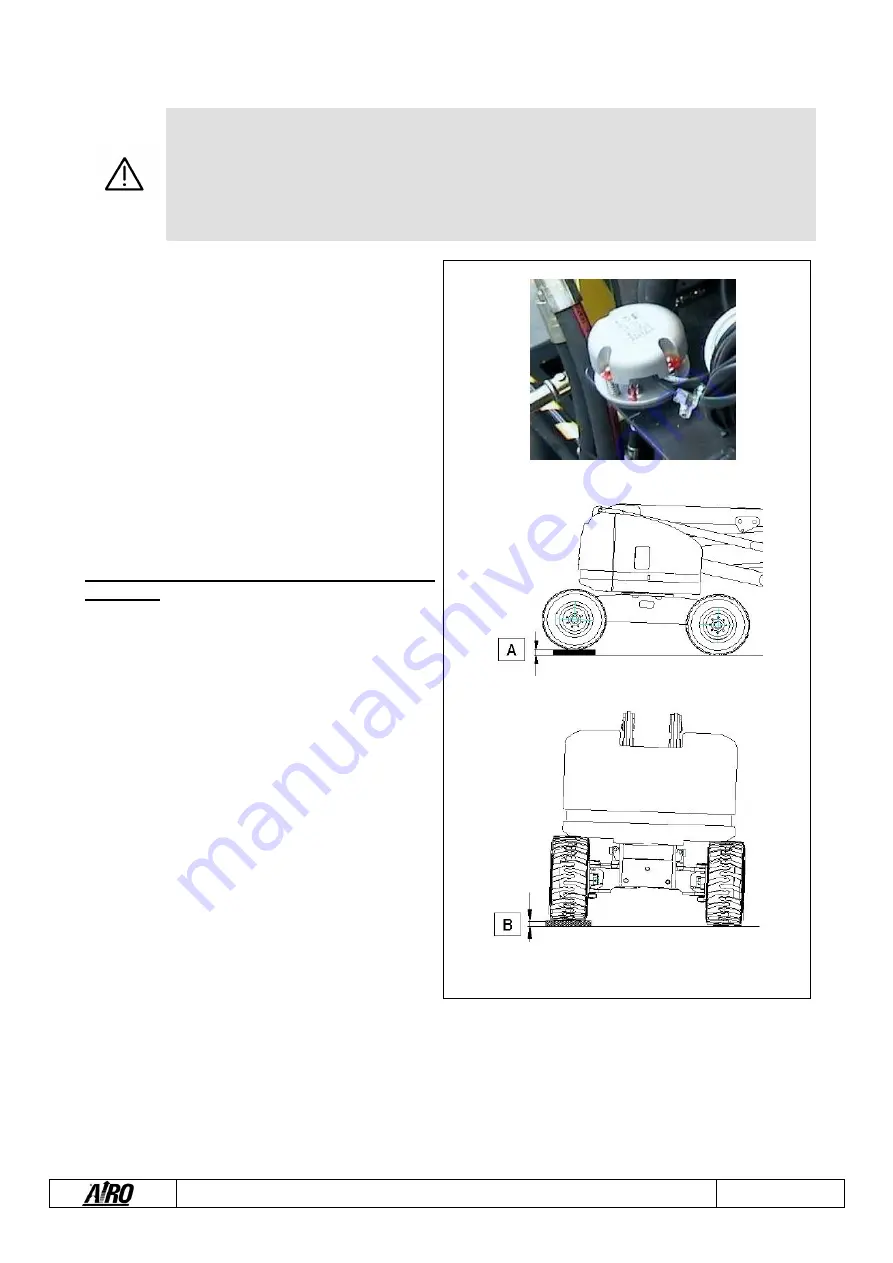
User’s Manual – A16 J A18 J Series
Page 75
7.2.11.
Checking the efficiency of the inclinometer
CAUTION!
Usually the inclinometer does not need to be adjusted unless the electronic control unit has been
replaced. The equipment needed for the replacement and adjustment of this component requires
skilled personnel.
THIS OPERATION IS A CRUCIAL MAINTENANCE TASK AND SHOULD BE STRICTLY CARRIED
OUT BY SPECIALIZED TECHNICIANS.
The inclinometer does not require any adjustment since it
is calibrated in the factory before the machine is delivered.
The inclinometer controls the chassis inclination and if the
latter exceeds the maximum admissible slope:
Stops platform ascent.
Disables travel with the platform raised above a given
height (depending on the model).
Sets off an acoustic alarm and a pilot light (on the
platform) to warn the operator that the machine is not
standing safe (see “General Use and Operation”).
The inclinometer monitors the inclination of the chassis
against two axes (X; Y). On machine models that have the
same lateral and longitudinal inclination limits, the control
is carried out against one axis only (X-axis).
Perform a functional control of the inclinometer at least
once a year.
To check the inclinometer operation against the
longitudinal axis
(generally the
X-axis
):
Use the control panel on the platform to place a n
(A+10 mm) thick shim under the front and rear wheels
(see table below).
Wait three seconds (lag time set at factory) till the red
pilot light and the acoustic alarm on the platform go
off. With the platform DOWN (booms down, telescopic
boom in and jib between +10° and –70°) all
manoeuvres are still possible. By lifting one of the
booms (excepting the Jib) and/or extending the
telescopic boom, the control system of the machine
disables all lifting and drive controls.
If no alarm is triggered ASK FOR TECHNICAL
SERVICE.
To check the inclinometer against the
lateral axis
(normally
Y-axis
):
Fig.29
Use the control panel on the platform to place a (B+10 mm) thick shim under the two out-wheels on right or on the
left wheels (see table below).
Wait three seconds (lag time set at factory) till the red pilot light and the acoustic alarm on the platform go off. With
the platform DOWN (booms down, telescopic boom in and jib between +10° and –70°) all manoeuvres are still
possible. By lifting one of the booms (excepting the Jib) and/or extending the telescopic boom, the control system of
the machine disables all lifting and drive controls.
If no alarm is triggered ASK FOR TECHNICAL SERVICE.
Summary of Contents for A16 J Series
Page 14: ...User s Manual A16 J A18 J Series Page 14...
Page 17: ...User s Manual A16 J A18 J Series Page 17...
Page 20: ...User s Manual A16 J A18 J Series Page 20...
Page 23: ...User s Manual A16 J A18 J Series Page 23...
Page 26: ...User s Manual A16 J A18 J Series Page 26...
Page 29: ...User s Manual A16 J A18 J Series Page 29...
Page 87: ...User s Manual A16 J A18 J Series Page 87...
Page 106: ...User s Manual A16 J A18 J Series Page 106 029 08 144...
Page 107: ...User s Manual A16 J A18 J Series Page 107 029 08 149...
Page 108: ...User s Manual A16 J A18 J Series Page 108 029 08 161...
Page 109: ...User s Manual A16 J A18 J Series Page 109 029 08 171...
Page 110: ...User s Manual A16 J A18 J Series Page 110 029 08 128...
Page 111: ...User s Manual A16 J A18 J Series Page 111 029 08 129...
Page 112: ...User s Manual A16 J A18 J Series Page 112 029 08 150...
Page 113: ...User s Manual A16 J A18 J Series Page 113 029 08 132...
Page 114: ...User s Manual A16 J A18 J Series Page 114 029 08 158...
Page 115: ...User s Manual A16 J A18 J Series Page 115 029 08 148...
Page 116: ...User s Manual A16 J A18 J Series Page 116 029 08 147...
Page 117: ...User s Manual A16 J A18 J Series Page 117...
Page 119: ...User s Manual A16 J A18 J Series Page 119...