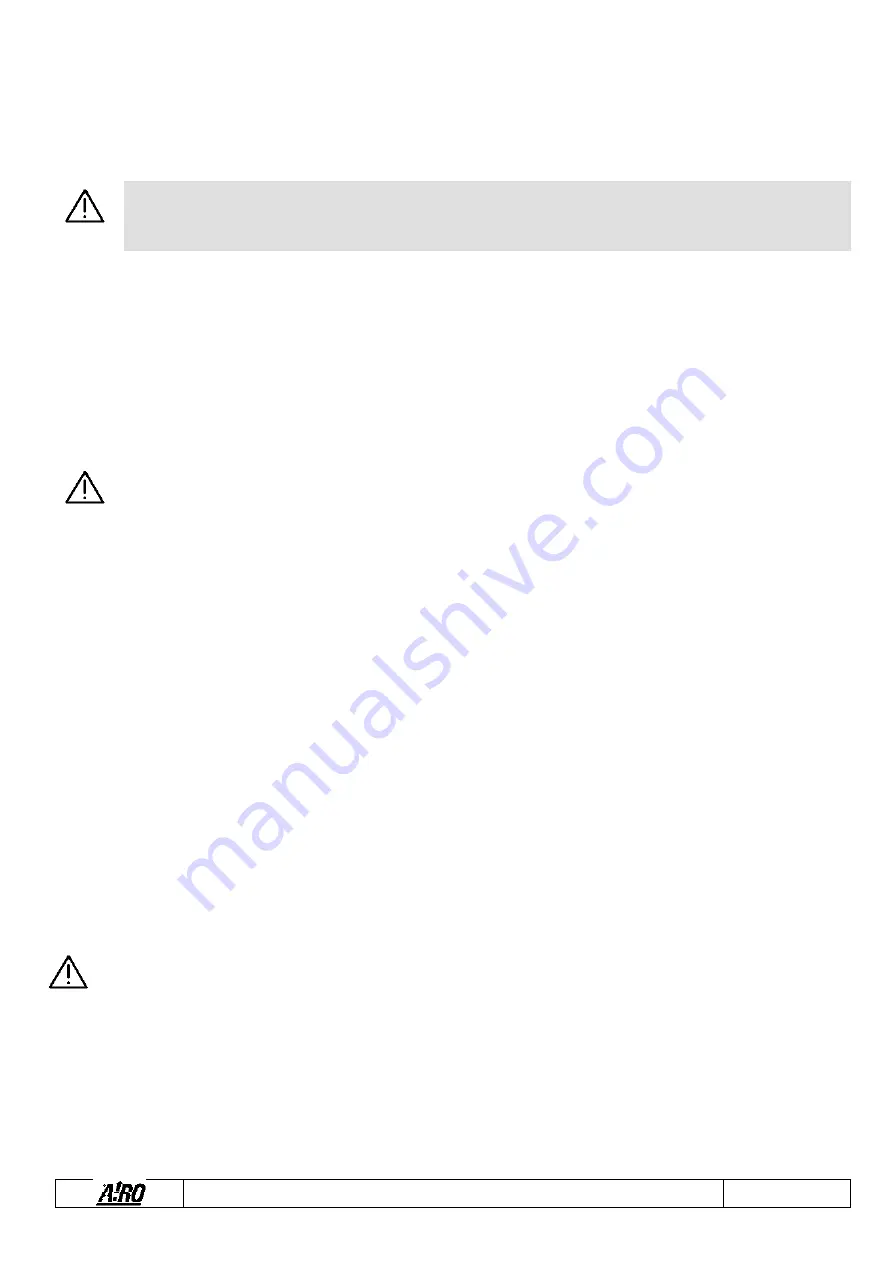
Use and Maintenance Manual - X_RT Series
Page 22
3.3
Use instructions
3.3.1
General
The electric and hydraulic circuits are provided with safety devices, calibrated and sealed by the manufacturer:
DO NOT TAMPER WITH AND MODIFY THE CALIBRATION OF ANY COMPONENT OF THE ELECTRIC AND
HYDRAULIC SYSTEMS.
