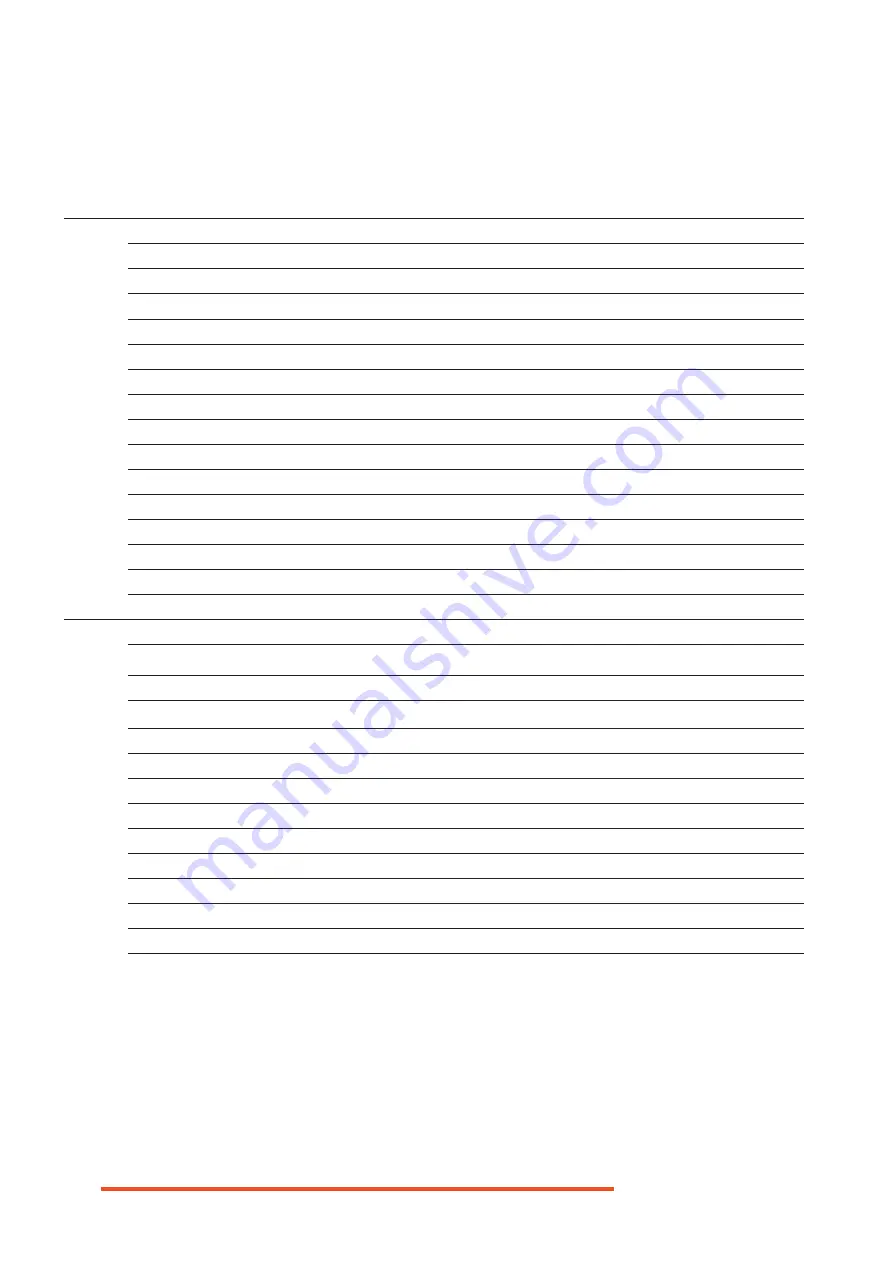
I-44
G-084383_EN • 03
P
roduct
I
nstallatIon
Art. Designation
Equivalent
length
Art. code
M&G T
win Pipe System 100 mm
Adaptor PP 150/100-100/100
TBD
41.008.57.22
Roof terminal skyline PP 100/100
TBD
41.008.48.53
Wall terminal mugro 100/100 incl. Wall plates
TBD
41.007.63.35
Extension PP 100x500 EPDM
TBD
41.008.54.81
Extension PP 100x1000 EPDM
TBD
41.008.54.82
Extension PP 100x2000 EPDM
TBD
41.008.54.84
Extension adjuster PP 100 EPDM
TBD
41.008.51.28
Elbow PP 100 90° EPDM
TBD
41.008.51.41
Elbow PP 100 45° EPDM
TBD
41.008.51.42
Support elbow PP 100 90° EPDM
TBD
41.008.51.45
Tee PP 100 90° + cover EPDM
TBD
41.008.51.46
Chimney top PP 100 + incl inox pipe
TBD
41.008.54.97
Support strip
TBD
41.008.74.37
Chimney shaft cover 100
TBD
41.008.74.13
Shaft distance holder PP 100 (2 pcs)
TBD
41.008.75.04
Wall bracket 100 PP
TBD
41.007.19.02
M&G Concentric System 100/150 mm
Roof terminal skyline std pp 100/150
TBD
41.008.48.62
Weather slate steep lead 100/150 25°-45°
TBD
41.008.79.13
Weather slate flat al 100/150 0°
TBD
41.008.73.79
Wall terminal mugro std 100/150 incl. Wall plates
TBD
41.007.63.43
Extension pp 100/150x 500 EPDM
TBD
41.008.43.51
Extension pp 100/150x1000 EPDM
TBD
41.008.43.52
Extension pp 100/150x2000 EPDM
TBD
41.008.43.54
Extension adjuster pp 100/150 EPDM
TBD
41.008.43.58
Elbow pp 100/150 90° short EPDM
TBD
41.008.43.60
Elbow pp 100/150 45° long EPDM
TBD
41.008.43.63
Tee pp 100/150 + cover EPDM
TBD
41.008.43.66
Chimney connection 100/150
TBD
41.008.43.78
Wall bracket 150
TBD
41.008.43.31
AIC-Approved Chimney Components
Summary of Contents for COILMASTER 100
Page 69: ...3 5 2 1 Fig 22 CM 100 120 Removing and Installing the Burner I 69 G 084383_EN 03 Maintenance...
Page 92: ...I 92 G 084383_EN 03 Declaration of Conformity...
Page 93: ...I 93 G 084383_EN 03 NOTES...
Page 94: ...www myaic eu AIC Europe B V Graafschap Hornelaan 163A NL 6001 AC Weert The Netherlands...