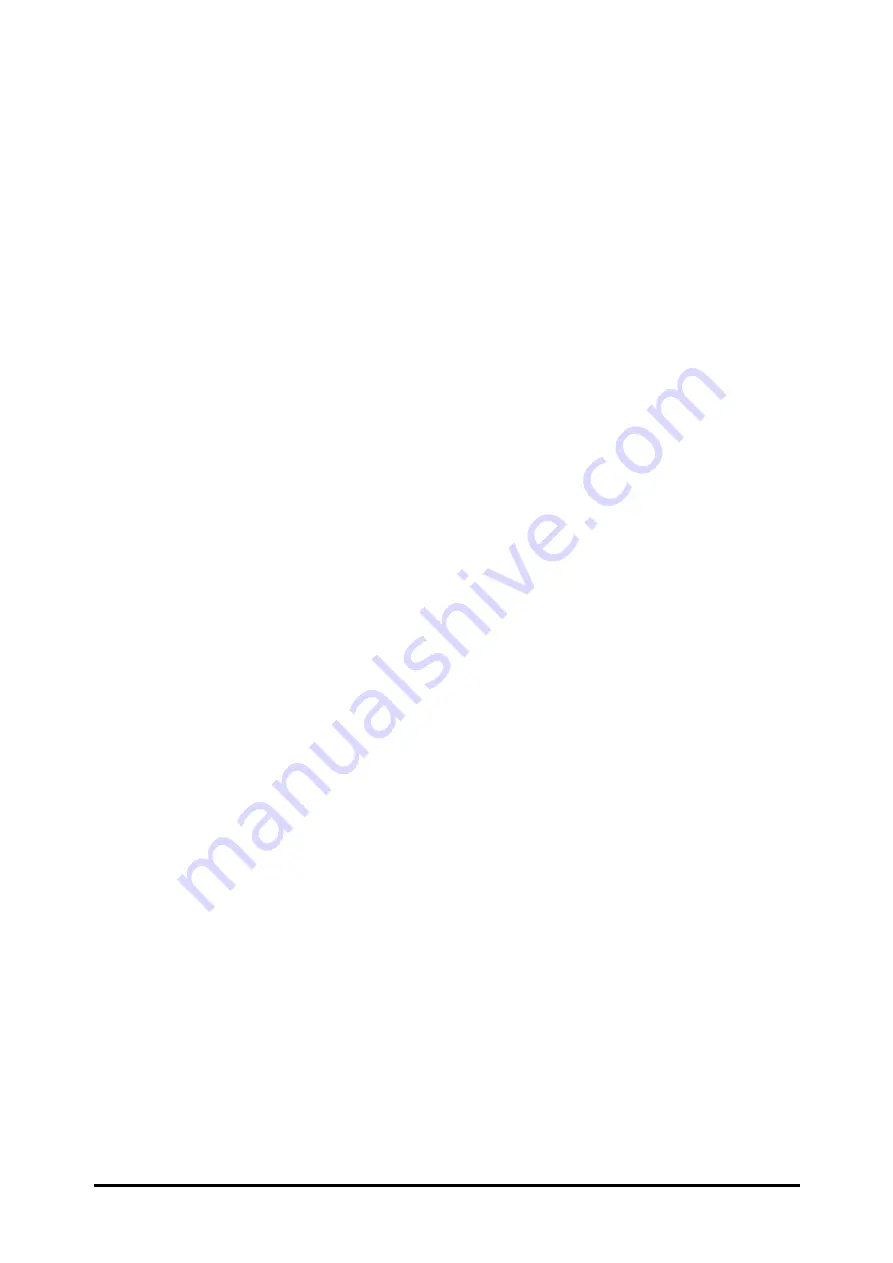
Move the hang point piece along the keel to adjust the hang point position. The nylon
locking rings must be fixed according to the chosen hanging point position (3 positions
available). Each position may be used. It only changes the cruising speed, without any
influence on stability and performance.
Warning: Any change in the hang point position means a variation of the A-frame angle
and therefore a different tension of the lower longitudinal cables. Various adjustment
holes are designed in the cable fixation U-shape rail at the nose of the wing, allowing
them to keep the correct tension according to the hang point position you choose.
For the normal forward setting of the hang point piece, the bolt that holds the swan catch
of the front inferior cables must be at the most reward hole on the rail. If the hang point is
moved backward, then the bolt must be moved forward.
Position of the pivot sleeves at the leading edges tips
The pivoting sleeves have been originally set to place the positioning marks glued on the
leading edge tube in front of the mark 0. Their differential rotation may be used for
correcting a tendency to turn on one side. They work in the same sense as ailerons on a
conventional aircraft – rotate the trailing edge down and more lift will be produced and
vice versa. If the wing pulls to the right, turn the left wing sleeve 2.5 millimeters
counterclockwise in order to increase the twist (), and the right wing sleeve
counterclockwise too, with the same value, in order to decrease the twist (toward -). For a
wing pulling to the left, turn the sleeves clockwise. If the correction is insufficient for
perfect wing adjustment, repeat the operation until you reach the correct adjustment.
Always proceed in the opposite direction on the sleeves of each half-wing. Separate the
strings holding the tip adjuster’s last straight batten and detach the Velcro patches joining
the upper and lower surfaces before rotating the sleeves and adjust the length of these
strings after pivoting in order to balance the tensions, and to limit the wrinkles in the
fabric, and to ensure the fit of the sleeve in its new position.
A coupled rotation ( or - on each side) of both sleeves changes speed and
stability in pitch. A maximum of 2.5 mm is suitable. Rotation in the positive direction
means slowing down and rotation in the negative direction means speeding up.
Sail tension
Modify the sail tension at the wing tip to counterweight any aging effects on the sail. To
perform this adjustment, remove the protective cap from the wing tips and rotate the bolt
placed at its end with a 10mm wrench. Put the cap back and readjust if necessary the
tension of the small ropes of the inner and upper surface last wing tip batten, because of
the modifications of the sail position on the leading edge tubes. Tense them with a
maximum of 5 turns (5mm) and control with a fly-test.
The leading edge tension can also be adjusted to correct a tendency to turn (if the sleeve
rotation has not completely corrected the problem. Increase the tension on the wing
which is trying to lift and decrease tension on the opposite wing, i.e. for a right turn
increase the tip tension on the left wing and decrease tension on the right wing. This is
done by removing the plastic end cap from the wing tips and rotating the 10mm bolt.
Proceed in adjustments of no more than 2.5 turns (2.5mm adjustment), with the same
value on both sides and then test the aircraft. This adjustment will change the tension of
the end batten strings. These must be re-tensioned before flying the aircraft.
GDMMIX13-1G Version
0010
35
Summary of Contents for IXess 13
Page 42: ......