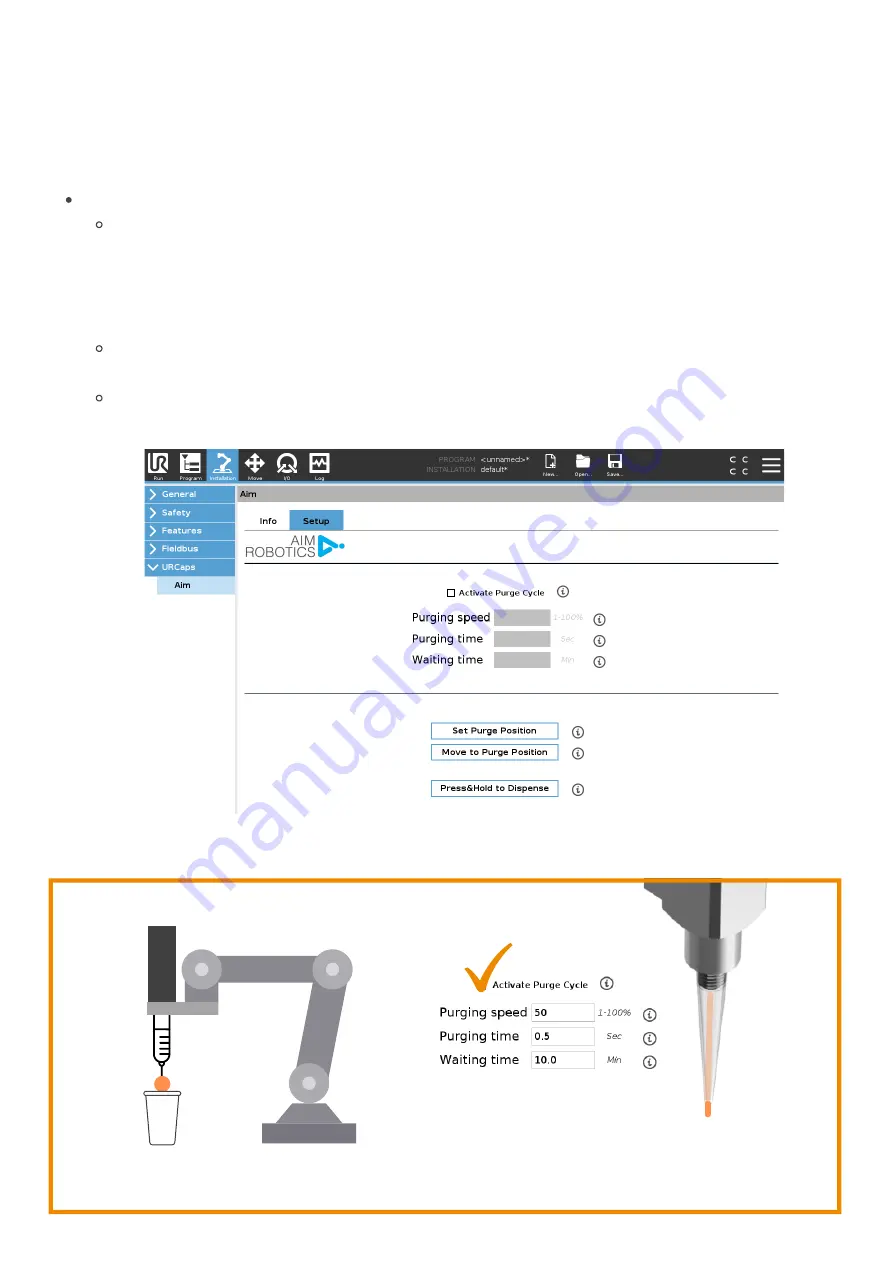
Select the Installation tab and select URCaps > Aim
In Setup you can activate the Purge Cycle and the connected inputs (Purging
speed, time and waiting time). These options are only available if the Purge
Cycle has been activated. The Purge Cycle is not part of the program and only
runs if the program is stopped and positioned over the Purge Position. This can
be useful if the unit has to stand for a longer period of time.
Use Set Purge Position to define the position the robot has to been in when
purging / cleaning.
Use Press and Hold to Dispense to dispense the fluid at startup to fill system
PROGRAMMING
Aim Installation Node / Purge Cycle
15
Purge Position
Dispenses for 0.5 seconds
every 10 minutes, when in Purge Position
Example