The machine must be used only in areas well lit up, checking that the ground is flat and firm. The machine may not
be used if the lighting conditions are not sufficient. The machine is not equipped with any lightening system.
Before using the machine check its integrity and conservation state.
During maintenance operations do not dispose of any waste materials in the environment, but comply with current
regulations.
Do not carry out any service or maintenance operations when the machine is connected to the mains supply. Follow
the instructions given in the following paragraphs.
Do not approach the electric and hydraulic system components with sources of heat or flames.
Do not increase the max. allowed height by means of scaffolds, ladders or other.
With the machine lifted, do not fasten the platform to any structure (beams, pillars or wall).
Do not use the machine as a crane, hoist or lift.
Protect the machine (in particular the platform control panel by means of the specially provided cover- optional) and
the operator when working in adverse environmental conditions (painting, de-painting, sand-blasting, washing, etc.).
Using the machine in bad weather conditions is forbidden; in particular, wind speeds must not exceed the limits
indicated in the technical specifications (to measure speeds, see following chapters).
Machines with a wind speed limit of 0 m/s are to be used indoors only.
In the event of rain or in parking condition always protect the platform control panel by means of the specially
provided cap (optional).
Do not use the machine in areas where risks of fire or explosion exist.
Do not use pressurized water jets (high-pressure cleaners) to wash the machine.
Overloading the work platform is forbidden.
Avoid knocks and/or contacts with other vehicles and fixed structures.
Leaving or accessing the work platform is forbidden unless this is in the position required for access or leaving (see
the “Accessing the platform” chapter).
3.3.2
Handling
Before handling the machine check that the connection plugs are disconnected from the power supply source.
In order to avoid any instability, use the machine on regular and firm grounds. To prevent the machine from
overturning, comply with the max. gradeability values indicated in the Technical data section under paragraph "Stability
limits". However, movements on inclined grounds are to be carried out with the utmost caution.
As soon as the platform is lifted (the tolerance varies from model to model) the safety drive speed is automatically
activated (all models of this handbook have passed the stability Tests in compliance with standard EN280).
Drive the machine with lifted platform only on flat grounds, verifying the absence of holes or steps on the floor and
bearing in mind the overall dimensions of the machine.
Backward drive (in the direction of the fixed wheels) does not allow the operator a complete visibility from the control
position. This operation shall be carried out with the utmost care.
While driving the machine with lifted platform the operators are not allowed to place horizontal loads onto the platform
(operators on board must not pull ropes, wires, etc.).
The machine must not be used directly for road transport. Do not use it for material transport (see chapter “Intended
use”).
Do not operate the machine if components boxes are not properly closed.
Summary of Contents for X RT Series
Page 83: ...Use and Maintenance Manual X_RT Series Page 83...
Page 104: ...Use and Maintenance Manual X_RT Series Page 104...
Page 105: ...Use and Maintenance Manual X_RT Series Page 105...
Page 106: ...Use and Maintenance Manual X_RT Series Page 106...
Page 107: ...Use and Maintenance Manual X_RT Series Page 107...
Page 108: ...Use and Maintenance Manual X_RT Series Page 108...
Page 109: ...Use and Maintenance Manual X_RT Series Page 109...
Page 110: ...Use and Maintenance Manual X_RT Series Page 110 12 2 ELECTRIC DIAGRAM X12 RTE X14 RTE...
Page 111: ...Use and Maintenance Manual X_RT Series Page 111...
Page 112: ...Use and Maintenance Manual X_RT Series Page 112...
Page 113: ...Use and Maintenance Manual X_RT Series Page 113...
Page 114: ...Use and Maintenance Manual X_RT Series Page 114...
Page 115: ...Use and Maintenance Manual X_RT Series Page 115...
Page 116: ...Use and Maintenance Manual X_RT Series Page 116...
Page 118: ...Use and Maintenance Manual X_RT Series Page 118...