Unit blows fuses or trips circuit
breaker.
1. Inadequate circuit ampacity.
1. Note electrical requirements in Chapter 2 and correct
as necessary.
2. Short, loose, or improper connection
in field wiring.
2. Check field wiring for errors.
3. Internal short circuit. Loose or
improper connection(s) in unit.
3. Check wiring in unit. See wiring and schematic dia-
grams. Test components (especially the compressor)
for shorts.
4. Excessively high or low supply volt-
age or phase loss (3ø only)
4. Note voltage range limitations specific to the compres-
sor troubleshooting section.
E. Water on floor near unit.
1. Obstruction in condensate line.
1. Check for clog or restriction.
2. Obstruction or leak in condensate
pan.
2. Check pan for leak or blockage.
3. Unit is not level.
3. Level unit.
F. No space heating or reduced heating
(units equipped with resistance ele-
ments)
1. Defective heating element(s).
1. Check resistance element(s) for continuity.
2. Thermal limit open.
2. Check continuity across thermal limit switch.
3. Defective heater contactor.
3. Check relay for proper operation. Replace if defective.
5.3 Compressor
Troubleshooting
NOTE: It is important to rule out other component failures before condemning the compressor.
The following electrical tests will aid diagnosis: