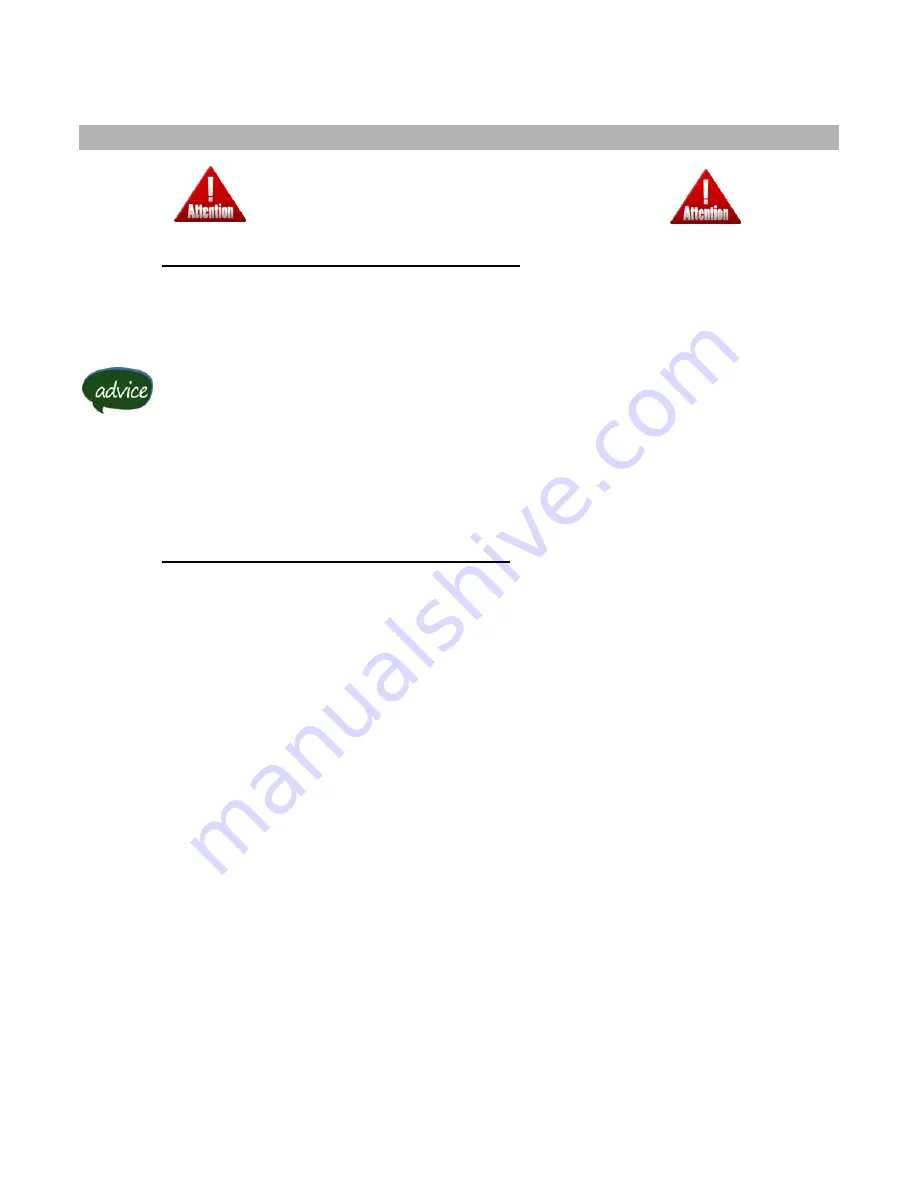
AIR DRYER SUPPLIER, INC.
AIR DRYER INSTRUCTION MANUAL
Model CATR
Reference ADS-316
Rev 0
Page 8 of 40
03/22/2019
SECTION 2: START UP & OPERATION
Prior to installation and start-up of this dryer,
please read and implement this section.
2.1
Dryer Location & Mounting Specifications
2.1.1
The standard electrical components are designed specifically for NEMA 4.
2.1.2
Remove all protective shipping crates, flange covers, etc.
Should vibrations occur on the installation location, the dryer is to be placed
onto vibration dampeners.
2.1.3
Because of vibration during shipping and installation, some lines, fittings, bolts, and
connections may have loosened; therefore, inspect all and, if required, tighten.
2.1.4
Locate and install any items that may have shipped loose from the dryer, such as
exhaust mufflers, auxiliary filters, etc.
2.2
Preventive Maintenance Prior to Start-up
2.2.1
All air dryers are tested at the factory for leak-tight joints and tightness of bolts;
however, during shipment, some bolts may vibrate loose. We have no control over
the handling our compressed air systems receive after leaving our factory. To
prevent costly problems at start-up and operation, all bolts should be checked for
tightness prior to system pressurization. This will assure gasket life, as well as
prevent possible gasket blowout. Gasket joints should be bubble tested after four or
five complete cycles of the dryer, to ensure gaskets are sealed. Any loose joints will
need to be re-tightened and re-tested for leaks.
If the dryer includes manual butterfly valves, valves must be totally closed before re-
torquing bolts.
Following is a comprehensive procedure for tightening all pressurized gasketed
joints:
2.2.2
TIGHTEN BOLTS IN SEQUENTIAL ORDER (i.e. 0
- 180
, 90
- 270
,
45
- 225
, and 135
- 315
) until final torque is reached.
2.2.3
Use ROTATIONAL TIGHTENING until all bolts are stable at final torque level (two
complete rotations are usually required).
Reference the next page for continuation of the flange bolt torque procedure.