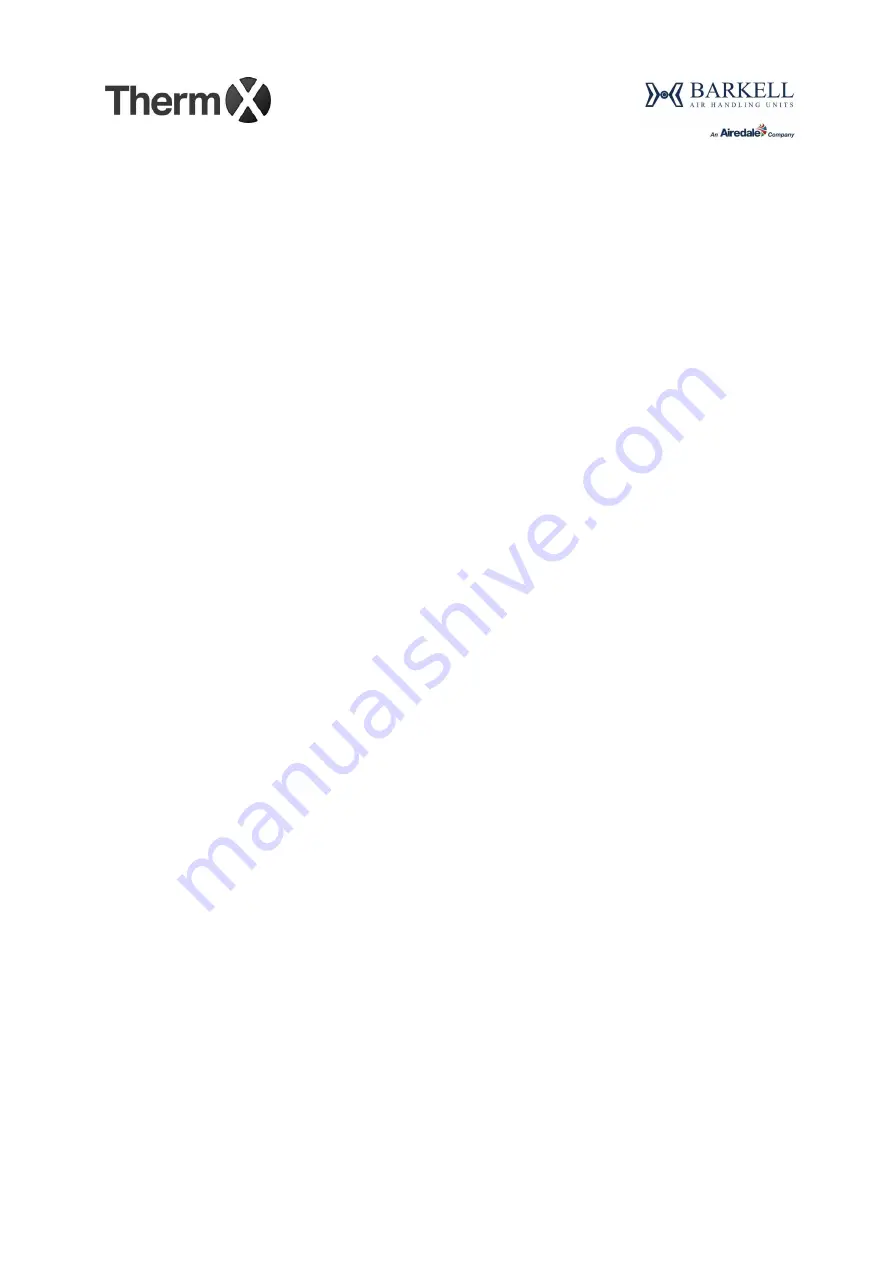
Therm-X MVHRU HR95
Technical Manual
Page 54 of 59
Version 2.4, 25/09/2020
6.
Counter flow plate heat exchanger
6.1.
The unit shall be equipped with highly efficient counter flow air to air plate heat exchanger, exceeding the 2018
requirements of regulation 1253/2014 of the Eco-design directive for ventilation units.
6.2.
The heat exchanger finned area and casing shall be manufactured from high thermal transmittance and
corrosion resistant aluminium.
6.3.
The exchanger shall be Eurovent certified and fully tested to EN308:1997 with low internal leakage (<0,5% @
250 Pa).
6.4.
The heat exchanger shall be provided with fully modulating face and by-pass dampers.
6.5.
The heat recovery section shall also be equipped with fully removable, epoxy coated, galvanized condensate
tray fitted with a 40mm OD drain connection for condensate collection and disposal.
6.6.
The condensate tray shall be equipped with a liquid level sensing mechanism to indicate the level of water on
the condensate tray.
6.7.
To ensure safe and reliable disposal of condensate an integral drain trap installed in a thermally insulated
compartment within the base frame of the unit shall be provided.
7.
Optional features
7.1.
The unit shall be optionally available with integral electrical pre-heating coil or post-heating coil.
7.1.1.
The electric heaters shall be manufactured with open coil heating elements and galvanized casing.
7.1.2.
The heater shall be complete with fully modulating SCR control (0-10V) to regulate the heat output from 0 to
100% and 2 stages of overheat protection (automatic and manual reset), integral
on the unit’s control logic.
7.2.
The units shall be optionally available with integral LPHW post-heating coil.
7.2.1.
LPHW coils shall be manufactured with aluminium fins, copper tubes and assembled on a corrosion resistant
galvanized casing.
7.2.2.
The maximum operating pressure of the LPHW coils shall be 16bar and the maximum operating temperature
130°C.
7.2.3.
The heating output shall be automatically modulated by use of the in-built temperature sensors and the
integral unit controls.
7.3.
The unit shall be optionally available with integral water changeover coil (WCO) or reverse cycle direct
expansion (DX) coils to allow cooling and/or heating operation. A plastic droplet eliminator shall be installed in the
coil and the coil section with fully removable, epoxy coated, galvanized condensate tray fitted with a 22mm OD
drain connection for condensate collection and disposal.